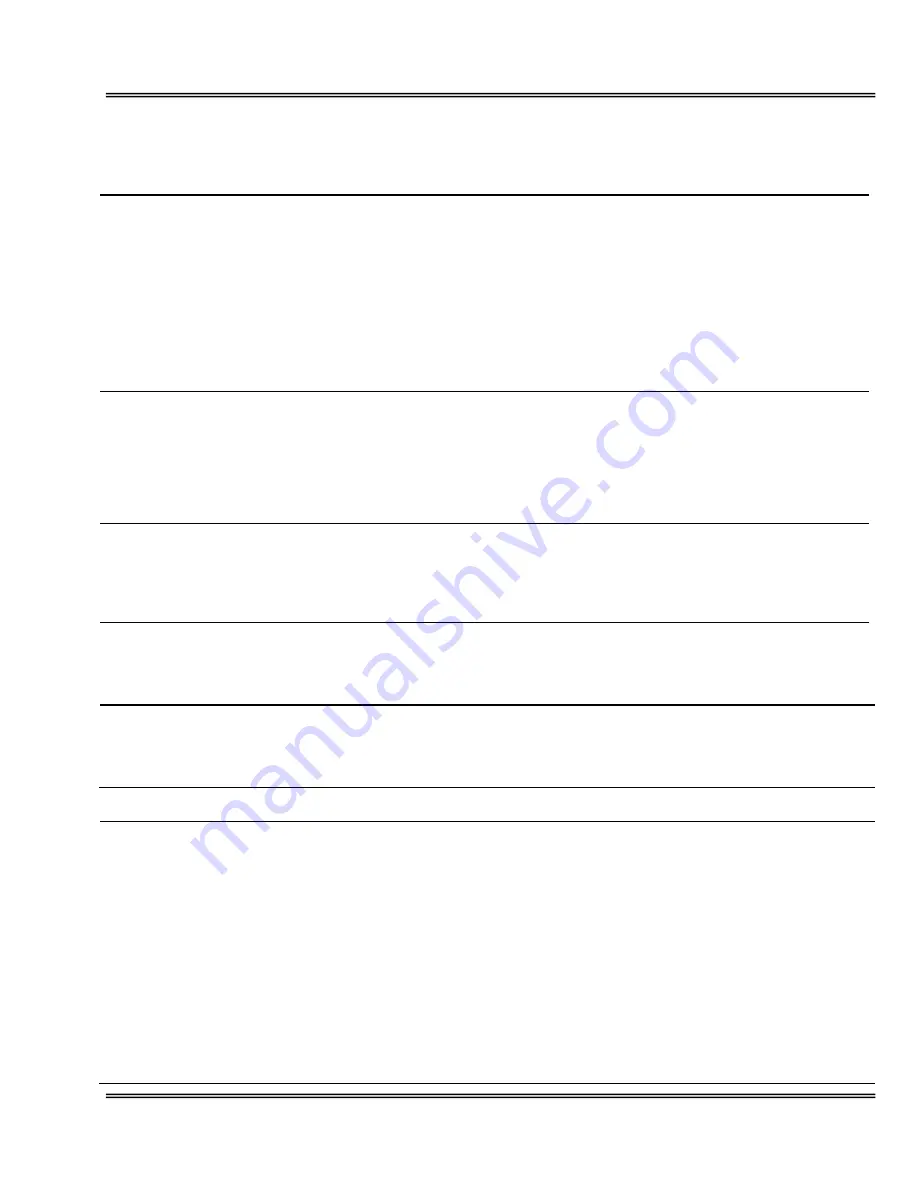
Advanced Instruments Inc.
8 Troubleshooting
Symptom
Possible Cause
Recommended Action
Slow recovery or
At installation, defective sensor
Air leak in sample system connection(s)
Abnormality in zero gas
Damaged in service - prolonged exposure to
air, electrolyte leak
Sensor nearing end of life
Replace sensor if recovery unacceptable or O
2
reading fails to reach 10% of lowest range
Leak test the entire sample system: Vary the flow
rate, if the O
2
reading changes inversely with the
change in flow rate indicates an air leak - correct
source of leak
Qualify zero gas (using portable analyzer)
Replace sensor
Replace sensor
High O
2
reading
after installing
or replacing sensor
Analyzer calibrated before sensor stabilized
caused by:
1) Prolonged exposure to ambient air, worse
if sensor was unshorted
2) Air leak in sample system connection(s)
3) Abnormality in zero gas
Allow O
2
reading to stabilize before making the
span/calibration adjustment
Continue purge with zero gas
Leak test the entire sample system (above)
Qualify zero gas (using portable analyzer)
High O
2
reading
Sampling
Flow rate exceeds limits
Pressurized sensor
Improper sensor selection
Correct pressure and flow rate
Remove restriction on vent line
Replace GPR/PSR sensor with XLT sensor when
CO
2
or acid gases are present
Response time slow
Air leak, dead legs, distance of sample line,
low flow rate, volume of optional filters and
scrubbers
Leak test (above), reduce dead volume or increase
flow rate
O
2
reading doesn’t
agree to expected O
2
values
Pressure and temperature of the sample is
different than span gas
Abnormality in gas
Calibrate the analyzer (calibrate at pressure and
temperature of sample)
Qualify the gas (use a portable analyzer)
Erratic O
2
reading
or
No O
2
reading
Change in sample pressure
Dirty electrical contacts in upper section of
sensor housing
Corroded solder joints on sensor PCB from
corrosive sample or electrolyte leakage from
sensor
Corroded spring loaded contact in upper
section of sensor housing from liquid in
sample or electrolyte leakage from sensor
Sensors without PCB use mV setting.
Calibrate the analyzer (calibrate at pressure and
temperature of sample)
Clean contacts with alcohol (minimize exposure time
of MS sensor to ambient air to extent possible)
Replace sensor and return sensor to the factory for
warranty determination
Upper section of sensor housing: Clean contacts
with alcohol, flow sample or zero gas for 2-3 hours
to flush sample system and sensor housing
Sensor: Replace if leaking and return it to the
factory for warranty determination
32