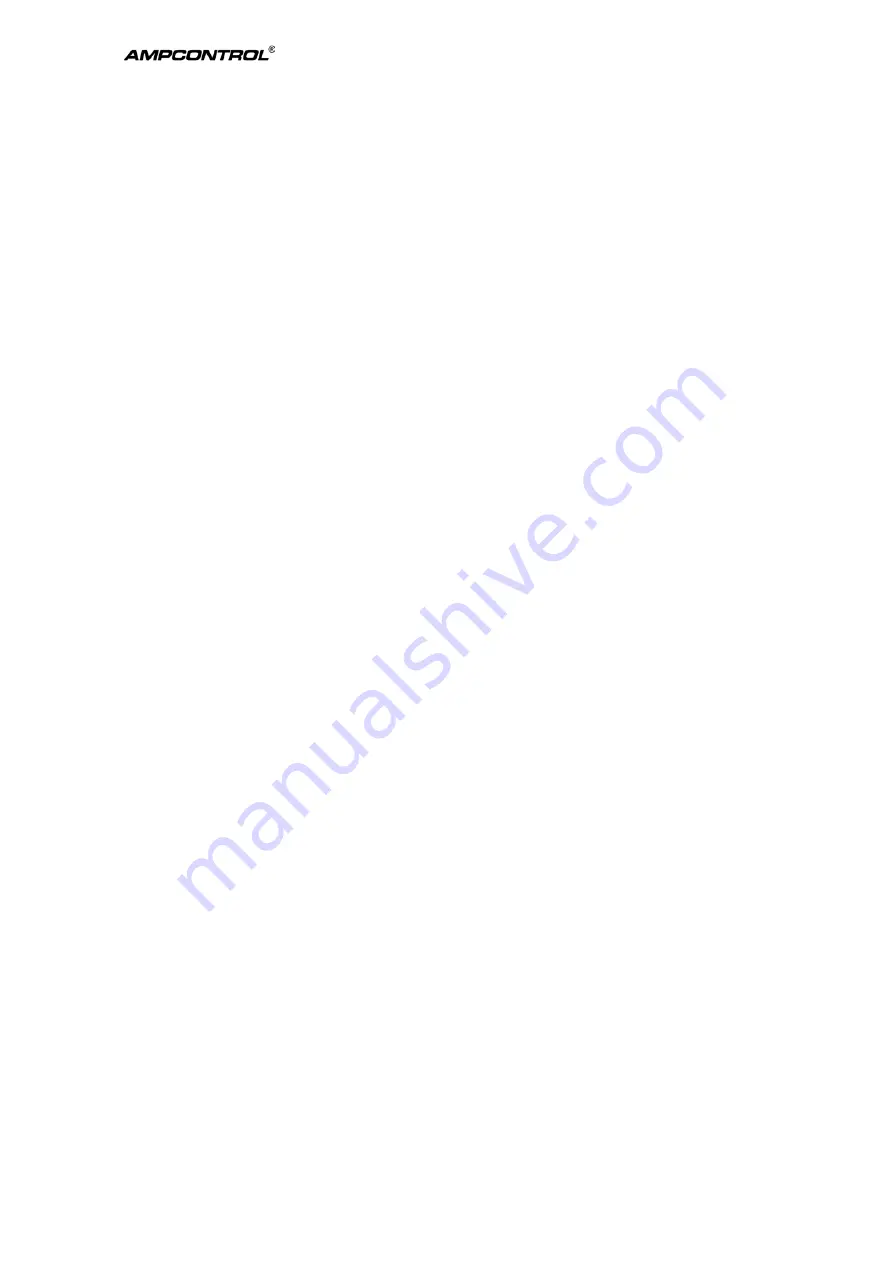
GASGUARD IS CONTROLLER Issue: R2, Date: 26/09/2011, CRN: 7502
Page 33
5.2
Mounting the Controller
5.2.1
IP rating and Physical Protection
The Controller enclosure is not rated to provide either dust or water ingress protection.
To ensure that the Controller is not subjected to conditions that could cause dust or moisture to enter the
enclosure, it must be mounted inside a suitable IP rated wall mounted enclosure.
Although the Controller housing is made from tough ABS, it will not provide protection against impact from heavy
objects. Damage to the enclosure and internal electronics could cause malfunction, rendering the controller
unsafe. Mounting the Controller in a robust, lockable enclosure will minimise the chance of physical damage.
5.2.2
Ease of Access
Mounting the Controller within an enclosure should be done in such a way as to allow full access to the
connection terminals, display and buttons. Positioning of the Controller should also be such to allow easy
removal of the unit for repair. The Controller should also be clearly visible to allow inspections to be carried out
without having to remove parts of the installation (visual inspections)
5.3
Connecting to the Controller
Wiring of the controller and systems must be carried out with reference to standards appropriate for the application,
industry and/or locale. Failure to comply with standards could lead to a dangerously installed system.
