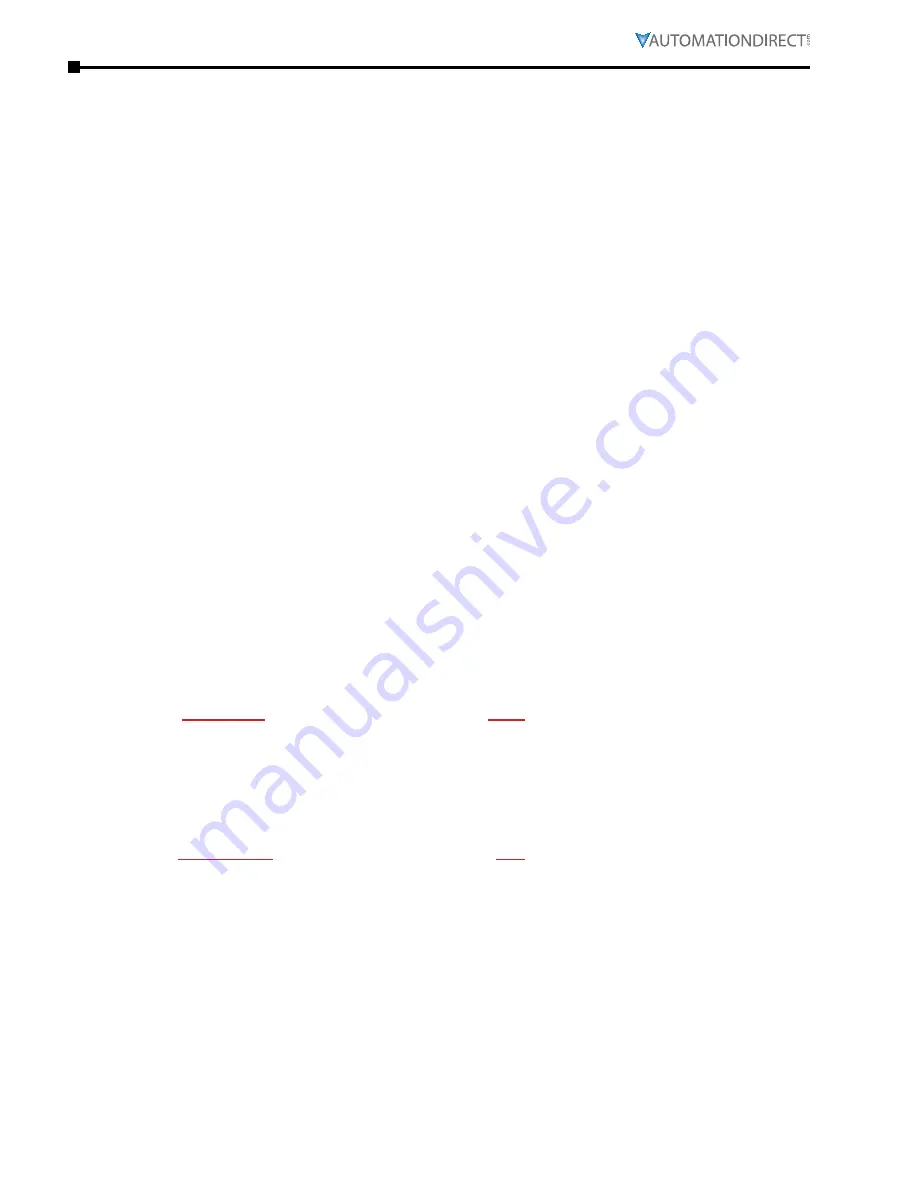
Page B–2
IronHorse® Helical Gearbox User Manual – 1st Ed. Rev. B
Appendix B: Gearbox Selection
Gearbox Selection Procedure
Gearbox Selection Steps
1) Determine the torque and speed required for the load.
2) Determine the overall speed ratio of motor speed to load speed.
3) Determine the gearbox ratio as well as any reduction outside the gearbox (pulleys, gears, etc.).
4) Determine the applicable service factor and overhung load K factor.
5) Determine the gearbox real output torque required, and select a gearbox with a higher
Maximum Thermal output Torque rating.
6) Determine the gearbox design output torque required (torque with service factor applied), and
select a gearbox with a higher Maximum Mechanical Output Torque rating. (Gearbox must also
meet requirement #5.)
7) Determine the required sizes of pulleys, gears, etc., and determine the overhung load force.
Select a gearbox with a higher Overhung Load rating. (Gearbox must also meet requirements
#5 & #6.)
8) Confirm that the selected gearbox meets the applicable system requirements.
9) Select a compatible motor.
Gearbox Selection Example
(Refer to the specifications tables for gearbox specifications, service factors, and K factors.)
A conveyor will run 8 hours/day with moderate shock loading. The conveyor will be driven by a
v-belt and needs to be driven approximately 30 rpm. The motor used will have a nominal speed of
1800 rpm (1750 rpm actual speed). The conveyor will require 5500 in-lb of torque.
1) Required torque = 5500 in-lb; required speed = 30 rpm.
2) Determine the overall speed ratio of motor speed to load speed:
Overall speed ratio = motor speed / load speed = 1750 / 30 = 58.33 (about 58:1)
3) Determine pulley ratios at available gearbox ratios:
Pulley ratio = (overall speed ratio) / (gearbox ratio)
For
5:1 gearbox:
pulley ratio = 58.33 / 5 =
11.67
[11.67 pulley ratio too large]
For 10:1 gearbox:
pulley ratio = 58.33 / 10 = 5.83
For 15:1 gearbox:
pulley ratio = 58.33 / 15 = 3.89
For 20:1 gearbox:
pulley ratio = 58.33 / 20 = 2.92
For 30:1 gearbox:
pulley ratio = 58.33 / 30 = 1.94
For 40:1 gearbox:
pulley ratio = 58.33 / 40 = 1.46
For
60:1 gearbox:
pulley ratio = 58.33 / 60 =
0.97
[0.97 pulley ratio too small]
Pulley ratio = (conveyor or pulley diameter) / (gearbox pulley diameter)
4) Determine service factor (SF) and overhung load factor (K) from applicable tables:
SF = 1.25
due to moderate shock loading and 3-10 hours/day operation
K = 1.5
due to V-belt
Содержание IronHorse HGR-37-005-A
Страница 1: ...IronHorse Helical Gearbox User Manual IH HG USER M WO 1st Ed Rev B...
Страница 2: ...IronHorse Helical Gearbox User Manual 1st Ed Rev B BLANK PAGE...
Страница 6: ...Page H 2 IronHorse Helical Gearbox User Manual 1st Ed Rev B BLANK PAGE...
Страница 32: ...Page A 4 IronHorse Helical Gearbox User Manual 1st Ed Rev B Appendix A Glossary of Terms BLANK PAGE...
Страница 37: ...IronHorse Helical Gearbox User Manual 1st Ed Rev B BLANK PAGE...
Страница 38: ...IronHorse Helical Gearbox User Manual IH HG USER M WO 1st Edition Revision B...