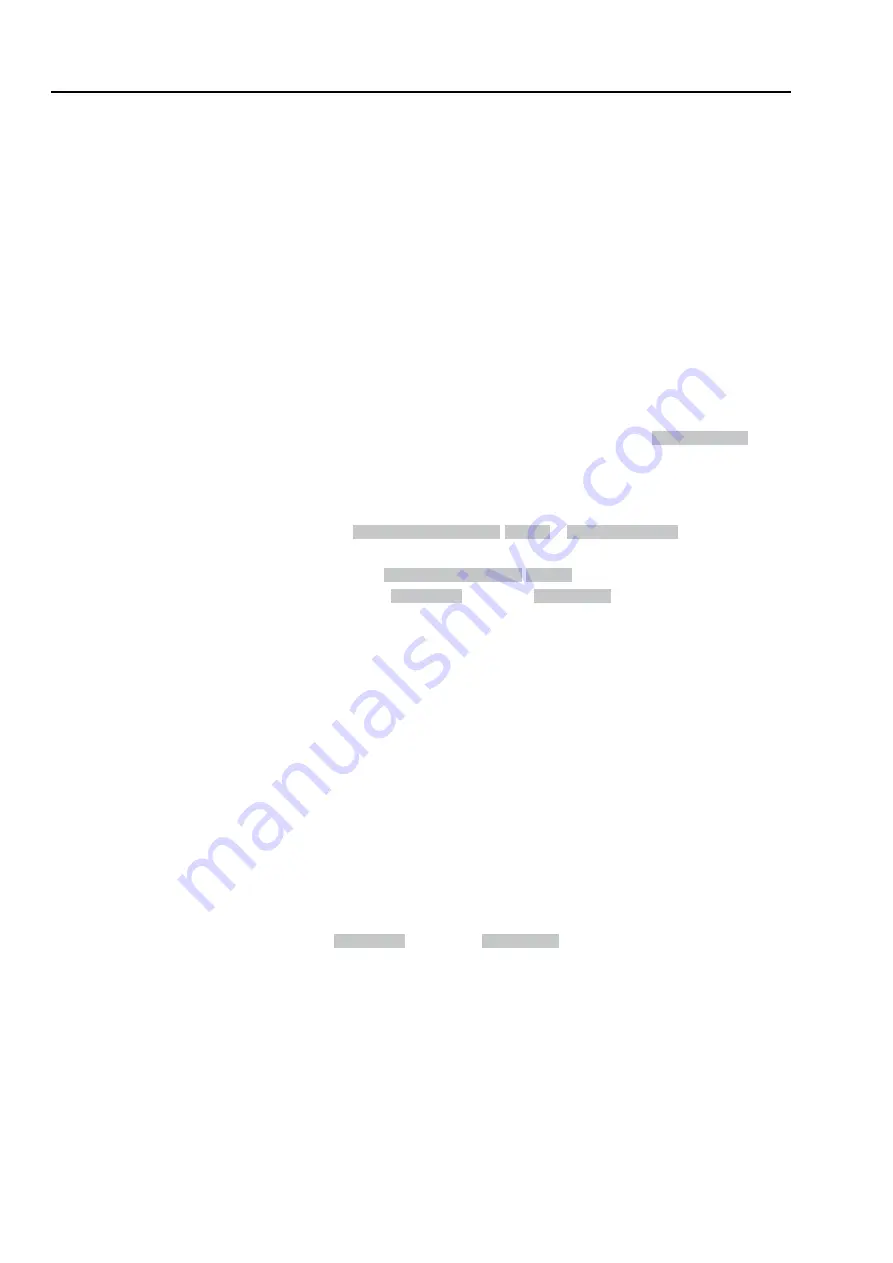
1.
Performing the PVST using safe inputs
Safe ESDa
and
Safe ESDb
:
The PVST must be controlled by the external safety PLC. The safety PLC uses
safe inputs
Safe ESDa
and
Safe ESDb
. Desired diagnostics is performed
by evaluating the SIL output contact (SIL module:
SIL failure
). Both control
signals and related actuator operation have to be present for at least 4 seconds.
The test is successfully passed if both control signals and the pertaining actu-
ator operation are present for at least 4 seconds without fault signal from the
SIL output contact (SIL module:
SIL failure
). Otherwise, the device has
to be checked in accordance with the steps indicated in the <Proof test: execute>
chapter.
2.
Performing the PVST using the PVST function of AC .2:
If the standard AC .2 actuator controls are configured with PVST input, this input
can be used for diagnostics of the safety-relevant part of actuator controls under
certain conditions.
Conditions and required settings:
-
Additional non-interacting end position switches for safe and reliable end
position feedback signals are available and wired to the safety PLC.
-
A digital input of standard actuator controls (galvanically separated from
the other inputs) is configured to the following value:
Execute PVST
(949),
or PVST control using an available fieldbus interface.
-
The safety PLC directly controls the PVST or will also receive the control
signal if the PVST input is controlled.
-
The PVST is performed with the following operation mode setting: Para-
meter
PVST operation mode M0889
=
End position test
-
The PVST may only be performed from one of the end positions.
-
Parameter
PVST operating time M0890
must amount to > 4 seconds.
-
The signals
PVST fault
(953) and
PVST abort
(954) of the standard actu-
ator controls are signalled to the safety PLC via digital outputs of the
standard actuator controls or from the BPCS-PLC when using a fieldbus
interface. For this, imperatively apply appropriate measures to ensure the
absence of interference to the safety instrumented system (safety PLC).
PVST is either directly requested at the PVST input of the standard actuator
controls by the safety PLC or the signal for requesting the PVST is also sent
to the safety PLC. While the AC.2 standard actuator controls perform the PVST,
the safety PLC monitors whether
-
the actuator was in one of the end positions prior to the PVST (check via
safe end position feedback).
-
the actuator left one of the end positions within the set PVST operation
time (check via safe end position feedback).
-
the actuator has returned to the correct end position after completing the
PVST (check via safe end position feedback).
-
If a fault was signalled via the SIL output contact (SIL module:
SIL
failure
).
Only if the actuator was in one of the end positions prior to the PVST, has left
this end position during the PVST, the standard actuator controls have neither
issued a
PVST fault
(953) nor a
PVST abort
(954) signal from standard actuator
controls, nor the SIL module signalled a
SIL fault
, was the PVST success-
fully completed. If this is not the case the device has to be checked in accord-
ance with the steps in the <Proof test> chapter.
Note: “Safe end position feedback” includes the end position switches which
are directly wired to the customer output and assessed by AUMA within the
framework of a Declaration of Incorporation for functional safety (SFC). These
switches are not part of the TÜV certification. Contrary to the output of the
standard actuator controls, they can be integrated within the safety instrumented
system.
28
Part-turn actuators
Tests and maintenance
with AC 01.2-SIL/ACExC 01.2-SIL