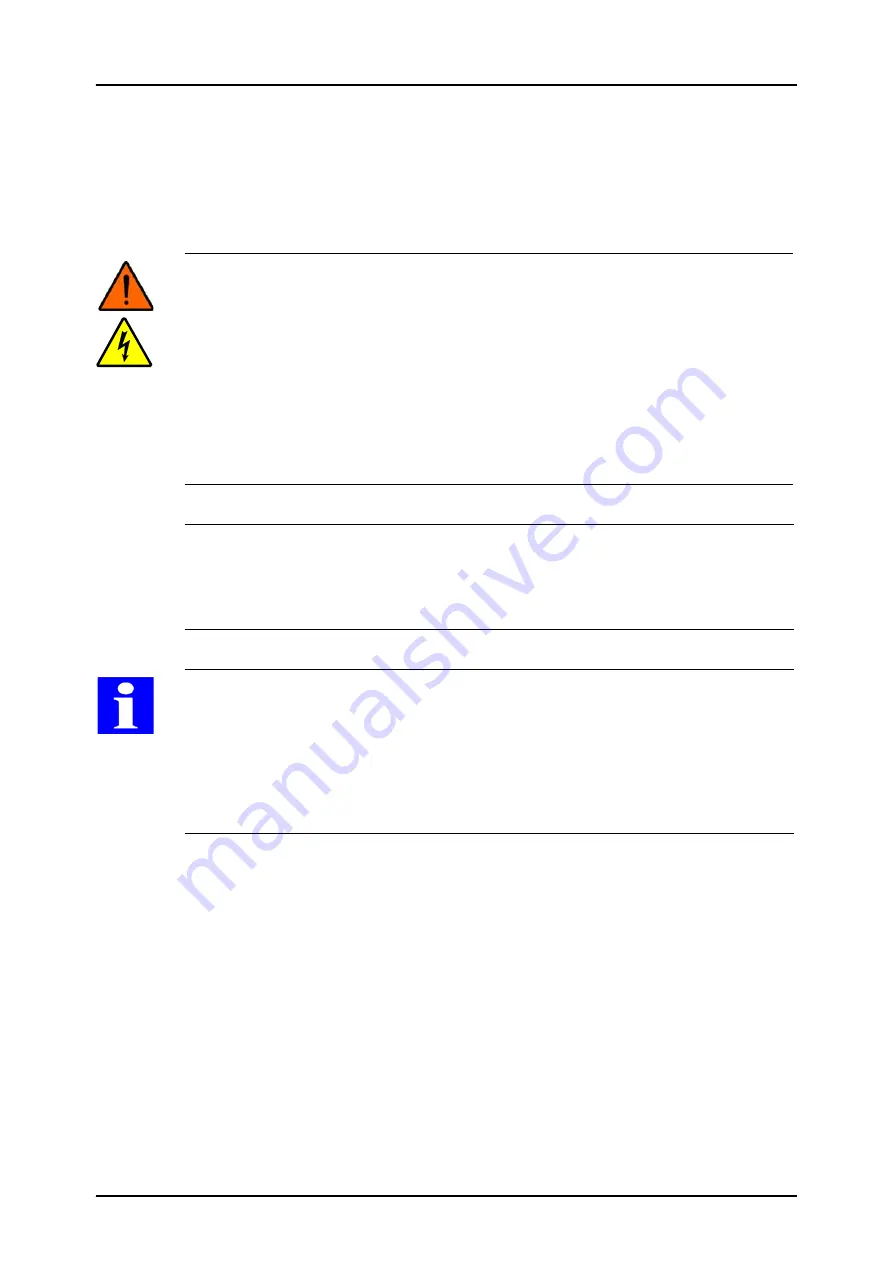
2015
53
Maintenance
&
Care
9
Maintenance & Care
9.1
Safety Notes
WARNING
Please
note
that
physical
contact
with
voltage-carrying
system
parts
may
lead
to
body
injury
or
even
death!
Turn
system
power
off
and
detach
power
cable
from
the
line
power
socket
before
you
proceed
to
any
kind
of
work
for
maintenance
or
care!
Take
adequate
precautions
to
protect
the
system
from
accidental
restoration
of
power!
Operating
personnel
are
prohibited
from
performing
work
for
maintenance,
repair
or
adjustment
of
voltage-carrying
system
parts!
Maintenance,
repair
or
adjustment
of
system
modules
under
electrical
voltage
may
only
be
carried
out
by
a
qualified
electrician!
CAUTION
Penetrating
liquid
may
cause
material
damage
to
electrical
and
electronic
components!
Make
sure
that
no
liquid
can
penetrate
into
the
inner
space
during
any
kind
of
maintenance
or
care.
NOTE
Intervention
to
mechanical
or
electronic
parts
in
the
inner
space
may
not
be
performed
by
anyone
other
than
customer
service
personnel
or
spe-
cially
authorized
expert
technicians.
To
ensure
that
your
system
is
kept
in
a
state
of
optimal
adjustment
and
faultless
function
over
a
longer
period
of
time,
we
recommend
the
conclusion
of
a
service/maintenance
contract
with
Analytik
Jena
AG
Jena.
Содержание 845-00003-03
Страница 1: ...InnuPure C96 User Manual ...
Страница 2: ......
Страница 4: ......
Страница 6: ......
Страница 7: ...2015 VII ...
Страница 8: ...VIII 2015 ...
Страница 12: ...XII 2015 ...
Страница 20: ...8 2015 General Information ...
Страница 44: ...32 2015 Technical Description ...
Страница 54: ...42 2015 Routine Start Up Procedure ...
Страница 60: ...48 2015 Operation ...
Страница 64: ...52 2015 What to do if ...
Страница 72: ...60 2015 Shutting Down ...
Страница 76: ...64 2015 Waste Disposal ...