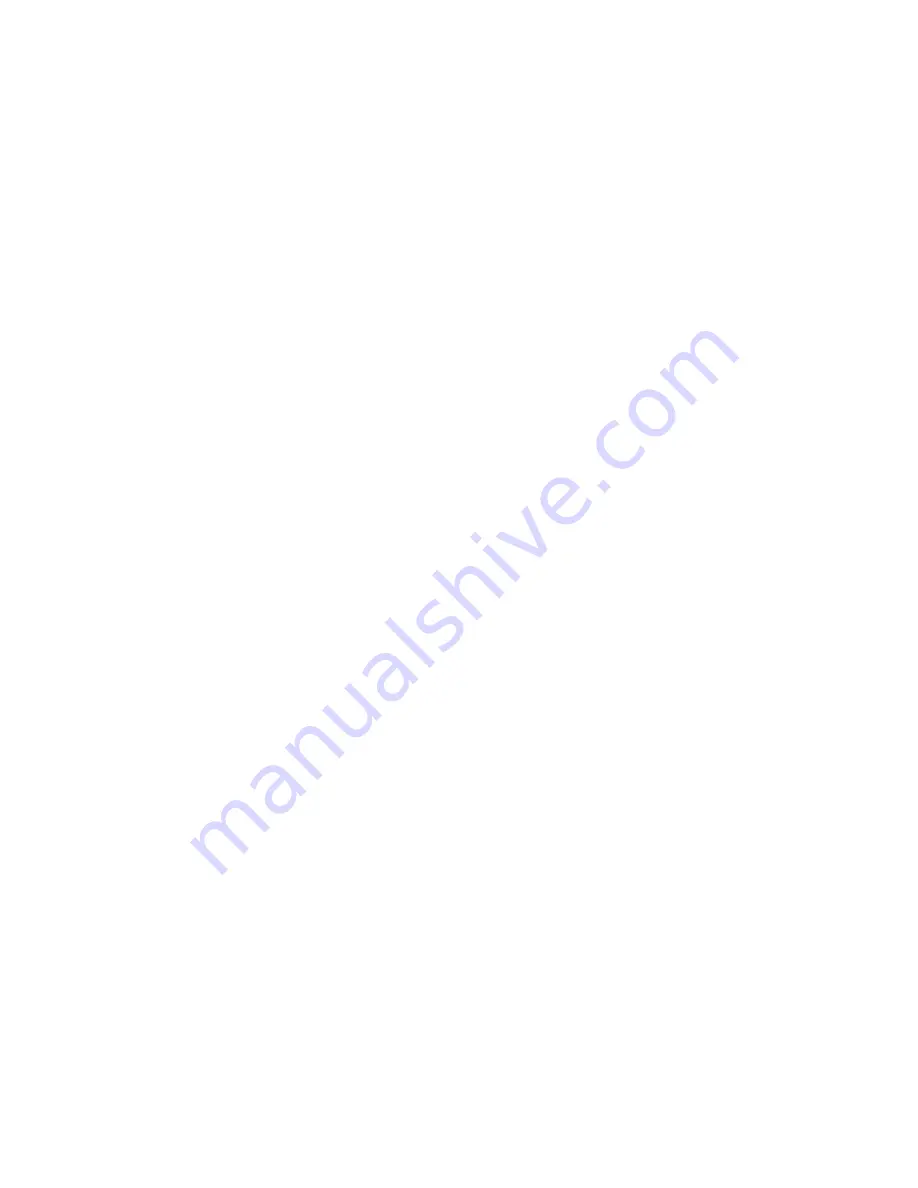
Lid Switch Test
This step verifies that the Lid Switch is correctly wired and work-
ing. Close the lid. When the lid switch is closed, the SPIN and
LID LOCK LEDs will be lit.
Close the lid and press Start/Pause button to exit the step.
Hot Fill Test
This step checks the hot water valve. The WASH LED is on dur-
ing this test. The valves will shut off once two inches of water
has been reached.
Press Start/Pause button to advance to the next step.
Cold Fill Test
This step checks the cold water valve. The RINSE LED is on dur-
ing this test. The valves will shut off once three inches of water
has been reached.
Press Start/Pause button to advance to the next step.
Pressure Sensor Fill Test
This step checks the water level input. All water valves will be on
until the low water fill level is satisfied (four inches). The WASH
and RINSE LEDs will be lit in this step.
Press Start/Pause button once the water level is satisfied to exit
the step.
Lid Lock Test
This step checks the Lid Lock input. When the step is entered, the
control will lock the lid. It will check to make sure the lid is
locked and if it is, the LID LOCK LED will be on, otherwise the
LID LOCK LED will flash.
Once locked, press Start/Pause button to exit the step.
Long Stroke Agitate Test
In Software Version 3 and higher this is skipped.
Not available on models through Serial Nos. beginning 1810.
This step checks the Low Agitate speed. The WASH and SPIN
LEDs are On, the Cycle Run Output is on, and the machine enters
a Delicate Cycle Long agitate.
The control will remain in this step until the Start/Pause button is
pressed.
Short Stroke Agitate Test
In Software Version 3 and higher this is skipped.
Not available on models through Serial Nos. beginning 1810.
This step checks the Regular Agitate speed. The RINSE and
SPIN LEDs are on and the machine enters a Delicate Cycle Short
agitate.
The control will remain in this step until the Start/Pause button is
pressed.
Factory Spin Test
This step checks the spin speeds. The machine steps through spin
speeds and maintains each speed for a few seconds. After 820
RPM, the motor will stop. All OBL checking is done and if either
the out of balance switch is hit or the OBL check fails at 300
RPM, the time will be reset indefinitely to allow the load to be
rebalanced so that it can spin up and reach full speed.
The control will advance to the next step if the Start/Pause button
is pressed at any time during this step.
During this step, if 300 RPM is reached, the WASH LED will be
lit. If 500 RPM is reached, the RINSE LED will be lit. If 820
RPM is reached, the SPIN LED will be lit and if 800 RPM is
reached, the LID LOCK LED will be lit to indicate that a passing
speed has been reached.
All water valves will be on during this entire test to blow them
out.
Unbalance Switch Test
This step checks that the unbalance switch is working. The
WASH and RINSE LEDs will be on during the entire test. When
the switch is pressed, the SPIN and LID LOCK LEDs will be on.
The switch must be pressed and then Start/Pause button can be
pressed to advance to the next step.
Breakaway Test
This step checks the lid unlock function. All valves will be open
at the beginning of this step to allow the blowing out of the
valves, if needed. The Start/Pause button must be pressed to start
exiting the test. The first Start/Pause press will turn off the water
valves and start the unlock process. Once the lid unlocks, the ma-
chine will exit the test.
The RINSE and SPIN LEDs will be lit during this test. The LID
LOCK LED will be lit when the lid is locked in this test.
Power Down Test
This is the final step of the factory test procedure. All LEDs will
be off to signify that the factory test procedure has been complet-
ed and that the user can safely unplug the machine. Cycling pow-
er to the machine is the only way to resume normal operation.
Advance to Drain and Spin
Models starting Serial Nos. beginning 1804 can be rapid ad-
vanced to the final spin/drain step. For example, when testing a
washer you could enter this mode after the machine fills to ad-
vance to the final spin to drain out the water.
How to Advance:
1. Make sure EXTRA RINSE is in the OFF position.
Troubleshooting Diagnostics
©
Copyright, Alliance Laundry Systems LLC -
DO NOT COPY or TRANSMIT
13
Part No. 204666ENR1
Содержание ZWN43RSN115CW01
Страница 2: ......