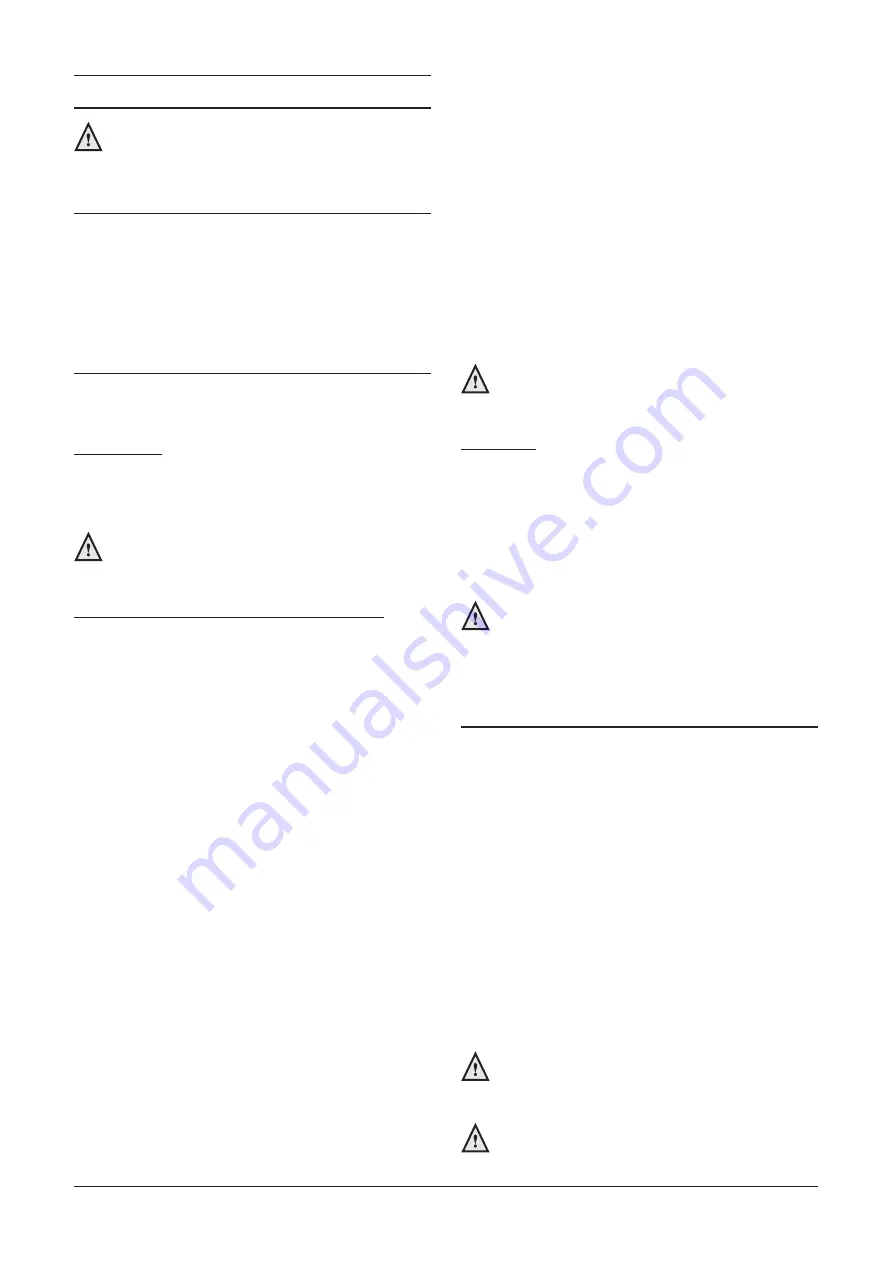
Installation instructions S-HR series page 24
14 Maintenance
Maintenance or changes to the unit may only
be carried out by an authorised technician.
