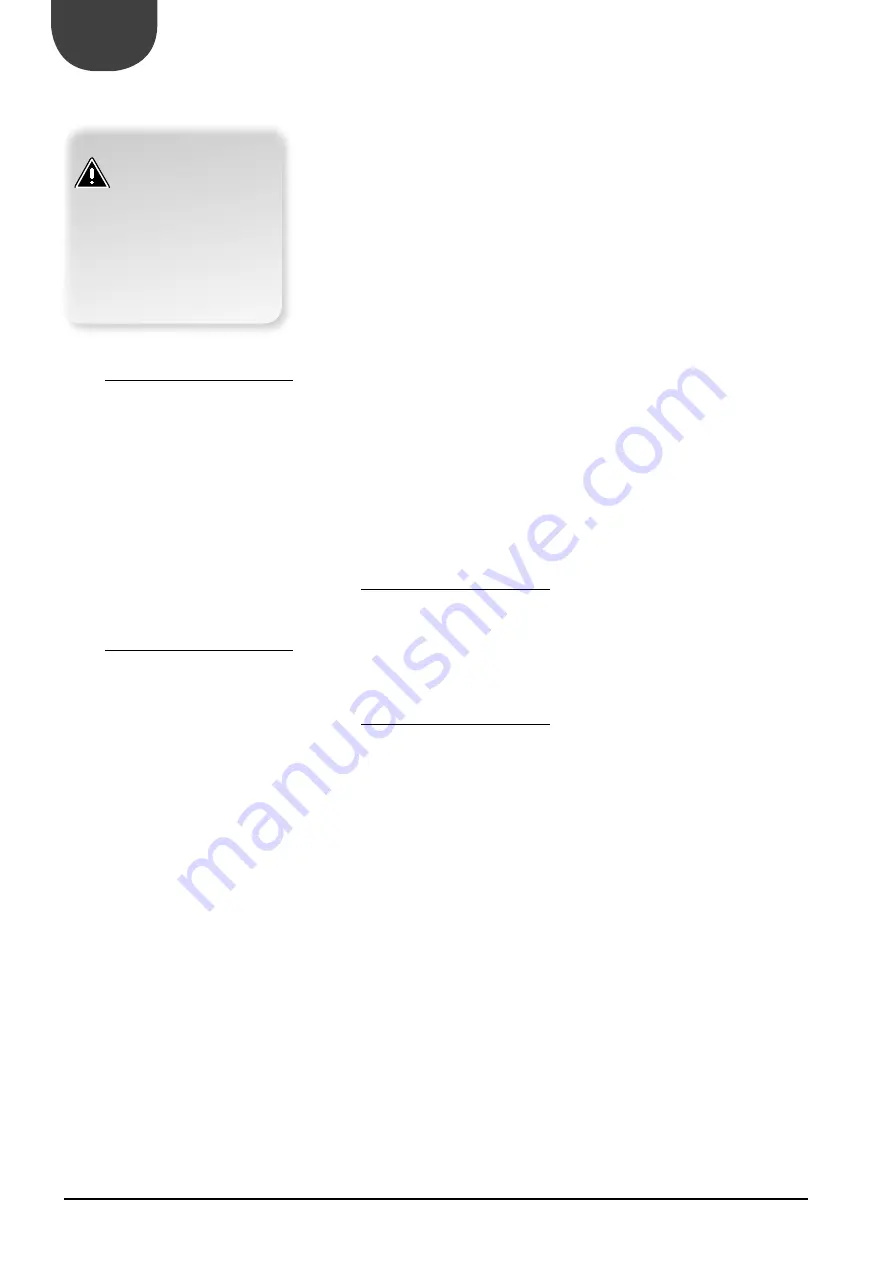
eN
1205. 6755517_02
32
25.
STrAT-UP
25.1. PreLIMINArY oPerAtIoNS to Be
MADe wItHoUt teNSIoN
check:
1.
All safety conditions have been respected
2.
The unit is correctly fixed to the support
surface
3.
The minimum technical spaces have been
respected
4.
That the power cables are generally of appro-
priate section, to withstand the overall drive
power consumption. (see section Electrical
data), and that the unit is properly connected
to earth.
5.
All electric and hydraulic connections have
been tightened well.
25.2. tHe FoLLowINg oPerAtIoNS Are
PerForMeD wHeN tHe UNIt IS
PowereD.
1.
Supply power to the unit by turning the
master switch to the ON position. The display
will come on a few seconds after voltage has
been supplied.
2.
Use a tester to check that the value of the po-
wer supply voltage to the RST phases is equal
to 400V ±10%; also verify that the unbalance
between phases is no greater than 3%.
3.
Check that the connections made by the
installer are in compliance with the documen-
tation.
