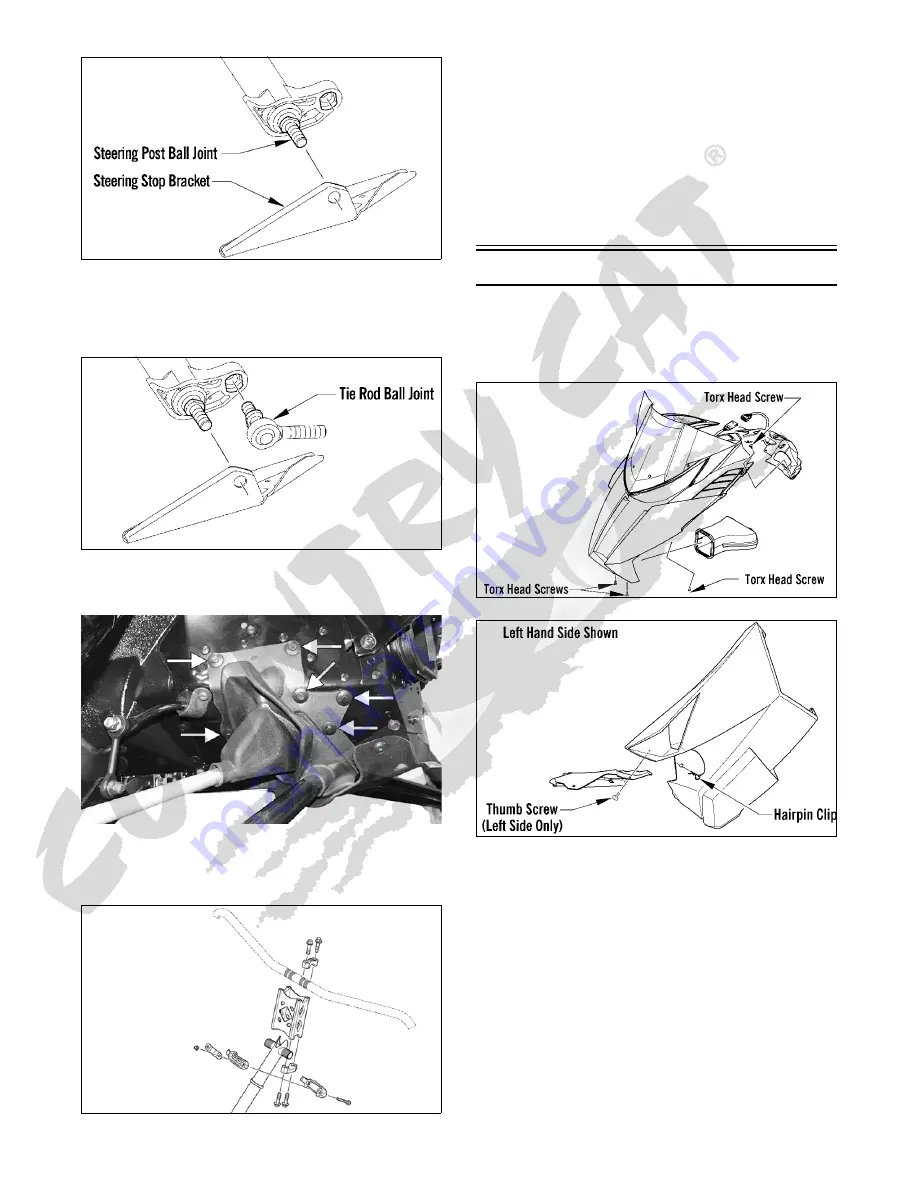
14
SNO-2218
2. Secure the tie rod assembly to the steering post using
a new M10 nut.
Be sure to align the tie rod ball
joint alignment tab with the steering post.
Tighten
to 35 ft-lb.
SNO-2219
3. Secure the right-side steering boot to the chassis
using the existing push rivets.
XM134A
4. Secure the top of the steering post to the steering
support using the existing retaining plate and nuts.
Tighten to 96 in.-lb.
SNO-357
5. Install the expansion chamber using the existing
springs; then connect the exhaust temperature sensor
to the main harness.
6. Position the hood onto the snowmobile and connect
the hood harness connector.
7. Secure the hood with the six torx-head screws and
tighten securely.
8. Install the access panels onto the lower console; then
close the access panels and secure with the clip.
Steering Post (XF HC/M)
REMOVING
To remove the access panel and hood, use the following
procedure:
0746-793
0746-800
1. Remove the hairpin clip from the pin located at the
front of the access panel; then unscrew the thumb
screw. Move the panel up and off the pin; then swing
the panel all the way out and unhinge the panel from
the lower console.
2. Remove all six torx-head screws securing the hood.
3. Locate the hood harness connector (located under the
center vent between the intake vents) and unplug the
connector; then move the hood slightly forward and
remove the hood.
4. Disconnect the exhaust temperature sensor from the
main harness; then remove all springs securing the
expansion chamber. Remove the expansion chamber.
Содержание 2014 XF 2-STROKE
Страница 1: ...SNOWMOBILE SERVICE MANUAL 2014 ZR XF M 2 STROKE...
Страница 3: ......
Страница 39: ...36 600_14_2...
Страница 47: ...44 800_12_2...
Страница 122: ...119 Troubleshooting Servomotor SERVO1A14...
Страница 123: ...120 SERVO2rv14...
Страница 152: ...149 0747 413 M Models...
Страница 196: ...Printed in U S A Trademarks of Arctic Cat Inc Thief River Falls MN 56701 p n 2259 956...