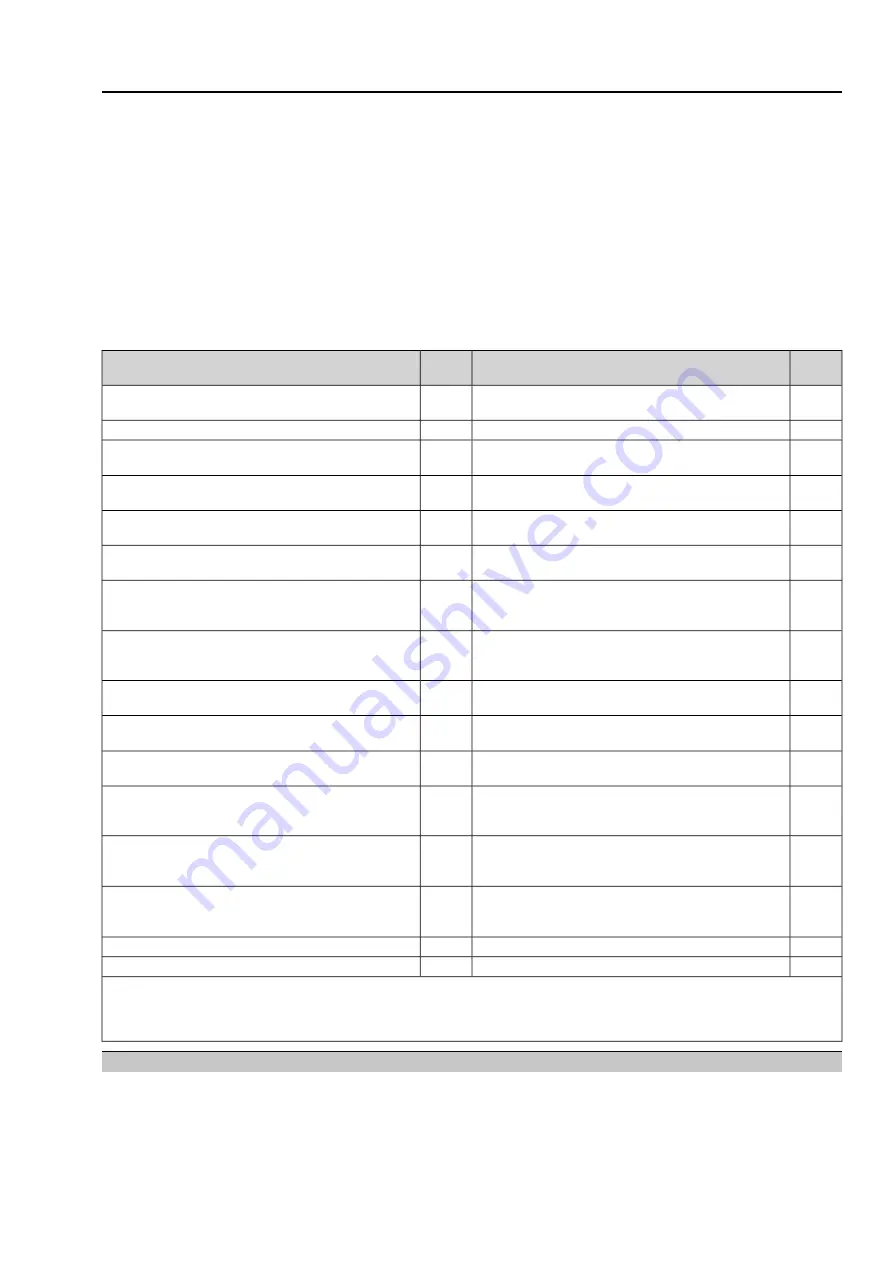
●
Actuators with electromechanical control unit or actuator with electronic control
unit and limit switches.
●
One of the following safety functions:
-
Safe ESD function “Safe CLOSING” (Safe ESD in direction CLOSE)
-
Safe ESD function “Safe OPENING” (Safe ESD in direction OPEN)
●
Configuration of “SIL seating”
= “no seating”
Also valid for combination of Safe ESD with Safe STOP.
