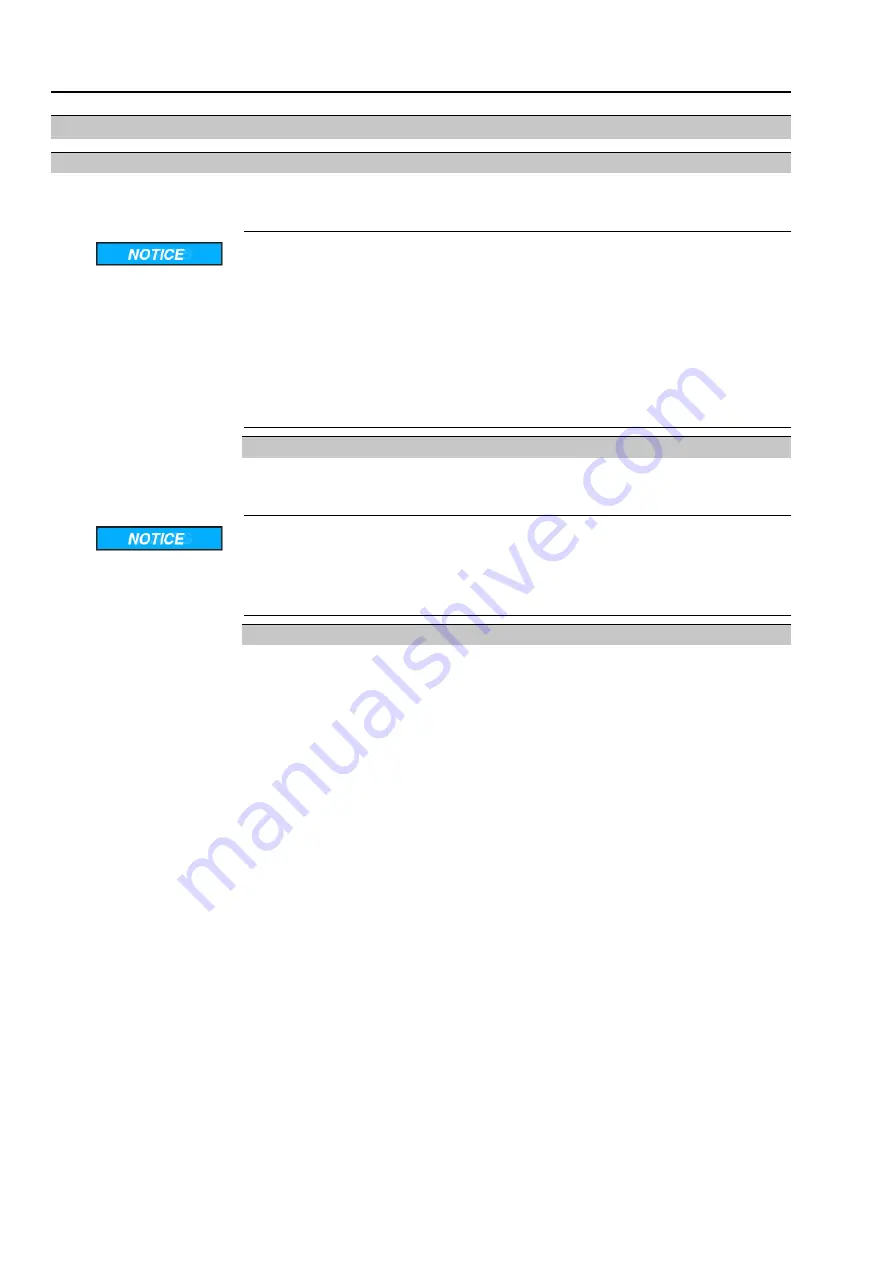
3.
Architecture, configuration and applications
3.1.
Architecture (actuator sizing)
For actuator architecture (actuator sizing) the maximum torques, run torques and
operating times are taken into consideration.
Incorrect actuator architecture can lead to device damage within the safety-
related system!
Possible consequences: Valve damage, motor overheating, contactor seizure,
damage to the electronics, heating up or damage to cables.
→
The actuator technical data must imperatively be observed when selecting the
actuator.
→
Sufficient reserves have to be provided to ensure that actuators are capable of
reliably opening or closing the valve even in the event of an accident or under-
voltage.
Architecture when using the Safe STOP function
Information
For the Safe STOP function, the motor is switched off, overrun may possibly occur!
Valve damage due to overrun!
→
For the Safe STOP function (SS), the overrun of the arrangement (actuator,
gearbox, valve) and the reaction time have to be observed.
→
If the application requires self-locking of the actuator, please consult AUMA.
Architecture when using the Safe ESD function
Actuators with electromechanical control unit:
The end position feedback (limit switching) and the torque signal of the
electromechanical control unit are safe signals, which can be integrated into a
safety-related system if they are directly wired to the XK customer output of the
actuator controls. However, this signal is not part of the certification by TÜV Nord.
Please refer to the specific safety manual for details regarding this signal.
For “SIL seating” = “no seating” (without end position protection), we recommend:
●
To prevent valve damage during safety operation, we recommend, depending
on the stiffness, sizing the valve to 3 – 5 times the maximum actuator torque.
●
To avoid thermal damage due to excessive currents, we recommend monitoring
(assessing) the motor protection.
Actuators with electronic control unit MWG:
Information
The end position feedback (limit switching) and the torque signal of the electronic
control unit MWG as well as all signals via the standard I/O interface and the fieldbus
interfaces are no safe signals.
●
In case safe signals are required, they have to be implemented differently, e.g.
using switches on the valve.
●
To prevent valve damage during safety operation, we recommend, depending
on the stiffness, sizing the valve to 3 – 5 times the maximum actuator torque.
●
To avoid thermal damage due to excessive currents, we recommend monitoring
(assessing) the motor protection.
Actuators with electronic control unit MWG including limit switches:
Information
In this version, safe signalling can exclusively be ensured via limit switches if they
are directly wired to the XK customer output of the actuator controls. However, this
signal is not part of the certification by TÜV Nord. Please refer to the specific safety
manual for details regarding this signal.
8
Part-turn actuators
Architecture, configuration and applications
with AC 01.2-SIL/ACExC 01.2-SIL