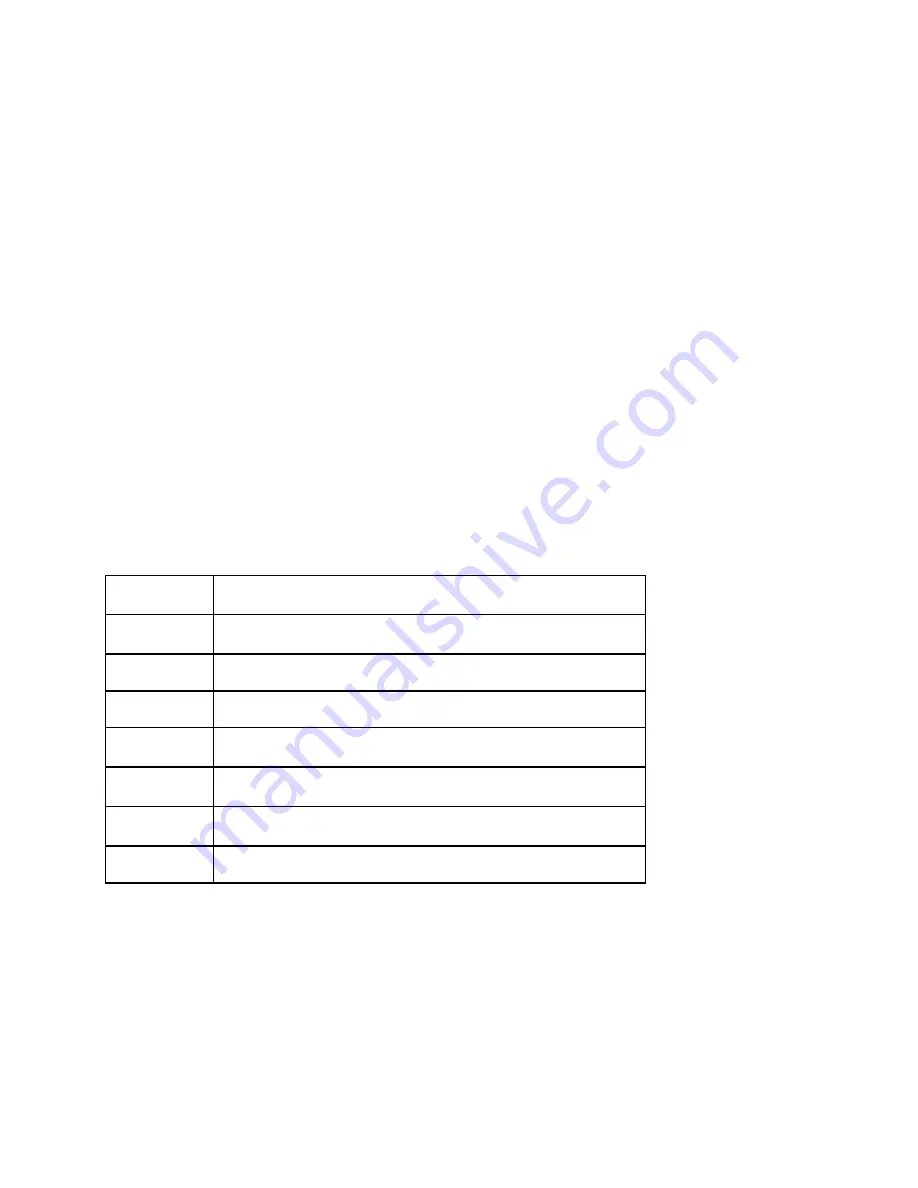
64
8210–00011 R1
3. Loosen cable clamps on cable truss where the cable requires adjustment.
4. Locate the eyebolt anchors for the cable. Refer to
5. Tighten cable eyebolts evenly on both sides (use eyebolt nuts to tighten eyebolts) until the discharge end
just starts to angle upward.
•
The tube should not deflect to the left or right if tightened evenly.
•
Tension should be greater on shorter cables than on longer cables. If the conveyor tubes remain straight
then the cables are tensioned properly.
6. If the proper cable tension can’t be obtained before the eyebolts run out of adjustment, then do the
following:
a. Loosen the eyebolts.
b. At the eyebolts, loosen the cable clamps, shorten the cables until there is tension on the cable, then
tighten the cable clamps fully.
c. Return to step 5.
7. Secure jam nut on cable eyebolt and re-tighten any cable clamps that were loosened.
8. The cables are properly tightened when:
•
There is no slack in the cables.
•
The discharge end is deflected sightly upwards.
•
The tube is straight side-to-side.
Table 7.
Truss Cable Adjustment
Item
Description
1
Cable Clamp
2
Truss Cable
3
Cable Return Bracket
4
Cable Eyebolt
5
Eyebolt Nuts
6
Eyebolt Anchor
7
Cable Truss
SWING-AWAY CONVEYOR – PORTABLE GRAIN BELT CONVEYOR