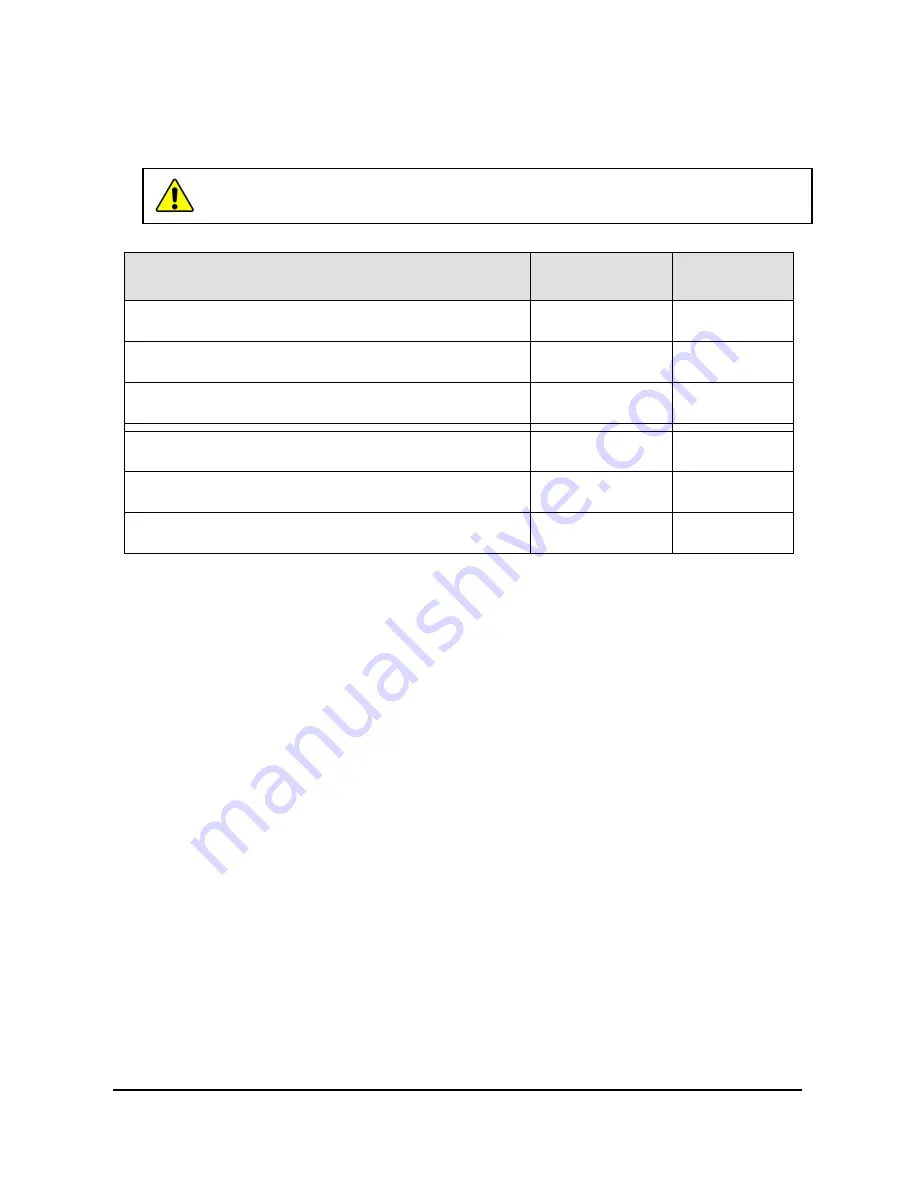
Installation and Operation Manual
Document #9620-20-b-mc-16 base tool changer-07
Pinnacle Park
•
1031 Goodworth Drive
•
Apex, NC 27539
•
Tel: 919.772.0115
•
Fax: 919.772.8259
•
www.ati-ia.com
•
Email: [email protected]
B - 4
All fasteners used to mount the Tool Changer to the robot and to user Tools should be tightened to a
torque value as indicated below. Furthermore, removable Loctite 222® must be used on M4 and M5
fasteners.
Mounting conditions
Fastener Size and
Property Class
Maximum
Recommended
Torque
Master Plate to interface plate (6061-T6 aluminum)
Minimum thread engagement of 6mm (0.24”) [1.5X fastener Ø]
M4–0.7
Class 12.9
12 in-lbs
Master Plate to Robot (steel
; USS ≥ 90KSI
)
Minimum thread engagement of 6mm (0.24”) [1.5X fastener Ø]
M4–0.7
Class 12.9
25 in-lbs
IP to Master Plate (6061-T6 aluminum) M5 threads into body
Minimum thread engagement of 7.5mm (0.30”) [1.5X fastener Ø]
M5–.8
Class 12.9
25 in-lbs
Tool Plate to TIP (6061-T6 aluminum)
Minimum thread engagement of 9mm (0.35”) [1.5X fastener Ø]
M4–0.7
Class 12.9
12 in-lbs
Tool Plate to TIP (steel; USS ≥ 90KSI)
Minimum thread engagement of 9mm (0.35”) [1.5X fastener Ø]
M4–0.7
Class 12.9
25 in-lbs
TIP to Tool Plate (steel) M5 threads into body
Minimum thread engagement of 7.5mm (0.30”) [1.5X fastener Ø]
M5–.8
Class 12.9
25 in-lbs
2.1 Master Interface
The Master assembly is attached to the robot arm. The Master Plate is designed with bolt
holes and dowel holes as mounting features. These features are used to accurately position
and secure the Master to the robot. An interface plate is utilized to adapt the Master Plate to a
specific robot flange that is not compatible with the Master Plate mounting features. Custom
interface plates are available upon request. (Refer to
Section 8—Drawings
information on mounting features.)
If the customer chooses to design and build a robot interface plate, the following should be
considered:
•
The interface plate should be designed to include bolt holes for mounting, and dowel
pins for accurate positioning on the robot and Master Plate.
•
The thickness of the interface plate must be great enough to provide the necessary
thread engagement for the mounting bolts.
•
The interface plate must be properly designed to provide rigid mounting to the
Master Plate boss area.
•
The plate design should take into account clearances required for Tool Changer
module attachments and accessories.
2.2 Tool Interface
The Tool Plate is attached to customer-supplied tooling. The Tool Plate is designed with bolt
and dowel holes as mounting features. These features are used to accurately position and
secure the end-effector. Most often an End-effector Interface Plate (EIP) is utilized to adapt
the Tool Plate to an end-effector that is not compatible with the Tool Plate mounting features.
CAUTION:
Care should be taken to select fasteners for mounting that are not too long,
such that a gap is formed at the interface