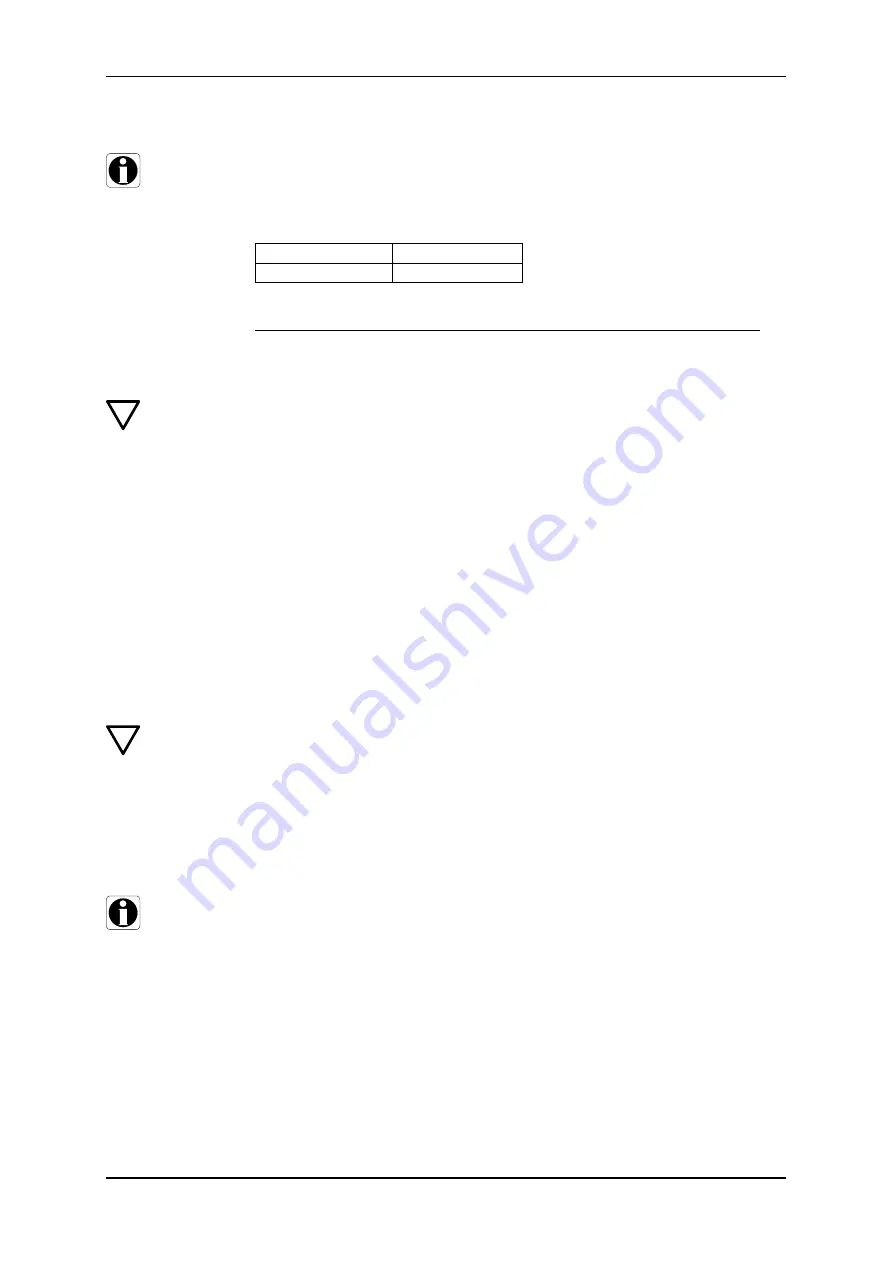
KM 255 en
42
15.720045-V1.0
6. Only close the deaeration screw (2u) when the separating agent stops flowing. (after
approx. 5 - 10 min)
Note
Once filled with separating agent and after a few operating hours, especially if the
pressure of the manometer is increasing, deaerate again.
Filling quantity of paraffin oil for dosing pumps with a double diaphragm (per dosing head)
Ordering data for double diaphragm filling components
9.7.5
Filling gear oil
Caution
Risk of leaking and damage caused by oil loss! For each oil change, a new flat gas-
ket (1b) must be used!
Check that the lock screw (B) is tightened.
1. Unscrew and remove the aeration screw and oil-level gauge (F).
2. Set the stroke adjustment button (L) to “0”.
3. Slowly add the hydraulic oil through the aeration screw opening (F), until the oil rea-
ches the mark on the oil-level gauge.
4. Wait 30 minutes.
5. Run the pump for approx. 5 minutes with a stroke adjustment of 0%.
6. Run the pump for approx. 10 minutes with a stroke adjustment of 40%.
9.7.6
Checking the oil level.
7. Switch off pump, check the oil level and add oil if necessary.
8. Fit the aeration screw and oil-level gauge (F) back on.
Caution
Following initial start-up and after each time the diaphragm is changed, tighten the
fixing screws on the dosing head:
After approximately 6 - 10 working hours or two days, tighten the dosing head
screws crosswise using a torque wrench.
Torque:
9.7.7
Cleaning the ball check valve
Note
Only clean the ball check after a diaphragm breakage!
Pump Type
Filling quantity in ml
KM 255
8
Order No.
Description
555-410
Filling components, set with paraffin oil, throw-away syringe and hose parts
50 - 54 Nm for KM 255
Содержание KM 255
Страница 34: ...KM 255 en 34 15 720045 V1 0 controller...
Страница 51: ...KM 255 en V1 0 51...
Страница 52: ...KM 255 en 52 15 720045 V1 0...