14.1 The frequency of maintenance
We advise to carry out an inspection to the boiler every
two years and an overhaul every four years. When doing
this the circumstances of the boiler’s location must be
taken into account. From this one can determine whether
to deviate from this advice.
14.2 Maintenance activities
If it is necessary to clean the boiler the following actions
to the following components must be carried out:
The air boiler
Dirt which is sucked in by the air supply pipe will end up
in the bottom of the air box. This dirt can be cleaned with
a cloth with a simple (non-abrasive) cleaning agent.
Do not use an abrasive agent for cleaning,
this causes disturbing scratches in the air
box.
The burner ceramic bricks and heat exchanger
These components should only be cleaned if it is
determined that the maximum Pa is no longer obtained
as described in chapter 12.1.
The fan unit must be removed in order to be able to
inspect the heat exchanger. In this case the following
actions must be carried out:
-
close the gas valve and isolate the boilers electrical
supply;
-
turn the Control Tower forward around its left hinge
point and remove the plastic air box;
-
loosen the nut of the gas pipe under the gas block;
-
loosen the small crosshead screw on the red
electrical connection adaptor of the gas block;
-
remove the electrical connection plug from the fan
motor;
-
loosen the front crosshead screw of the black plastic
air inlet damper;
-
after this turn the two clamping rods ¼ turn and
remove them by pulling them forward;
-
slightly lift the fan unit and remove it towards the front
of the heat exchanger;
-
the fan unit and the air inlet damper can be checked
for contamination and if necessary cleaned;
-
now remove the burner ceramic bricks by slightly
lifting them upward and removing them in the same
direction as the heat exchanger fan unit;
-
the burner ceramic bricks and the heat exchanger
can be cleaned by means of a soft brush;
Refitting of the components is done in reverse.
The following components require extra attention during the
service procedure and when dismantling and reassenbling
the burner:
-
ensure that the orange gasket that fits around the
ceramic brick has not heat hardened or perished in
any way, if it has, it is essential that the gasket is
replaced before continuing to reassemble the boiler. If
in any doubt replace the gasket;
-
make sure that the burner gasket is fitted onto the heat
exchanger precisely;
-
make sure that the fan unit clamping rods have been
pushed backward sufficiently and that they have
again been turned ¼ turn;
-
make sure that the gas connection under the gas
block is tightened;
Following maintenance or other activities;
always check the installation of all parts through
which gas flows (using leak-search spray).
The siphon
In order to check the siphon for contamination the following
actions must be carried out:
-
make sure that the boiler is off by isolating the boilers
electrical supply;
-
turn the Control Tower forward around its left hinge point;
-
turn the siphon cup to the left until it is released from
the screw thread;
Do not use pliers or wrenches for removing
the siphon cup
Refitting is done in reverse order.
14.3 Further checks
Checking the ionisation current.
-
ionisation determines if there is a flame present with
correct combustion. The measurement is done by
means of connecting a micro Ampere gauge in series
with the ionisation thread. The minimum allowed
ionisation is 2 µA. The boiler will modify its load anyway
if the ionisation reaches the bottom limit of 2 µA.
Checking by means of a visual inspection.
-
A visual inspection entails viewing and checking of a
number of components with regard to their functioning.
The safety valve may not show any traces of leaks.
The waste trap should be clean.
The central heating water filter only requires
cleaning if the circulation pump is adjusted at maxi-
mum speed and the maximum
'
T is exceeded.
Following maintenance or other activities,
always replace the housing and secure it with
the screws.
Complete the Benchmark Service Record
Log Book as required and hand back to
customer.
Содержание Blauwe Engel S-HR 15
Страница 2: ......
Страница 15: ...Installation instructions S HR series page 15 electrical connecting diagram figure 11...
Страница 31: ...Installation instructions S HR series page 31 19 CE Certificate United Kingdom...
Страница 32: ...Installation instructions S HR series page 32 20 CE Certificate Ireland...
Страница 33: ......
Страница 34: ......
Страница 35: ......