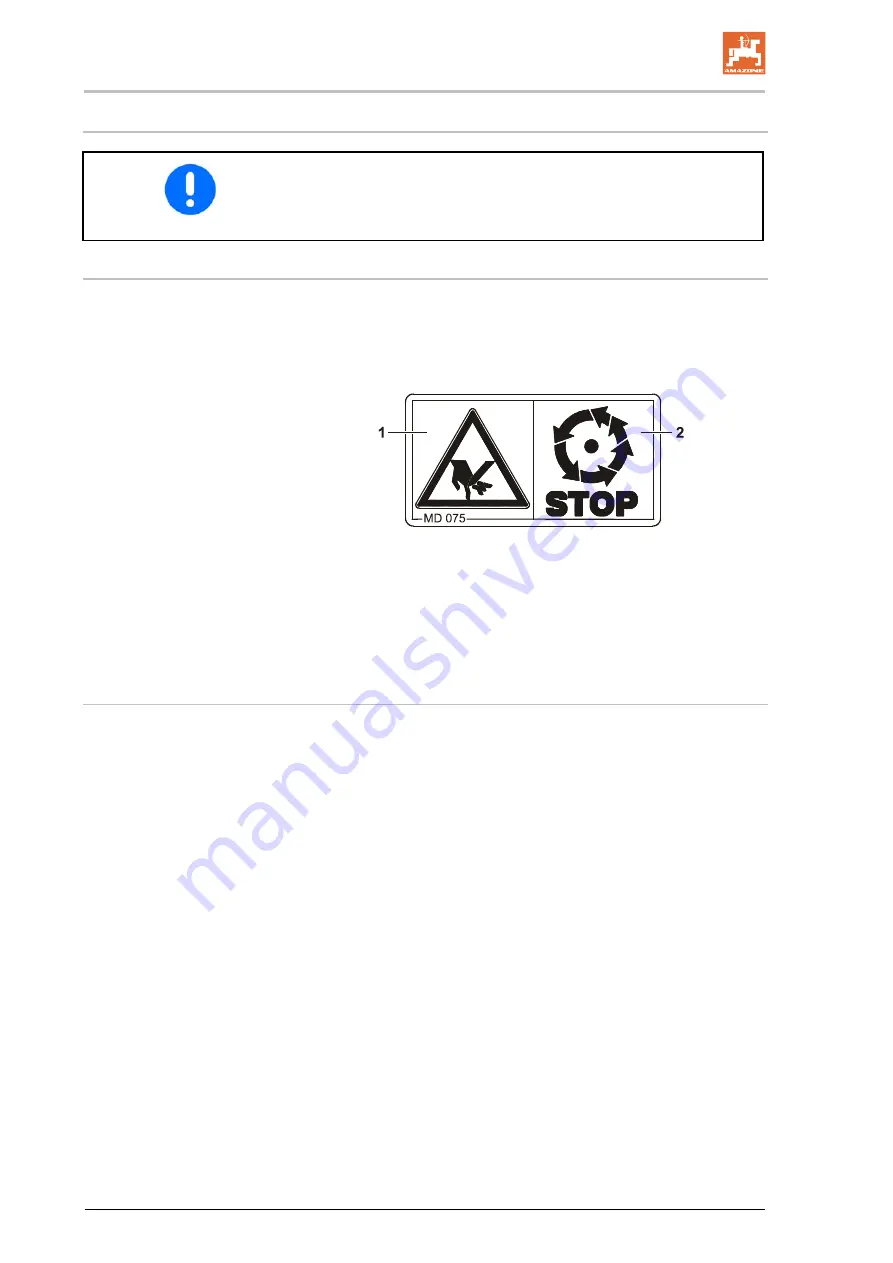
General safety instructions
2.13
Warning symbols and other signs on the machine
Always keep all the warning symbols on the machine clean and in a
legible state. Replace illegible warning symbols. You can obtain the
warning symbols from your dealer using the order number (e.g. MD
075).
Warning symbols - structure
Warning symbols indicate danger areas on the machine and warn
against residual dangers. At these points, there are permanent or
unexpected dangers.
A warning symbol consists of two fields:
Field 1
is a symbol describing the danger, surrounded by triangular safety
symbol.
Field 2
is a symbol showing how to avoid the danger.
Warning symbols - explanation
The column
Order number and explanation
provides an explanation
of the neighbouring warning symbol. The description of the warning
symbols is always the same and specifies, in the following order:
1. A description of the danger.
For example: risk of cutting
2. The consequence of non-compliance with the risk avoidance
instructions.
For example: causes serious injuries to fingers or hands.
3. Risk avoidance instructions.
For example: only touch machine parts when they have come to
a complete standstill.
18
UX Super
BAG0054.10 11.16