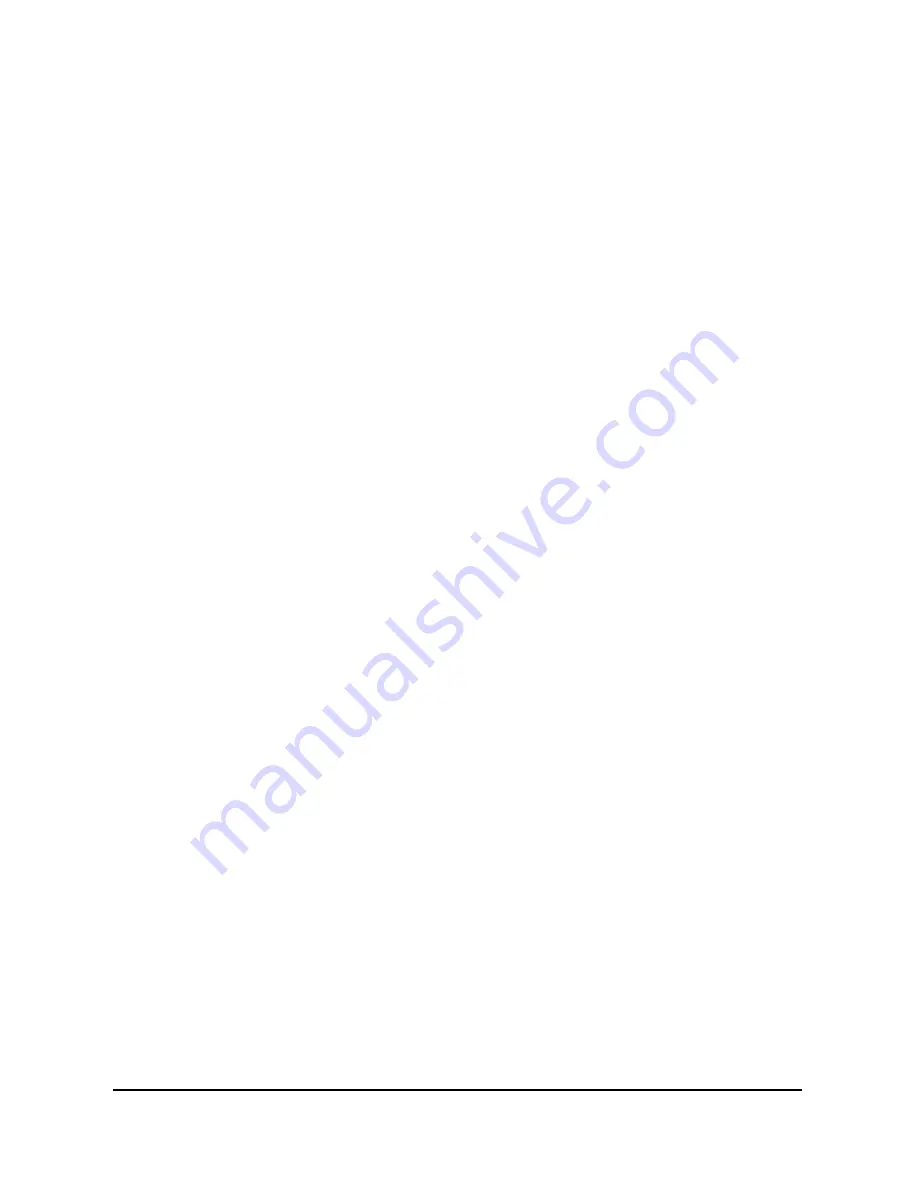
Installation and Operation Manual
Document #9620-20-b-mc-16 base tool changer-07
Pinnacle Park
•
1031 Goodworth Drive
•
Apex, NC 27539
•
Tel: 919.772.0115
•
Fax: 919.772.8259
•
www.ati-ia.com
•
Email: [email protected]
B - 5
Custom EIPs can be supplied by ATI to meet customer requirements (Refer to
Section 8—
for technical information on mounting features.).
When the customer chooses to design and build an End-effector Interface Plate, the following
should be considered:
•
The interface plate should be designed to include bolt holes for mounting, and dowel
pins for accurate positioning.
•
The thickness of the interface plate must be great enough to provide the necessary
thread engagement for the mounting bolts.
•
The plate design should take into account clearances required for Tool Changer
module attachments and accessories.
2.3 Optional Module Installation
The optional modules are typically installed by ATI prior to shipment. The following the steps
outlining the field installation and removal of optional modules.
2.3.1
Installing Optional Modules
1.
Clean the mounting surfaces.
2.
Align the module to the mounting flat as shown in
3.
If fasteners do not have pre-applied adhesive, apply Loctite 222
®
to the supplied
M3 Socket head cap screws. Install the (2) M3 socket head screws securing the
module to the Master or Tool plate and tighten to 7–10 in-lbs.
2.3.2
Removing Optional Modules
1.
Depending upon the service or repair being done, customer connections up to
the module may or may not need to be disconnected.
2.
Remove the M3 socket head cap screws and lift the module from the Master or
2.4 Tool Stand Design
In most cases, the Tools are stored in a Tool Stand when not being used by the robot. During
coupling and lock-up, the Tool Stand must allow for movement (float) in a plane parallel with
the mating surfaces of the Master Plate and Tool Plates (X and Y). This will help reduce wear
on alignment pin features and help to extend the life of the product.
Ideally, the Tool should be hanging vertically in the Tool Stand so that gravity helps to
uncouple the Tool Plate from the Master Plate during unlocking. It is possible to design Tool
Stands that hold tools in the horizontal position, but care must be taken that the necessary
compliance is provided during coupling and uncoupling. In general, “horizontal-position”
tool stands will cause more wear on the locking mechanism and locating features of the Tool
and Tool Stand.
Tool Stands may also need to incorporate means for covering Tools and electrical modules to
protect them in dirty environments, such as grinding or welding. Alternatively, locating Tool
Stands in areas shielded from weld spatter, fluids, adhesives, or other debris would eliminate
the need for Tool covers.
2.4.1
Tool Locating Features
The Tool should be positively and repeatably located in the Tool Stand. A variety
of methods may be used to accomplish this. A common method is to use tapered