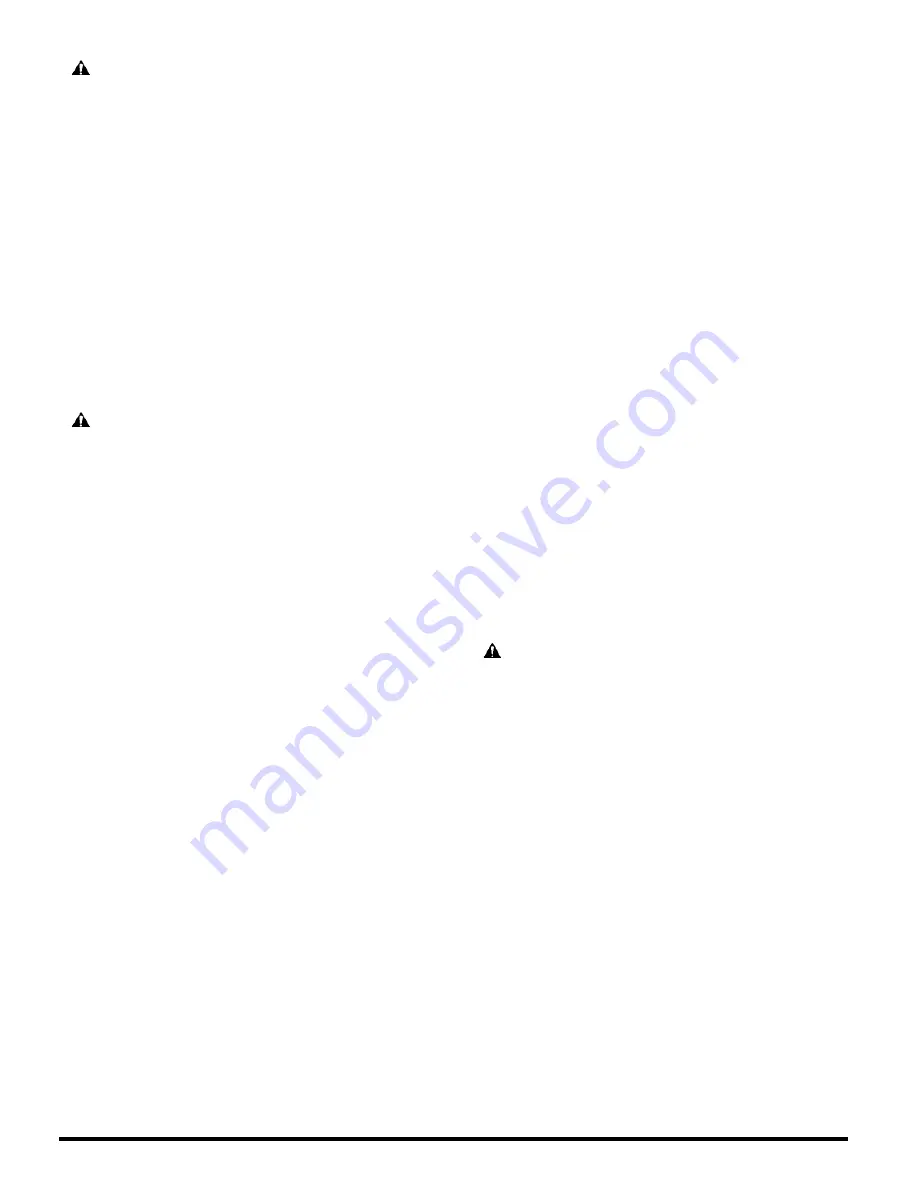
I&M No. V 5538 R8
©ASCO Valve, Inc.®
50 Hanover Road, Florham Park, New Jersey 07932 www.ascovalve.com
Testing for External Leakage
WARNING: To prevent the possibility of
severe personal injury or property damage,
extinguish all open
fl ames and avoid any type
of sparking or ignition.
1.
Block gas fl ow on downstream side of valve.
2.
Apply pressure to valve within nameplate rating and
energize solenoid.
3.
Apply a soapy solution or a commercially available leak
detecting solution to the pipe connections and check for
bubbles. If the valve has been tested for seat leakage or
disassembled and reassembled for inspecting, cleaning, or
rebuilding apply the solution around solenoid base sub
-
assembly, bonnet/body joint and pipe plugs.
4.
If leakage exists, depressurize valve and turn off electrical
power supply. Tighten connections as required and retest
following the above steps.
MAINTENANCE
WARNING: To prevent the possibility of
severe personal injury or property damage,
turn off electrical power, depressurize valve,
extinguish all open fl ames, and avoid any
type of sparking or ignition. Vent hazardous
or combustible fl uid to a safe area before
servicing the valve.
NOTE: It is not necessary to remove the valve from the pipeline
for repairs.
Cleaning
All solenoid valves should be cleaned periodically. The time
between cleanings will vary depending on the medium and
service conditions. In general, if the voltage to the coil is correct,
sluggish valve operation, excessive noise or leakage will indicate
that cleaning is required. In the extreme case, faulty valve
operation will occur and the valve may fail to open or close.
Clean strainer or fi lter when cleaning the valve.
Preventive Maintenance
•
Keep the medium fl owing through the valve as free from
dirt and foreign material as possible.
•
While in service, the valve should be operated at least once
a month to insure proper opening and closing.
•
Depending on the medium and service conditions, periodic
inspection of internal valve parts for damage or excessive
wear is recommended. Thoroughly clean all parts. If parts
are worn or damaged, install a complete ASCO Rebuild Kit.
Causes of Improper Operation
•
Incorrect Pressure:
Check valve pressure. Pressure to
valve must be within range specifi ed on nameplate.
•
Excessive Leakage:
Disassemble valve and clean all parts.
If parts are worn or damaged, install a complete ASCO
Rebuild Kit.
Valve Disassembly
(Refer to Figure 3)
1.
Disassemble valve in an orderly fashion using exploded
view for identifi cation and placement of parts.
2.
Remove solenoid enclosure. See separate instructions.
3.
Unscrew solenoid base sub
-
assembly from valve bonnet.
4.
Remove bonnet screws, valve bonnet, solenoid base gasket,
core assembly (with core spring, rider ring and core guide)
and body gasket from valve body.
5.
All parts are now accessible for cleaning or replacement.
If parts are worn or damaged, install a complete ASCO
Rebuild Kit.
Valve Reassembly
1.
Lubricate body gasket and solenoid base gasket with DOW
CORNING
®
200 Fluid lubricant or an equivalent high
-
grade silicone fl uid.
2.
Position body gasket and core assembly in valve body.
3.
Replace valve bonnet, solenoid base gasket and bonnet
screws.
4.
Install bonnet screws and hand thread screws as far as
possible, then torque bonnet screws in a crisscross manner
to 110 ± 10 in
-
lbs [12 ± 1 Nm].
5.
Install solenoid base sub
-
assembly and torque to 175 ± 25
in
-
lbs [19,8 ± 2,8 Nm].
6.
Install solenoid. See separate instructions.
WARNING: To prevent the possibility of
personal injury or property damage, check
valve for proper operation before returning
to service. Also perform internal seat and
external leakage tests (with a nonhazardous,
noncombustible fl uid if practical).
7.
Check valve for external leakage as indicated under the
Piping
section, and for internal (seat
)
leakage as follows.
1
8