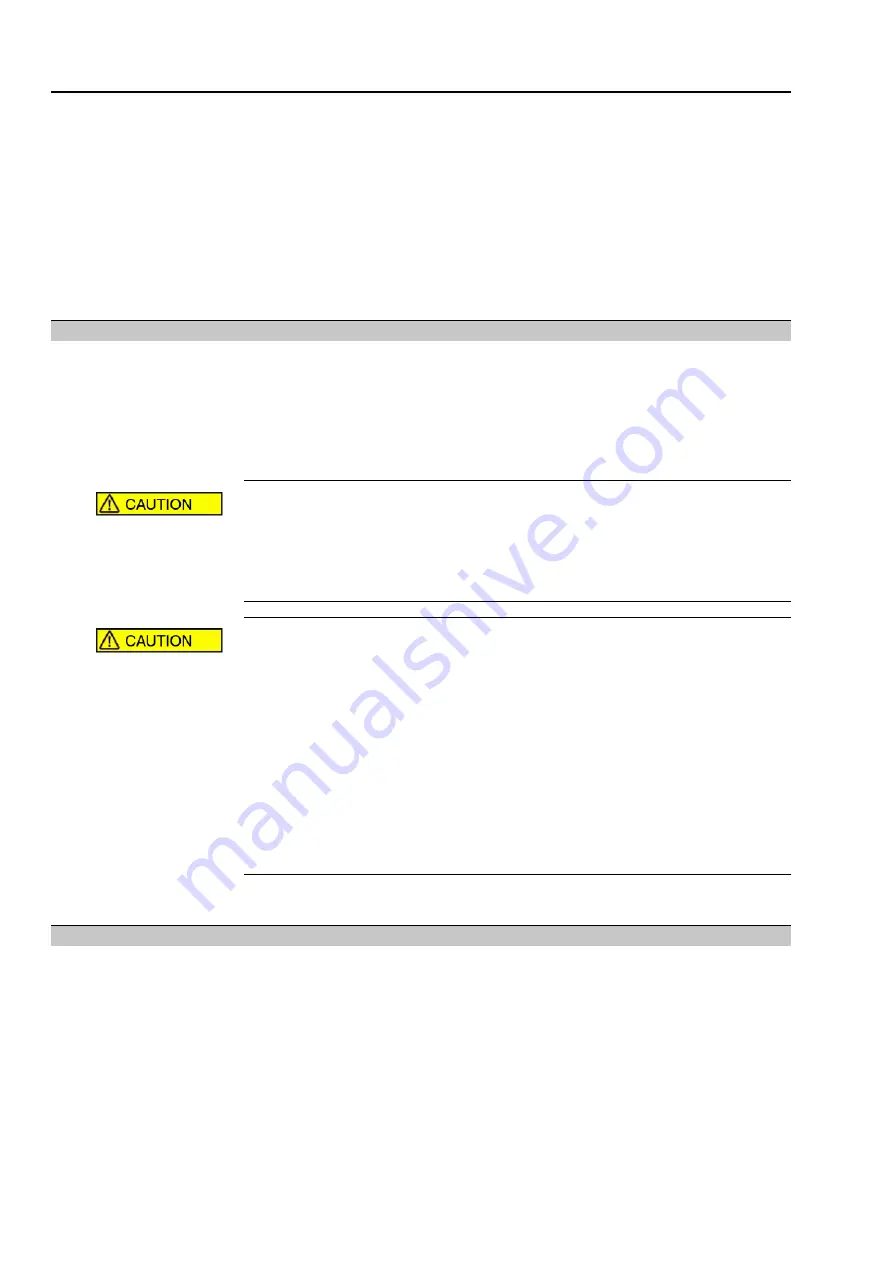
Information
The basic function "automatic correction of direction of rotation" is not available for
this version. When connecting the power supply ensure that phases L1, L2 and L3
are correctly connected. For checking the direction of rotation, refer to operation in-
structions pertaining to the actuator.
The "external supply of electronics" option of the actuator controls refers to standard
actuator controls. In case of mains failure, the SIL module would no longer be
operable despite external supply of the electronics.
Information
Limit switch setting for version with electronic control unit and SIL limit switches is
slightly different from the standard setting for the electromechanical control unit.
Refer to the supplement to operation instructions for correct setting (Y006.238).
5.2.
Commissioning
The operation instructions pertaining to the device must be observed for general
commissioning.
Information
For the Safe ESD function, operation into the safe position can be performed irre-
spective of the selector switch position (LOCAL - OFF - REMOTE) or the operating
status. Upon request of the safety function, the actuator will start operation even in
positions LOCAL and OFF or on system start.
Risk of immediate actuator start when switching on if the motor/handwheel
locking device was removed while the motor was in disengaged position!
Risk of personal injuries or damage to the valve
→
Ensure that high level is present at the
Safe ESDa/ESDb
inputs when
switching on (default: +24 V DC).
If the actuator is operated over a longer period (for several hours) while the
motor is disengaged, this entails considerable wear of the actuator. Worst
case would be accidental start-up or even destruction of the actuator.
On delivery, the motor is disengaged to prevent accidental start-up of the actuator
as well as consequential personal injuries or damage to the valve.
If the actuator is connected to 3-phase AC current without high level is present at
the
Safe ESDa/ESDb
inputs (default: +24 V DC), the motor will start without any
movement at the output drive.
→
Operational actions have to be provided ensuring that the described state only
persists for a short time, i.e. a few minutes at the maximum.
→
Remove the motor locking device prior to commissioning. It must only be used
for a short time during proof test.
After commissioning, the safe actuator function must be verified. Refer to <Proof
test> chapter.
5.3.
Operation
Regular maintenance and device checks in determined T
proof
intervals are the basis
for safe operation. The figures indicated in the <Safety figures> chapter are valid for
T
proof
= 1 year.
For operation, both the pertaining operation instructions and the Manual (Operation
and setting) AC 01.2/ACExC 01.2 have to be observed.
In case of possible failures or defects of the safety system, safe function must be
guaranteed by introducing alternative actions. Furthermore, a detected fault including
fault description has to be sent to AUMA Riester GmbH & Co. KG. Autonomous
repair work by the plant operator is not permitted.
20
Part-turn actuators
Installation, commissioning and operation
with AC 01.2-SIL/ACExC 01.2-SIL