4.
Verify that the resistor of the compressor
sump is working by measuring the increase in
temperature of the oil pan. The resistance/s
must function for at least 12 hours before
start-up of the compressor and in all cases the
temperature of the oil pan must be 10 -15°C
higher than the room temperature.
HYDrAULIC CIrCUIt
1.
Check that all hydraulic connections are
made correctly, that the plate indications are
complied
2.
Check that the hydraulic system is filled and
under pressure and also make sure that no air
is present; if so, bleed it.
SYSteM LoAD
:
Before starting the load,
CHECK
:
− that the system drain tap is closed.
− open all the drain valves of the system and of the
related terminals.
− open the shut-off devices of the system.
− start the filling by slowly opening the water
system load cock placed outside the machine.
− When water begins to flow from the terminal
vent valves,
close them and continue loading up
to read on the gauge the value of 1.5 bar. The
system is loaded at a pressure between 1 and 2
bar.
It is advisable to repeat this operation once
the machine has worked for some hours and to
periodically check the system pressure, restoring
if it drops below 1 bar. Check the hydraulic seal of
the joints.
3.
Verify that any on-off valves present in the
system are correctly opened.
4.
Make sure that the circulation pump is
operating and that the flow rate of the water
is sufficient to close the contact of the flow/
pressure switch.
5.
Check lthe water flow rate, measuring the
pressure difference between input and output
of the evaporator and calculate the flow rate
using theevaporator pressure drop diagram
present in technical documentation. (www
.
aermec.com)
6.
Check the correct functioning of the flow/
pressure switch if installed. Closing the cut-off
valve at the output of the heat exchanger; the
unit control panel must show the block. Finally
re-open thevalve and rearm the block.
25.3. MACHINe CoMMISSIoNINg
After having performed all controls stated above, it
is possible to start the unit by pressing the ON key.
The display shows the temperature of the water and
machine functioning mode. Check the operating
parameters (set-point) and reset any alarms present.
After a few minutes, the unit will begin operating.
25.3.1.
CHECKS THE MACHInE IS On
CooLINg CIrCUIt
CHECK:
-
That the compressor input current
is lower than
the maximum indicated in the technical data
table.
-
That in models with three-phase
power supply,
the compressor noise level is not abnormal. If this
is the case, invert a phase.
-
That the voltage value lies within the prefixed
limits
and that unbalance between the three
phases (three-phase power supply) is not above
3%.
-
The presence of any refrigerant GAS leaks
particularly with reference to pressure plugs,
pressure transducers and pressure switches.
(ViBraTions dUrinG TransporTaTion may
loosEn ConnECTions).
-
Overheating
Comparing the temperature read using a contact
thermostat positioned on the compressor intake
with the temperature shown on the low pressure
manometer (saturation temperature correspon
-
ding to the evaporation pressure). The difference
between these two temperatures gives the
overheating value. Optimal values are between 4
and 8°C
-
The Pressing line temperature
If the subcooling and overheating values are re-
gular the temperature measured in the pressing
line pipe at the outlet of the compressor must be
30/40°C above the condensation temperature.
CoNtroL AND SAFetY DeVICeS
CHECK:
- High pressure switch
That stops the compressor, generating the
respective alarm, when the delivery pressure
exceeds the setpoint value. The control of its
correct functioning can be performed by closing
the air intake to the exchanger (in cooling mode)
and keeping the high pressure manometer under
control, check the intervention in corresponden-
ce of the calibration value. Caution: In the event
of failure to intervene at the calibration value,
stop the compressor immediately and check
the cause. The reset is manual and can only be
performed when the pressure falls below the
differential value. (For the set and differential
values, consult the technical manual).
- The anti-freeze control
The anti-freeze control managed by the electronic
regulation and by the temperature probe located
at the outlet of the evaporator is to prevent the
formation of ice when the water flow rate is
too low. Correct operation can be checked by pro-
gressively increasingly the anti-freeze set-point
until it passes the outlet water temperature and
keeping the water temperature controlled with a
high precision thermometer, verify that the unit is
off and generates the respective alarm. After this
operation, take the anti-freeze set-point back to
its original value.
AtteNtIoN
Before carrying out the controls
indicated below, make sure that
the unit is disconnected from the
power mains. Make sure that the
master switch is locked in the
OFF position and an appropriate
sign is affixed. Before starting the
operations, check that there is no
voltage present using a voltmeter
or a phase indicator.
Содержание ANL 100HA
Страница 2: ......
Страница 5: ......
Страница 30: ...eN 1205 6755517_02 30 23 HYDrAULIC CoNNeCtIoNS 102 mm 4 0 in 413 mm 16 3 in IN 1 OUT 1 ...