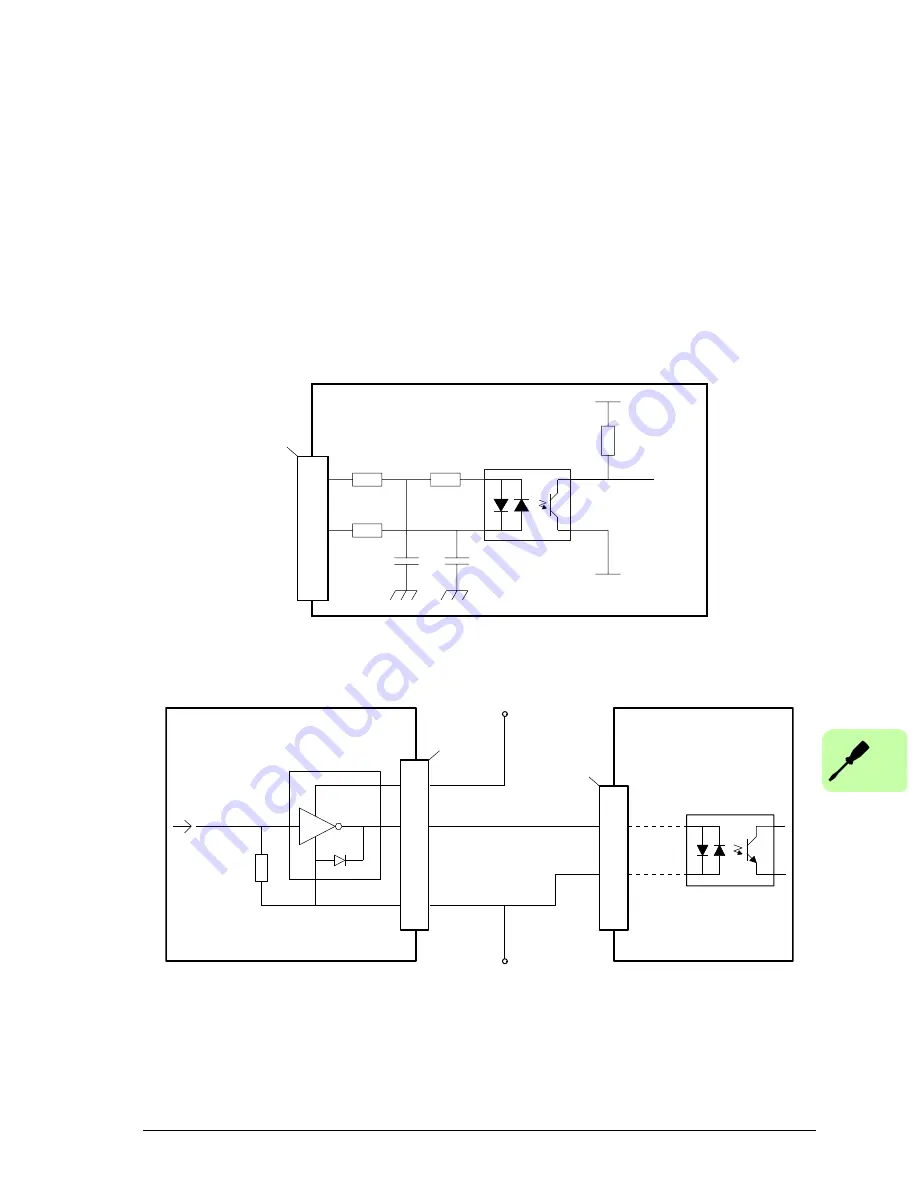
Electrical installation: input / output 65
Digital inputs - general purpose DIN0, DIN3
Location: X3, pins 17 & 7 (DIN0), 15 & 5 (DIN3)
These general purpose digital inputs are buffered by a TLP280 opto-isolator, allowing
the input signals to be connected with either polarity. The inputs do not share a
common reference. When the MicroFlex e150 is connected to Mint WorkBench, the
digital inputs can be configured using the Digital I/O tool. Alternatively, Mint keywords
including
DRIVEENABLEINPUT
,
RESETINPUT
,
ERRORINPUT
and
STOPINPUT
can be
used. The state of the digital inputs can be viewed using the Mint WorkBench Spy
window's Axis tab. See the Mint help file for details.
General purpose digital input - DIN0 shown:
Digital input - typical connections from an ABB NextMove e100:
33R
33R
3k3
Vcc
DGND
17
7
DIN0-
DIN0+
MicroFlex
e
150
X3
TLP280
Mint
UDN2982
Mint
DRIVEENABLEOUTPUT
MicroFlex
e
150
USR GND
DOUT0
DIN0-
17
10k
TLP280
7
10
1
9
DIN0+
USR V+
X11
X3
NextMove e100 / controller
User
supply
24 V
User
supply
GND
Содержание MicroFlex e150
Страница 1: ...ABB motion control User s manual MicroFlex e150 servo drive MN1961WEN ...
Страница 4: ......
Страница 20: ...20 Introduction to the manual ...
Страница 26: ...26 Hardware description ...
Страница 32: ...32 Mechanical installation ...
Страница 42: ...42 Planning the electrical installation ...
Страница 116: ...116 Start up ...
Страница 126: ...126 Fault tracing ...
Страница 152: ...152 Technical data EtherCAT Conformance Test Certificate ...
Страница 162: ...162 Technical data ...
Страница 178: ...178 Appendix Safe Torque Off STO STO function TüV certificate ...