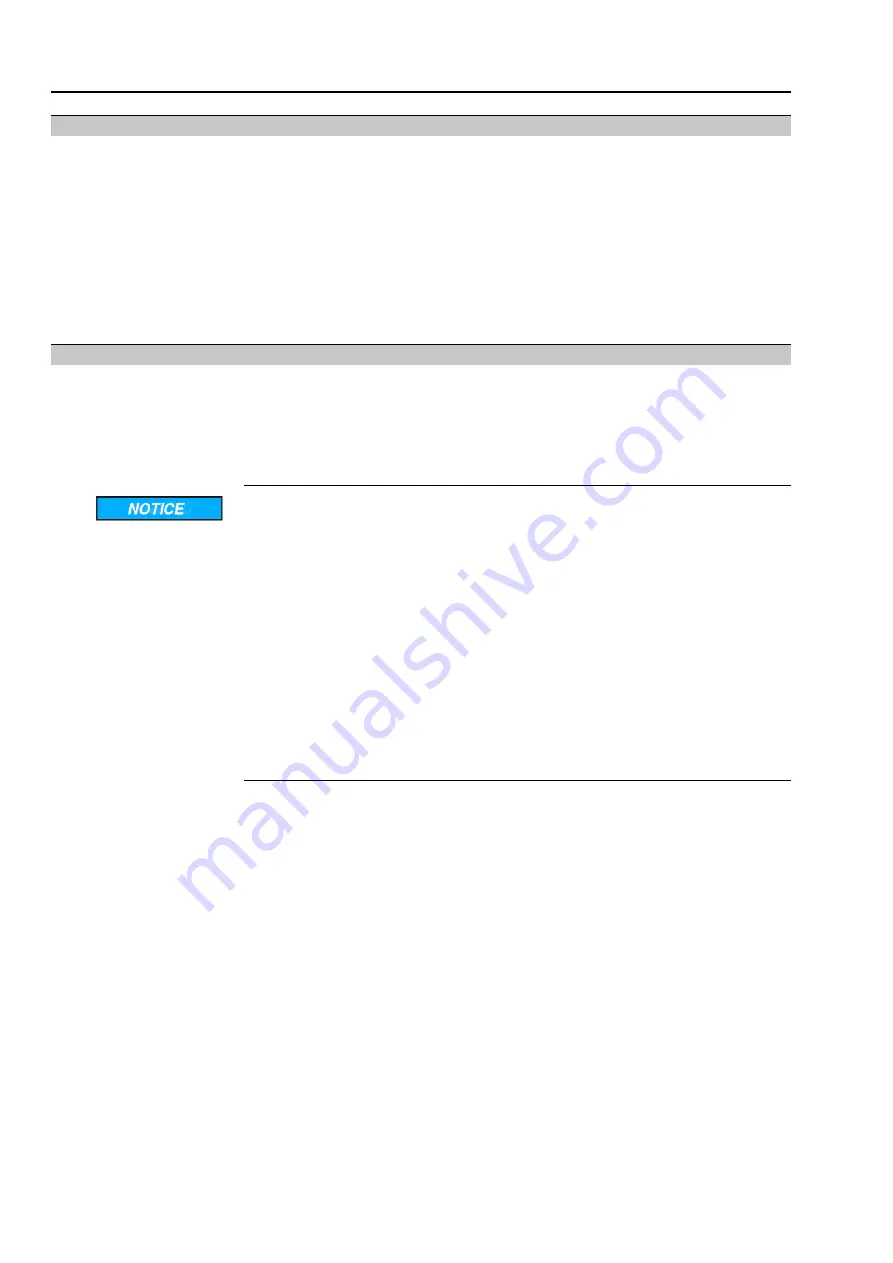
8.4.1.
Preliminary test
The actuator system has to be subjected following inspections first:
Test procedure
●
Visual inspection:
-
Visual inspection for external damage and corrosion.
-
Check electrical and mechanical connections.
●
Function check
●
Operate actuator at least once from CLOSED to OPEN and back (or vice versa).
-
During this operation, monitor actuator for conspicuous noise and sluggish-
ness.
-
Check whether both end positions are reached and signalled as expected.
8.4.2.
Check Safe ESD safety operation “Safe OPENING/CLOSING”
Configuration
The test is valid for all versions with Safe ESD function (irrespective of the “SIL
seating configuration”). The Safe ESD reaction to the different seating types is verified
in separate tests.
Test procedure
When switching the
Safe ESDa/Safe ESDb
inputs accordingly, safety operation
into the configured direction must be triggered.
If "SIL seating = no seating" (without end position protection) is configured,
faulty operation during the test may result in damage to the elements within
the safety-related system.
Possible consequences: Valve damage, motor overheating, contactor jamming, de-
fective thyristors, heating up or damage to cables.
→
Check “SIL seating” before proof test configuration. The configured type of
seating is indicated in the wiring diagram (page 2).
→
For actuators with “SIL seating” = “no seating”: Interrupt safety operation be-
fore reaching the end position (Set
Safe ESDa/Safe ESDb
input signals
to +24 V DC).
→
For the test, the valve should either be in mid-position or at sufficient distance
from the end positions.
→
In case of damage, the actuator system has to be checked and repaired, if ne-
cessary.
Test sequence
1.
Operate actuator in mid-position or at sufficient distance from the end positions.
2.
Execute operation command in opposite direction of the configured Safe ESD
safety function:
→
For “Safe CLOSING” (Safe ESD in direction CLOSE) configuration:
Start operation command in direction OPEN.
→
For "“Safe OPENING” (Safe ESD in direction OPEN) configuration:
Start operation command in direction CLOSE.
Information: For the test, operation commands (in directions OPEN or CLOSE)
can be executed both from remote (via DCS) and from Local at the controls
(via the push buttons of the local controls).
3.
Start safety operation during operation:
→
Set
Safe ESDa
and
Safe ESDb
input signals to 0 V (low).
➥
Safety function is correct if the actuator stops and performs a safety operation
into the configured direction up to the end position.
➥
No SIL fault signal may be issued.
4.
Set
Safe ESDa
and
Safe ESDb
input signals to +24 V DC (high) after the
test.
30
Part-turn actuators
Tests and maintenance
with AC 01.2-SIL/ACExC 01.2-SIL