5.3.1
Entity Parameters
When connecting the Controller to other equipment, it is important that the specified parameters that apply to
each Controller terminal are known and understood. It is also important to know and understand these
parameters in relation to connected equipment and cables. These parameters are given on the equipment’s
certificate of compliance and set the maximum limits, beyond which the equipment is no longer safe to use within
its hazardous area certification. These specified limits, known as ‘entity parameters’ inform and restrict quantities
such as voltages, currents, capacitance and inductance in relation to the terminals that will be used to connect to
other equipment.
Inputs will have maximum allowable voltages and currents that may be applied to them along with maximum
values of capacitance and inductance that appear at these terminals resulting from internal circuitry.
Typical input parameters would be:-
Ui:
Maximum voltage that can be applied to an input terminal
Ii:
Maximum current that can be supplied to an input terminal
Ci / Li:
Maximum capacitance / inductance that ‘appears’ at an input terminal
Output terminals will have maximum values of voltages and currents available from them, specified under worst
case conditions. Outputs also carry limitations regarding the maximum capacitance and inductance that they can
connect to whilst maintaining safe operation. Output terminals may also specify the level of capacitance and
inductance that appears on them as a result of internal circuitry.
Typical output parameters would be:-
Uo:
Maximum voltage available from a terminal under worst case conditions
Io:
Maximum current available from a terminal under worst case conditions
Co / Lo:
Total capacitance / inductance that can be safely connected to a terminal
Capacitance is found in connecting cables and the inputs of other equipment. When connecting equipment
together, the total values of all capacitances and inductances must be taken into account and must not exceed
the values specified for that connection or system total. For example, if a gas detector’s output terminal has 1nF
of capacitance associated with it, and can connect safely to a maximum capacitance of 10nF, any equipment and
cable that is to be connected to the gas detector must have a total capacitance of no more than 9nF.
Содержание gasguard
Страница 46: ...GASGUARD IS CONTROLLER Issue R2 Date 26 09 2011 CRN 7502 Page 45 10 2 Modbus Memory Map Part 2 ...
Страница 47: ...GASGUARD IS CONTROLLER Issue R2 Date 26 09 2011 CRN 7502 Page 46 ...
Страница 49: ...GASGUARD IS CONTROLLER Issue R2 Date 26 09 2011 CRN 7502 Page 48 A2 Top Level Functional Block Diagram ...
Страница 50: ...GASGUARD IS CONTROLLER Issue R2 Date 26 09 2011 CRN 7502 Page 49 A3 Input Channel Functional Block Diagram ...
Страница 51: ...GASGUARD IS CONTROLLER Issue R2 Date 26 09 2011 CRN 7502 Page 50 A4 Zoning Functional Block Diagram ...
Страница 52: ...GASGUARD IS CONTROLLER Issue R2 Date 26 09 2011 CRN 7502 Page 51 A5 Relay Functional Block Diagram ...
Страница 53: ...GASGUARD IS CONTROLLER Issue R2 Date 26 09 2011 CRN 7502 Page 52 A6 Current Follower Outputs Performance Graph ...
Страница 62: ...GASGUARD IS CONTROLLER Issue R2 Date 26 09 2011 CRN 7502 Page 61 B2 Main Menu Flowchart ...
Страница 63: ...GASGUARD IS CONTROLLER Issue R2 Date 26 09 2011 CRN 7502 Page 62 B3 Calibration Flowchart ...
Страница 64: ...GASGUARD IS CONTROLLER Issue R2 Date 26 09 2011 CRN 7502 Page 63 B4 Configuration Flowchart ...
Страница 65: ...GASGUARD IS CONTROLLER Issue R2 Date 26 09 2011 CRN 7502 Page 64 Configuration Flowchart con t ...
Страница 66: ...GASGUARD IS CONTROLLER Issue R2 Date 26 09 2011 CRN 7502 Page 65 Configuration Flowchart con t ...
Страница 74: ...GASGUARD IS CONTROLLER Issue R2 Date 26 09 2011 CRN 7502 Page 73 Appendix C Approvals ...
Страница 75: ...GASGUARD IS CONTROLLER Issue R2 Date 26 09 2011 CRN 7502 Page 74 ...
Страница 76: ...GASGUARD IS CONTROLLER Issue R2 Date 26 09 2011 CRN 7502 Page 75 ...
Страница 77: ...GASGUARD IS CONTROLLER Issue R2 Date 26 09 2011 CRN 7502 Page 76 ...
Страница 78: ...GASGUARD IS CONTROLLER Issue R2 Date 26 09 2011 CRN 7502 Page 77 ...
Страница 79: ...GASGUARD IS CONTROLLER Issue R2 Date 26 09 2011 CRN 7502 Page 78 ...