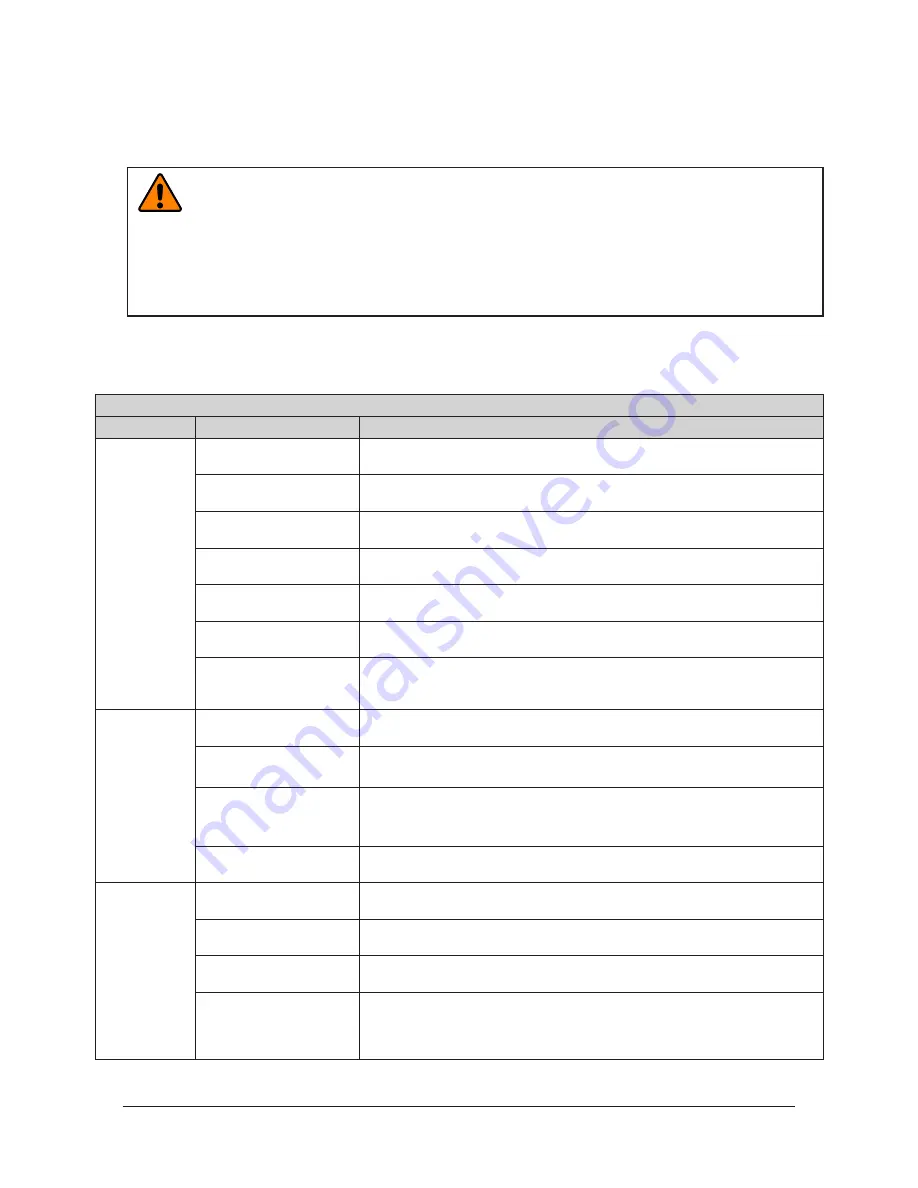
Manual, Control Module, PROFINET, DL10
Document #9620-20-C-DL10-04
Pinnacle Park • 1031 Goodworth Drive • Apex, NC 27539 • Tel: 919.772.0115 • Fax: 919.772.8259 •
C-41
6. Troubleshooting and Service Procedures
The following section provides troubleshooting information to help diagnose conditions with the Tool Changer or
Utility Coupler and service procedures to help resolve these conditions.
WARNING:
Do not perform maintenance or repair(s) on the Tool Changer or modules unless
the Tool is safely supported or placed in the tool stand, all energized circuits (e.g. electrical,
air, water, etc.) are turned off, pressurized connections are purged and power is discharged
from circuits in accordance with the customer’s safety practices and policies. Injury or
equipment damage can occur with the Tool not placed and energized circuits on. Place the
Tool in the tool stand, turn off and discharge all energized circuits, purge all pressurized
connections, and verify all circuits are de-energized before performing maintenance or
repair(s) on the Tool Changer or modules.
6.1 Troubleshooting
Refer to the following table for troubleshooting information.
Table 6.1—Troubleshooting
Symptom
Possible Cause
Correction
Unit will not
lock or unlock
Debris caught between the
Master and Tool plates.
Clean debris from between Master and Tool plates. Verify mounting fasteners is
secure and does not protrude above the mating surfaces.
Ball bearings are not
moving freely.
Verify that ball bearings are moving freely. Clean and lubricate as needed.
Refer
to the Maintenance section of the Tool Changer manual for instructions.
Air supply not to
specifications.
Check air supply.
Refer to Pneumatic Connection section of the Tool Changer
Manual
for specifications.
Exhaust port is not
properly vented.
Check that exhaust port is properly vented.
Refer to Pneumatic Connection
section of the Tool Changer Manual for valve requirements.
Incorrect valve operation.
Check valve for proper operation.
Refer to Pneumatic Connection section of the
Base Tool Changer Manual for valve requirements.
Signals are mapped
incorrectly.
Verify that signals are mapped and are communicating properly. Refer to
for electrical schematic.
Master and Tool are within
the specified No‑Touch
zone.
Verify that the Master and Tool are within the specified No‑Touch zone when
attempting to lock.
Refer to the Operation Section of the Tool Changer manual
for specifications.
Sensors not
operating
properly (but
PROFINET
is operating
correctly).
Sensor cables damage or
incorrectly connected.
Verify that cables are connected correctly and not damaged, replace if
damaged.
Refer to the Troubleshooting Section of the Tool Changer manual.
Sensors are not set
correctly.
Verify that the sensors are set correctly.
Refer to the Troubleshooting Section of
the Tool Changer manual.
Tool plate is not secured
properly or debris is
trapped between surfaces.
Ensure that the Tool plate is securely held to the Master plate, that nothing is
trapped between their surfaces.
Air trapped in the unlock
(U) air port.
Ensure that there is no air trapped in the Unlock (U) air port.
Refer to Pneumatic
Connection section of the Tool Changer Manual for valve requirements.
Loss of
communication
Contaminated or loose
cable connections.
Ensure all cable connections are clean and tight.
Damaged signal cabling
Check/replace signal cabling upstream and downstream of Tool Changer
modules.
Worn or damaged contact
pins
Inspect module contact pins for debris/wear/damage. Contact ATI for contact
pin replacement.
Product upstream
and downstream of
Tool Changer failed or
damaged
Check product upstream and downstream of Tool Changer for failure. This
failure can “appear” to be caused by the Tool Changer or affect Tool Changer
performance.