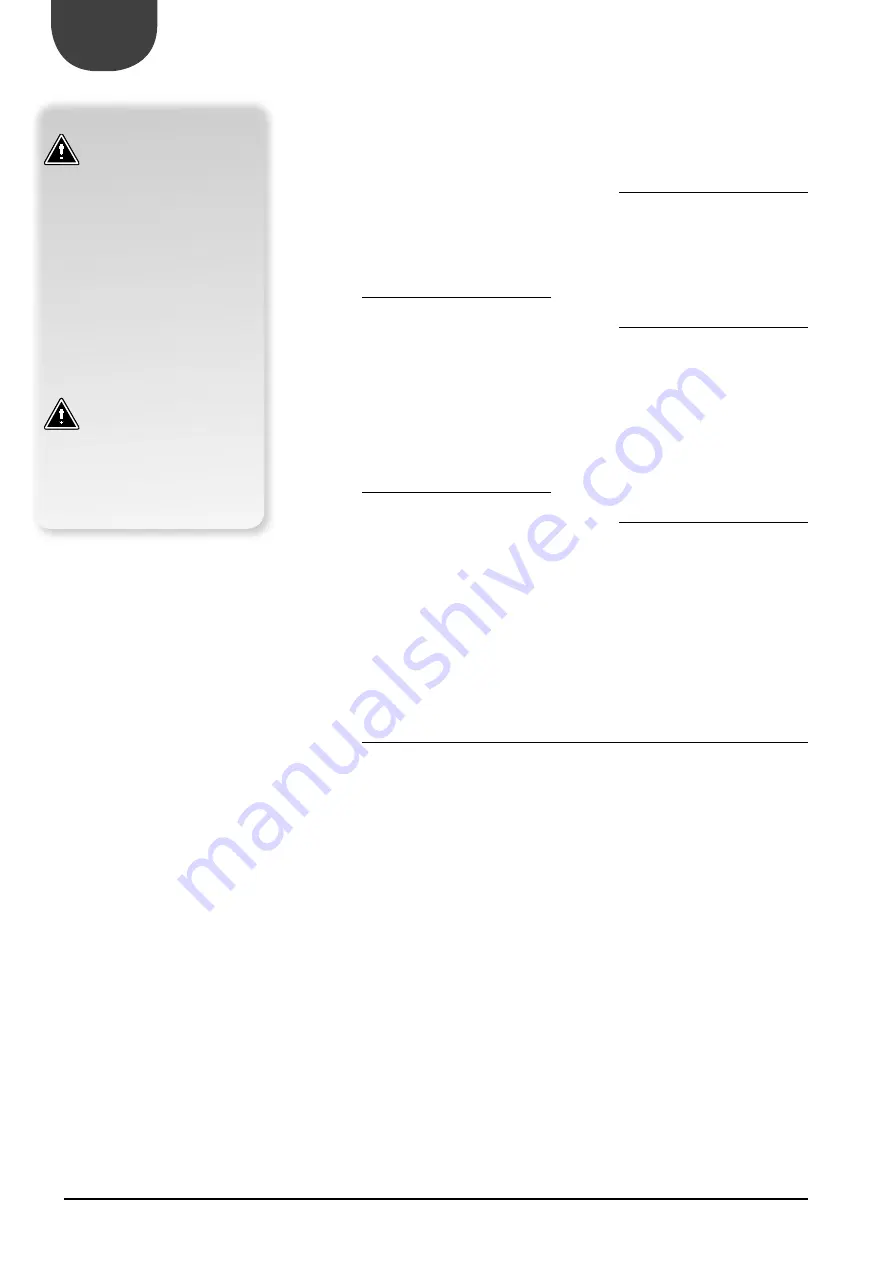
eN
1205. 6755517_02
34
27.
MAINteNANCe
27.1. eXtrAorDINArY MAINteNANCe
all cleaning is prohibited until the unit has been
disconnected from the electric power supply mains.
Make sure there is no voltage present before operat-
ing. Periodic maintenance is fundamental to keep
the unit perfectly efficient under a functional and
energetic point of view.
It is therefore essential to carry out periodic yearly
controls for the:
27.2. HYDrAULIC CIrCUIt
CHECK:
1.
