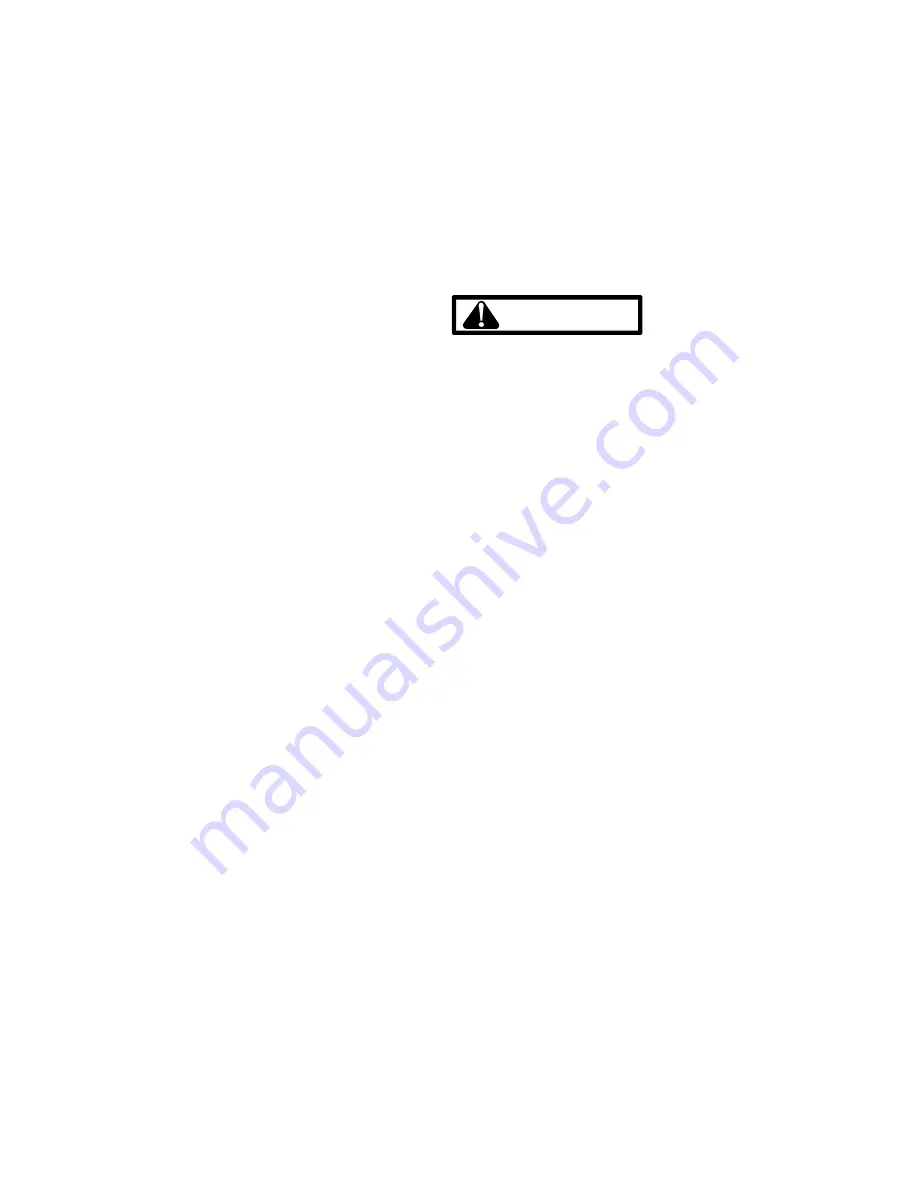
68
Rev. 2
SERVICING
TEST EQUIPMENT
Proper test equipment for accurate diagnosis is as essen-
tial as regulator hand tools.
The following is a must for every service technician and ser-
vice shop.
1. Dial type thermometers or thermocouple meter (optional)
- to measure dry bulb temperature.
