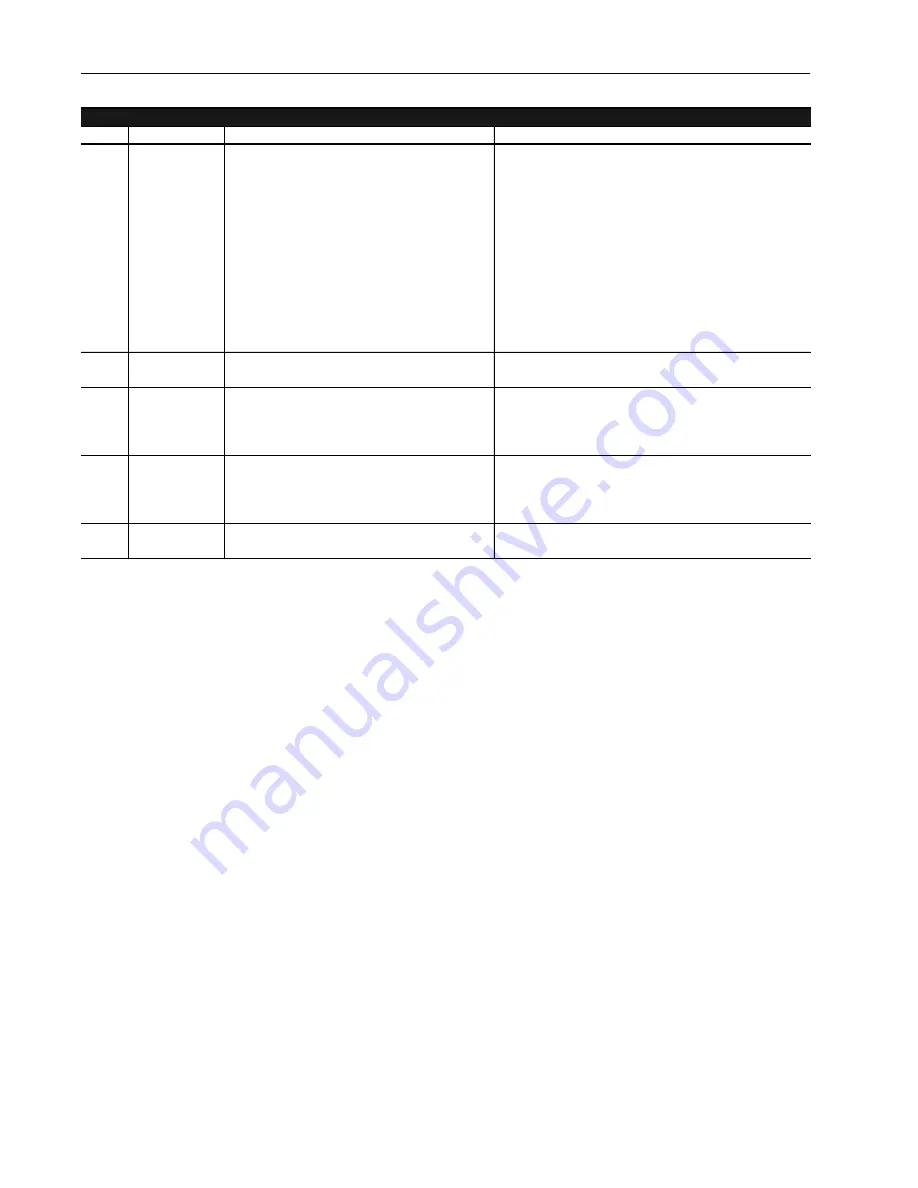
2-22
Malfunctions with Indications
Current Processor Faults
(CP–XX)
The Current Processor is responsible for fault monitoring of the armature
and field bridges in the drive. This includes monitoring the armature and
field currents to the motor, power components, incoming line
synchronization, and communications to the Velocity Processor. These
faults can be induced by problems external to the immediate drive such as
incoming AC line variations, motor malfunction, etc. An attempt to identify
and correct these conditions, if applicable, must be done prior to replacing
components in the drive. Internal drive malfunctions are also monitored
such as bridge component malfunctions, excessive currents, loss of power
supplies, etc. These faults will try to indicate the cause of the problem so
that it can corrected.
A test of the armature bridge components is made every time the power is
cycled or the drive is RESET. This testing will alert the user to a shorted
bridge component prior the start of normal operation, minimizing the
possibility of further damage. A more comprehensive armature bridge test
is performed during Autotune. This test verifies conduction capability as
well as shorted or open power devices.
Internal processor faults that occur can be induced by Electrostatic
Discharge (ESD), Electromagnetic Interference (EMI), excessive heat,
contamination of printed circuit boards (PCB), improper connector
connections, etc. An attempt should be made to correct any of these
environmental conditions prior to replacing components in the drive. This
can help reduce the possibility of reoccurrence. If board replacement is
necessary, replace the board and any EPROMS that may reside on the
board.
VP-49
CEMF Unstable
(Soft)
The measured CEMF did not stabilize during a
Field Flux measurement. The CEMF must be
stable in 2 seconds after an adjustment of the field
current.
Execute a Clear Fault and attempt normal operation. If the
fault reoccurs, verify that the actual velocity is remaining
relatively constant. This fault can be caused by varying
speed, varying loads which results in armature reaction, or
incorrect CEMF regulator gains (parameters 672,673), all
which can cause the CEMF to vary. It can also be caused by
having parameter 610 “Rated Motor Volt” incorrectly set-up.
Programmed Rated Motor voltage must be achieved for
proper operation.
Check Parameters 612 & 616. Parameter 612 must equal
rated field from motor nameplate, and Param 616 value
should be taken from Table 8-J of the Installation Manual.
VP-50
Profile Timeout
Velocity loop Autotune profile did not complete
within 5 minutes.
Motor or system inertia too great, parameter 698 too low.
Execute a Clear Fault and reattempt Autotune.
VP-51
No Current Limit
on Accel
Autotune velocity test failed on the accel portion of
the profile.
Autotune current limit (parameter 698) was not reached.
Verify Current Loop Tune was done prior to velocity loop.
Parameter 698 may have too high a value or parameter 699
may be too low. Clear faults and reattempt Autotune.
VP-52
No Current Limit
on Decel
Autotune velocity test failed on the decel portion of
the profile.
Current limit (parameter 698) was not reached. Verify
Current Loop Tune was done prior to velocity loop.
Parameter 698 may have too high a value or parameter 699
may be too low. Clear faults and reattempt Autotune.
VP-53
Contactor
Control
Autotune for current loop was aborted due to
contactor closed or contactor forced open.
Assure that ECOAST is NOT open and contactor is not
closed. Reset faults and try again.
Velocity Processor Faults
No.
Name
Description
Recovery
Aotewell Ltd industry-mall.net
www.aotewell.com
www.aotewell.com
Содержание 1395
Страница 104: ...A 14 Parameter List Record Notes Aotewell Ltd industry mall net www aotewell com sales aotewell com www aotewell com ...
Страница 106: ...Index 2 Notes Aotewell Ltd industry mall net www aotewell com sales aotewell com www aotewell com ...
Страница 107: ...Aotewell Ltd industry mall net www aotewell com sales aotewell com www aotewell com ...