Refilling of water circuit
2.
Cleaning the water filter
3.
Control of pressure/flow switch
4.
no air in the circuit (bleed) that the water flow
rate to the
5.
Evaporator is constant
6.
The thermal insulation state of the hydraulic
piping
7.
The percentage of glycol where necessary
27.3. eMPtYINg tHe SYSteM
Before starting to drain the system, turn "off" the
unit
− Check that the water system load/restore tap is
closed
− open the drain tap outside the machine and all
the vent valves of the system and the correspon-
ding terminals.
− in case of prolonged shut-down of the unit
during winter (if not added with glycol) or for other
inconveniences, drain the chiller hydraulic circuit by
the corresponding knobs. If the system uses glycol,
this liquid should not be drained to the environment
because it is a pollutant. It must be collected and, if
possible, reused.
27.4. eLeCtrICAL CIrCUIt
CHECK:
8.
Safety efficiency
9.
Electric supply pressure
10. Electrical Input
11. Connection tightness
12.
Verify the operation of the carter compressor
resistance
27.5. CooLINg CIrCUIt
CHECK:
13. State of compressor
14. Efficiency of the plate heat exchanger resistan-
ce if envisioned
15. Work pressure
16. Leak test for watertightness control of the
cooling circuit
17. Functioning of high and low pressure switches
18. Carry out the appropriate checks on the filter
dryer to check efficiency
27.6. MeCHANICAL
CHECK:
1.
Check the tightening of the screws the
compressors and the electrical box, as well as
the exterior panelling of the unit. Insufficient
fastening can lead to undesired noise and
vibrations
2.
State of the structure.
Treat any shares if you encounter any oxidized
paint suitable to iminate or reduce the pheno-
menon of oxidation.
The anl | anlH are filled with r410a gas and are
inspected at the factory. Under normal conditions
they do not require Technical Assistance related to
control of refrigerant gas. Through time gas leakage
may be generated from the from the joints, causing
refrigerant to escape and discharge the circuit,
causing appliance malfunctioning. In these cases the
leakage points are to be discovered, repaired and
the Gas circuit is to be replenished, respecting the
December 28 1993 n°549 law.
Load procedure
13
1.
Empty and dry the entire cooling circuit using
a vacuum pump connected to the low and
high pressure socket until 10 Pa is read on the
vacuum meter. Wait a few minutes and check
that this value does not rise above 50 Pa.
2.
Connect the refrigerant gas cylinder or a load
cylinder to the socket on the low pressure
line.
3.
Load the amount of refrigerant gas indicated
on the appliance features plate.
4.
After a few hours of functioning, check that
the liquid indicator indicates the dry circuit
(dry-green). in the case of partial loss, the
circuit must be emptied completely before
being re-loaded.
5.
The R410A refrigerant must only be loaded in
the liquid state.
6.
Functioning conditions that are different to
the nominal conditions can give rise to values
that are greatly different.
7.
The sealing test or the search for leaks must
only be performed using R410A refrigerant
gas, checking using a suitable leak detector.
8.
In the cooling circuit it is prohibited to use
oxygen or acetylene or other inflammable or
poisonous gases because they are a cause of
explosions or intoxication.
Provide that the disposal unit is implemented in
accordance with the rules in force in different
countries.
AtteNtIoN
We recommend that you include a
booklet machine (not supplied, but
at the expense user), which allows to
keep track of operations performed
unit, in this way will be more
easy to organize adequately
facilitating research and interven-
tions prevention of potential failures
the machine.
Return the booklet date, type of
surgery performed (maintenance
ordinary inspection or repair),
description of the measures imple-
mented.
AtteNtIoN
13
cooling circuits must not be
filled with a refrigerant other
than that indicated. Use a
different refrigerant gases can
cause serious damage to the
compressor.
28.
DISPoSAL
Содержание ANL 100HA
Страница 2: ......
Страница 5: ......
Страница 30: ...eN 1205 6755517_02 30 23 HYDrAULIC CoNNeCtIoNS 102 mm 4 0 in 413 mm 16 3 in IN 1 OUT 1 ...