2. Amprobe - to measure amperage and voltage.
3. Volt-Ohm Meter - testing continuity, capacitors, and
motor windings.
4. Micro-Amp meter for reading flame sense signal.
5. Inclined Manometer - to measure static pressure, pres-
sure drop across coils, filters, and draft.
6. "U" Tube Manometer (12") - to test gas inlet and mani-
fold pressure, Induced Draft negative pressure.
Other recording type instruments can be essential in solv-
ing abnormal problems, however, in many instances they
may be rented from local sources.
Proper equipment promotes faster, more efficient service and
accurate repairs resulting in fewer call backs.
HEATING PERFORMANCE TEST
Before attempting to diagnose an operating fault, run a heat-
ing performance test and apply the results to the Service
Problem Analysis Guide.
To conduct a heating performance test, the BTU input to the
furnace must be calculated.
After the heating cycle has been in operation for at least
fifteen minutes and with all other gas appliances turned off,
the gas meter should be clocked.
To find the BTU input, multiply the number of cubic feet of
gas consumed per hour by the heating value of the gas be-
ing used. (The calorific value of the gas being used is found
by contacting your local utility.)
Example:
It is found by the gas meter, that it takes forty (40) seconds
for the hand on the cubic foot dial to make one complete
revolution, with all appliances off, except the furnace. Take
this information and locate it on the gas rate chart. Observe
the forty (40) seconds, locate and read across to the one (1)
cubic foot dial column. There we find the number 90, which
shows that ninety (90) cubic feet of gas will be consumed in
one (1) hour.
Let's assume the local gas utility has stated that the calo-
rific value of the gas is 1025 BTU.
Multiplying the ninety (90) cubic feet by 1025 BTU gives us
an input of 92,250 BTUH.
Checking the BTU input on the rating plate of the furnace
being tested.
EXAMPLE:
GUIA090B30
INPUT: 92,000 BTU/HR
OUTPUT CAP: 74,000 BTU/HR
Should the figure you calculated not fall within five (5) per-
cent of the nameplate rating of the unit, adjust the gas valve
pressure regulator or resize orifices.
Note: For the GUIS,GCIS and GUIV Two-Stage Furnaces
the heating performance test will need to be conducted in
both the low stage (1st stage) operation, then repeated in
the high stage (2nd stage) operation.
CAUTION
Always connect a manometer to the 1/8" pipe tap at
the gas valve before adjusting the pressure regulator.
In no case should the final manifold pressure vary more
than plus or minus .3 inches water column from 3.5
inches water column for natural gas or 10 inches wa-
ter column for propane gas.
To adjust the pressure regulator on the gas valve, turn down
(clockwise) to increase pressure and input, and out (coun-
terclockwise) to decrease pressure and input.
Since normally propane gas is not installed with a gas meter,
clocking will be virtually impossible. The gas orifices used
with propane are calculated for 2500 BTU gas and with proper
inlet pressures and correct piping size, full capacity will be
obtained.
With propane gas, no unit gas valve regulator is used; how-
ever, the second stage supply line pressure regulator should
be adjusted to give 11" water column with all other gas con-
suming appliances running. Units installed on propane gas
are derated 10% by design when installed with the proper
propane conversion kit.
The dissipation of the heat transferred to the heat exchanger
is now controlled by the amount of air circulated over its
surface.
The amount (CFM) of air circulated is governed by the exter-
nal static pressure in inches of water column of duct work,
cooling coil, registers and etc., applied externally to the unit
versus the motor speed tap (direct drive).
A properly operating unit must have the BTU input and CFM
of air, within the limits shown to prevent short cycling of the
equipment. As the external static pressure goes up, the
temperature rise will also increase. Consult the proper tables
for temperature rise limitation.
Содержание GCIA045A30
Страница 34: ...BLOWER PERFORMANCE SPECIFICATIONS 34 Rev 2...