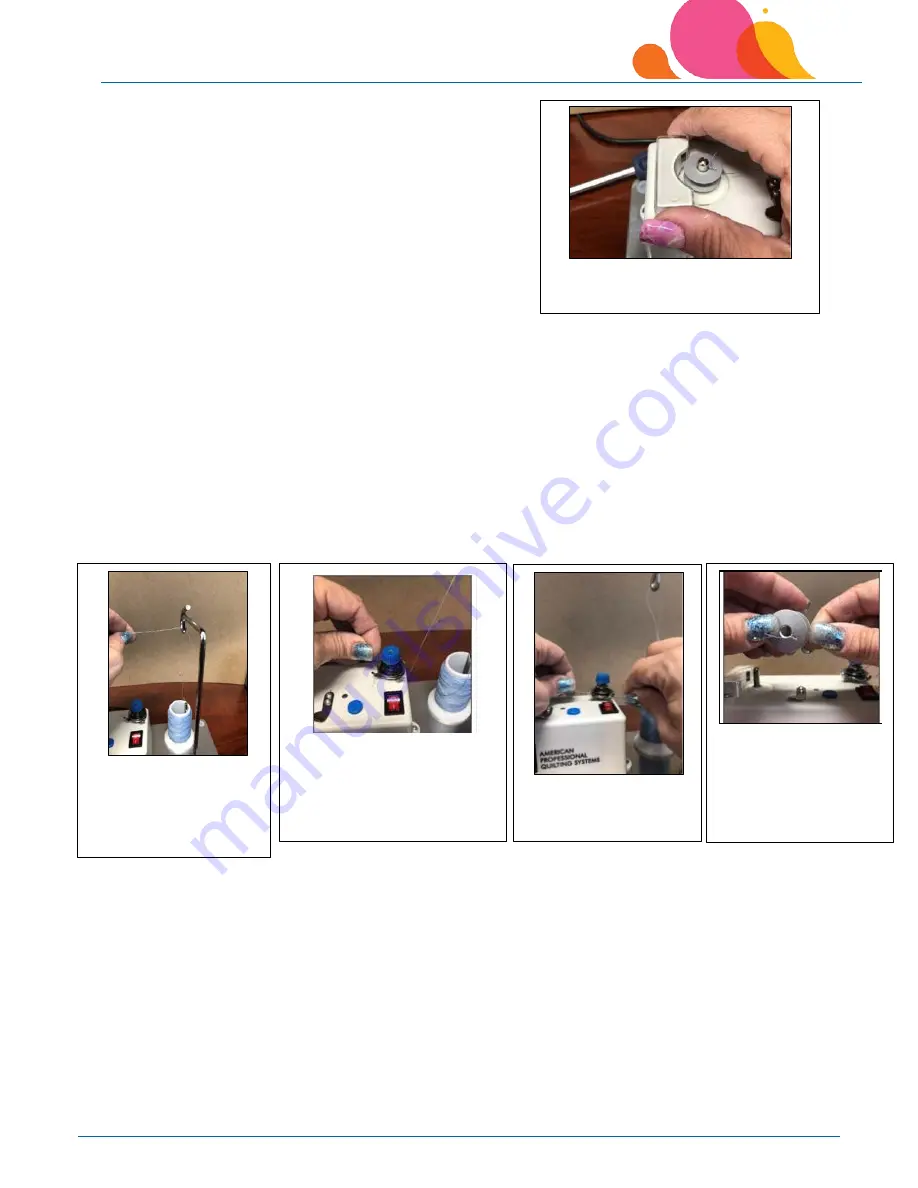
79
9-1-2022
APQS.com
Machine Operation
Once the screws have been loosened (about 2 full turns
counterclockwise is enough), move the sensor housing so
it is positioned similarly to the pictures on the previous
page. A final adjustment may be necessary once a bobbin
has been wound, but this is a good starting point.
Threading the Winder and Winding a Bobbin
Using a thread net on the cone is advised due to the speed that the thread will come off the cone. Once the
net is on the cone, pull the thread up through the tall stand, going from right to left as shown below, and
then down to the tension control. Start at the thread guide closest to the cone, and then wrap the thread
around the tension discs counterclockwise and through the thread guide closest to the bobbin. Once the
thread is through the tension discs, pull on both sides to make sure the thread is seated between the
tension discs. Then, if your bobbin has slots in the center, run the thread through the slot towards the
center and out the top of the bobbin. If your bobbin does not have slots, leave the bobbin on the post and
wrap the thread around the bobbin counterclockwise 4
–
5 revolutions to get the winding process started.
10.
Adjusting sensor position to set
for bobbin size.
4.
Adjusting sensor
position to set for
bobbin size.
3.
Pull on thread to
seat between
tension discs.
2.
Place thread through the
first guide, around the
tension discs counter-
clockwise and through the
second guide.
1.
Pull thread up and
over the thread
stand from the right
to the left.