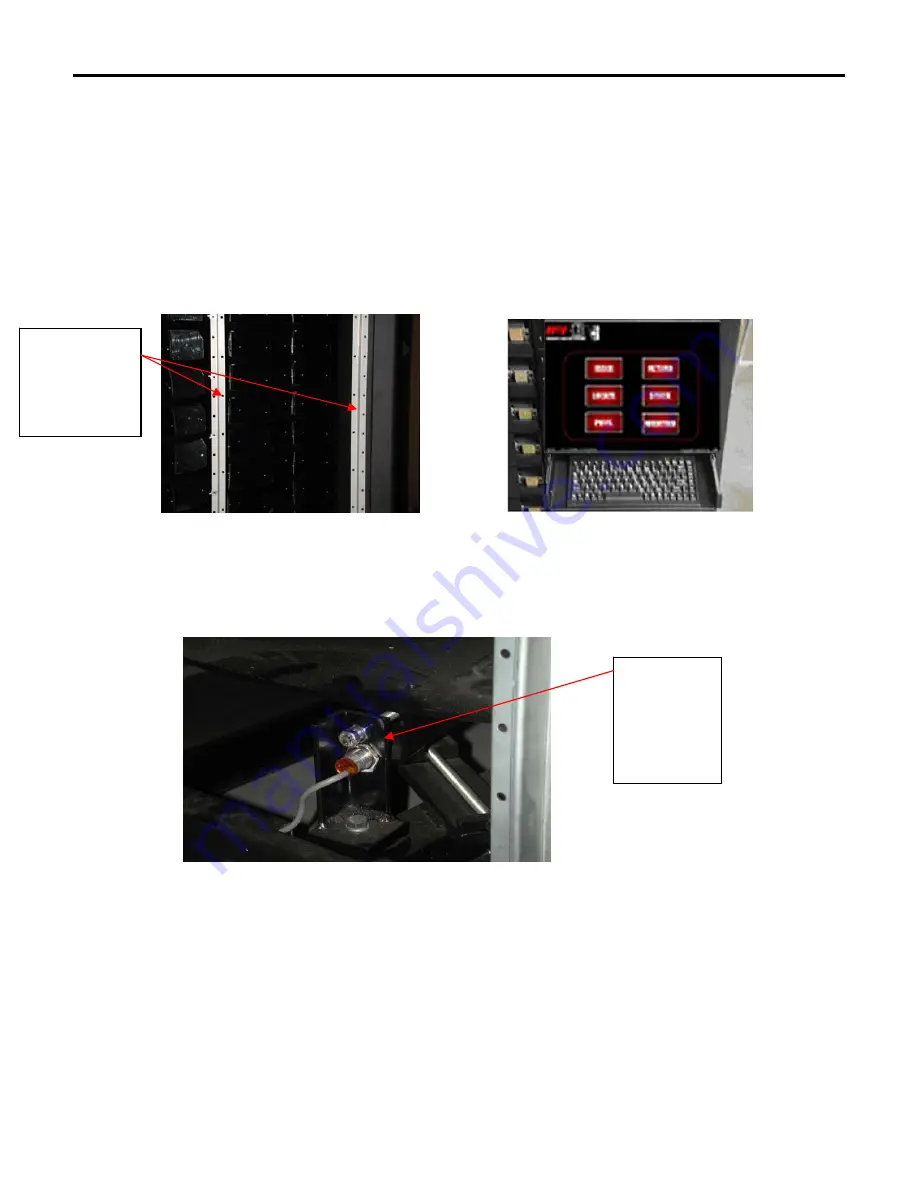
AUTO
CRIB
d.
The Display Assembly fits below the power panel and above the return tray assembly.
e.
Install the studs through the holes, attach, and tighten the 2 extended wing nuts and 2
nylocks from the backside. Install the extended wing nuts on the right of the computer
(while looking at the back of the PC). Install the nylocks on the left of the computer
using a 3/8 open end wrench.
f.
Attach the DB9 cable and AC plug to the outlets located on the bottom of the power
panel.
g.
Attach the Cat5 cable from the NIC card located at the top of the Display Assembly to
the hub provided by AutoCrib, Inc.
Mount display
Studs In Z
channel holes
here.
9.
Remove main platter locking bolt
a.
Bolt is located on the sensor bracket below bin door #1.
Remove bolt
before using
machine
using the 2 –
9/16 open end
wrenches.
b.
Loosen the lock nuts and unscrew the bolt using two 9/16 wrenches.
c.
Retain the bolt and nuts for possible future use.
Note: This bolt is inserted horizontally through the top of the bracket and into one of the radial arms on the main
platter. Do NOT loosen the bracket-mounting bolt, which holds the bracket down on the frame.
10.
Attach power and network services
a.
Uncoil the power cord and route it through the bottom of the frame.
b.
Attach power cord to a standard UPS (provided with the system) to a 120 VAC power
outlet – (max usage 4 Amps).
6