Information
For version of electronic control unit with limit switches, steps 6 – 9 are obsolete.
Table 29: Checklist 9
✎
Configuration
Safe OPENING (Safe ESD in direction OPEN)
✎
Configuration
Safe CLOSING (Safe ESD in direction CLOSE)
⎕ ✓
1. Is actuator in mid-position or at sufficient distance
from the end positions?
⎕ ✓
1. Is actuator in mid-position or at sufficient distance
from the end positions?
⎕ ✓
2. Switch compartment opened?
⎕ ✓
2. Switch compartment opened?
⎕ ✓
3.
Safe ESDa
and
Safe ESDb
input signals
set to 0 V (low)?
⎕ ✓
3.
Safe ESDa
and
Safe ESDb
input signals
set to 0 V (low)?
⎕
Yes
⎕
No
➥
Check actuator reaction:
Safety operation initiated?
⎕
Yes
⎕
No
➥
Check actuator reaction:
Safety operation initiated?
⎕ ✓
4. Limit switch OPEN operated?
(Test button [2] turned in direction of the LSO arrow?)
⎕ ✓
4. Limit switch CLOSE operated?
(Test button [1] turned in direction of the LSC arrow?)
⎕
Yes
⎕
No
➥
Check actuator reaction:
Safety operation not stopped?
⎕
Yes
⎕
No
➥
Check actuator reaction:
Safety operation not stopped?
⎕ ✓
5.1
Safe ESDa
and
Safe ESDb
input signals
set to +24 V DC (high) prior to reaching the end pos-
ition?
⎕ ✓
5.1
Safe ESDa
and
Safe ESDb
input signals
set to +24 V DC (high) prior to reaching the end pos-
ition?
⎕ ✓
5.2 Actuator operated via local controls or from RE-
MOTE to end position OPEN and then to end position
CLOSED?
⎕ ✓
5.2 Actuator operated via local controls or from RE-
MOTE to end position OPEN and then to end position
CLOSED?
⎕ ✓
5.3 Actuator operated to mid-position or at sufficient
distance from the end positions?
⎕ ✓
5.3 Actuator operated to mid-position or at sufficient
distance from the end positions?
⎕ ✓
6.
Safe ESDa
and
Safe ESDb
input signals
set to 0 V (low)?
⎕ ✓
6.
Safe ESDa
and
Safe ESDb
input signals
set to 0 V (low)?
⎕ ✓
7. Torque switch OPEN operated?
(Test button [2] turned in direction of the TSO arrow?)
⎕ ✓
7. Torque switch CLOSE operated?
(Test button [1] turned in direction of the TSC arrow?)
⎕
Yes
⎕
No
➥
Check actuator reaction:
Safety operation not stopped?
Display illuminated in red?
⎕
Yes
⎕
No
➥
Check actuator reaction:
Safety operation not stopped?
Display illuminated in red?
⎕
Yes
⎕
No
➥
Check SIL module signal behaviour:
SIL fault signal?
SIL failure
output (NC contact) = closed)
⎕
Yes
⎕
No
➥
Check SIL module signal behaviour:
SIL fault signal?
SIL failure
output (NC contact) = closed)
⎕ ✓
8.
Safe ESDa
and
Safe ESDb
input signals
set to +24 V DC (high) prior to reaching the end pos-
ition?
⎕ ✓
8.
Safe ESDa
and
Safe ESDb
input signals
set to +24 V DC (high) prior to reaching the end pos-
ition?
⎕ ✓
9. Torque fault of standard controls acknowledged?
⎕ ✓
9. Torque fault of standard controls acknowledged?
⎕ ✓
10. Switch compartment closed?
⎕ ✓
10. Switch compartment closed?
☒ ✓
= Executed
☒ Yes
= Condition met
☒ No
= Condition not met
If the answer to one of the questions is no, the safety instrumented system must be checked.
11.2.9.
Safe STOP function – irrespective of the selected control unit
Proof test checklist for version or configuration:
“SIL function” = “Safe STOP OPEN/CLOSE” (safe stop) configuration.
Also valid for combination of Safe ESD with Safe STOP.
51
Part-turn actuators
with AC 01.2-SIL/ACExC 01.2-SIL
Checklists