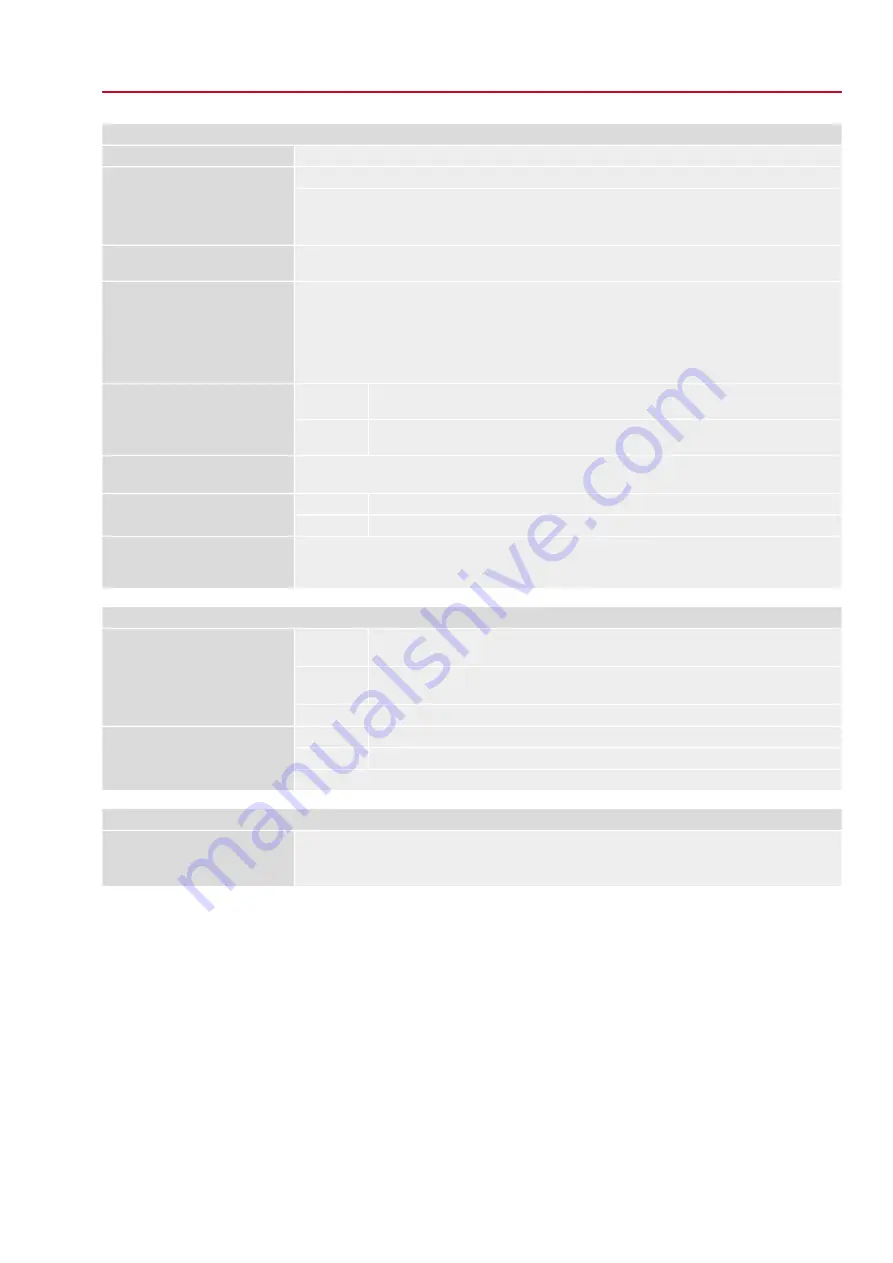
Service conditions
Up to 100 % relative humidity across the entire permissible temperature range
Humidity
IP68
Enclosure protection according to
EN 60529
According to AUMA definition, enclosure protection IP68 meets the following requirements:
●
Depth of water: maximum 8 m head of water
●
Duration of continuous immersion in water: Max. 96 hours
Pollution degree 4 (when closed), pollution degree 2 (internal)
Pollution degree according to
IEC 60664-1
FQM 05.1/07.1 with valve attachment F07 = 0.3 g, 10 to 200 Hz
FQM 05.1/07.1 with valve attachment F10 = 0.5 g, 10 to 200 Hz
FQM 10.1/12.1 with valve attachment F10 = 0.3 g, 10 to 200 Hz
FQM 10.1/12.1 with valve attachment F12 = 0.5 g, 10 to 200 Hz
Resistant to vibration during start-up or for failures of the plant. However, a fatigue strength may not be
derived from this.
Vibration resistance according to
IEC 60068-2-6
KS: Suitable for use in areas with high salinity, almost permanent condensation, and high
pollution.
Standard:
Corrosion protection
KX: Suitable for use in areas with extremely high salinity, permanent condensation, and
high pollution.
Option:
Double layer powder coating
Two-component iron-mica combination
Coating
AUMA silver-grey (similar to RAL 7037)
Standard:
Colour
Available colours on request
Option:
500 fail safe operations (ESD cycles)
AUMA fail safe units meet or even exceed the lifetime requirements of EN 15714-2 in motor operation.
Detailed information can be provided on request.
Lifetime
Special features for use in potentially explosive atmospheres
II 2G Ex db eb IIB T4 Gb, or
II 2G Ex d IIB T4 Gb
ATEX:
Explosion protection
Ex db eb IIB T4 Gb, or
Ex d IIB T4 Gb
IECEx:
For exact version, refer to actuator name plate.
DEKRA 16 ATEX 0080 X
ATEX:
Certificates and standards
IECEx DEK 16.0039X
IECEx:
All standards applied and their respective issues are indicated on the certificates supplied.
Further information
●
ATEX Directive: (2014/34/EU)
●
Electromagnetic Compatibility (EMC): (2014/30/EU)
●
Machinery Directive: (2006/42/EC)
EU Directives
33
FQM 05.1 – FQM 12.1 / FQMEx 05.1 – FQMEx 12.1
Technical data
Содержание FQM
Страница 35: ...35...