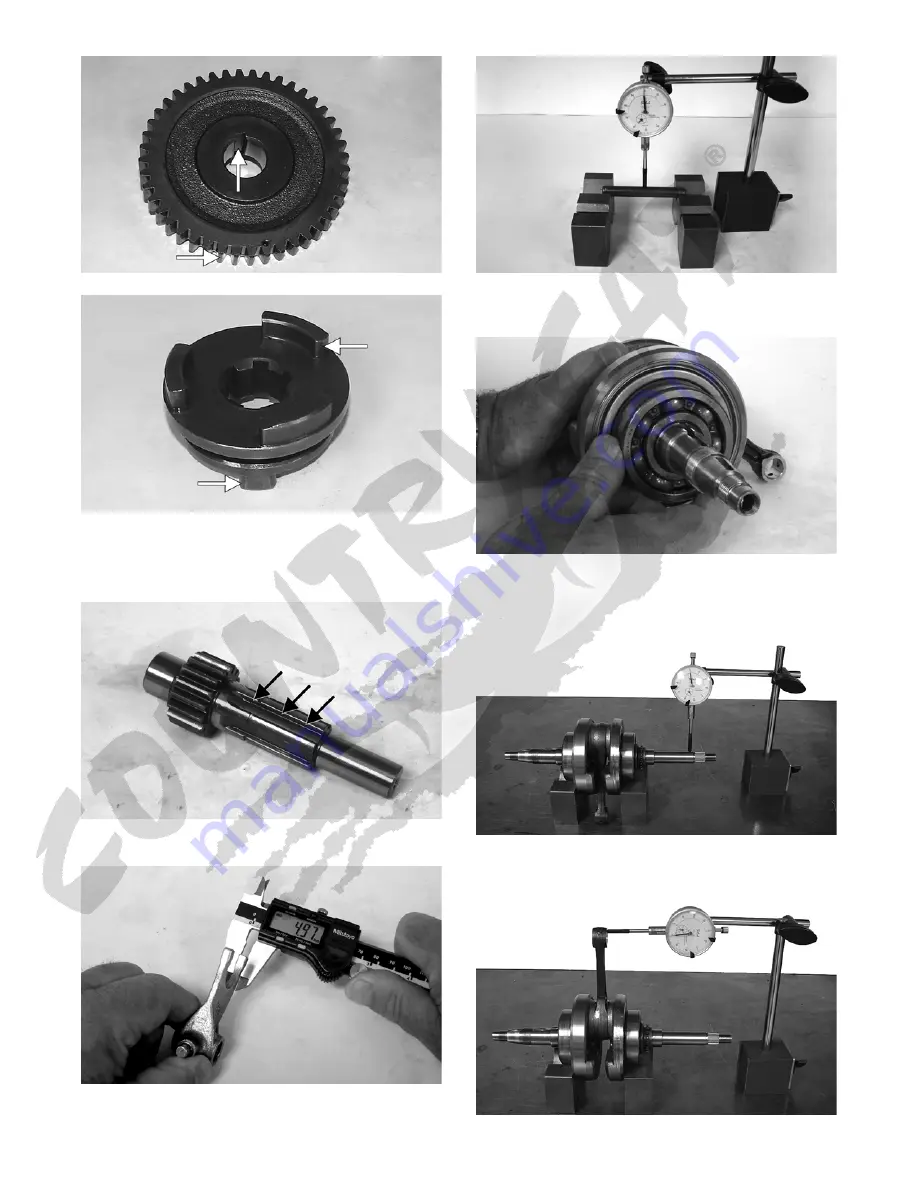
48
TR145A
TR142A
2. Inspect the transmission shafts, bushings, and bear-
ings for excessive wear or discoloration.
3. Check splines for excessive wear or twisting.
TR162A
4. Check shift fork for excessive wear or discoloration.
TR153
5. Check shift fork shaft for distortion. Maximum dis-
tortion (runout) must not exceed specifications.
TR155
6. Inspect crankshaft bearings for smoothness of turn-
ing and any signs of discoloration.
TR160
7. Using V-blocks and a dial gauge, check crankshaft run-
out. Maximum runout must not exceed specifications.
TR121
8. Check connecting rod small-end deflection. Maxi-
mum deflection must not exceed specifications.
TR122