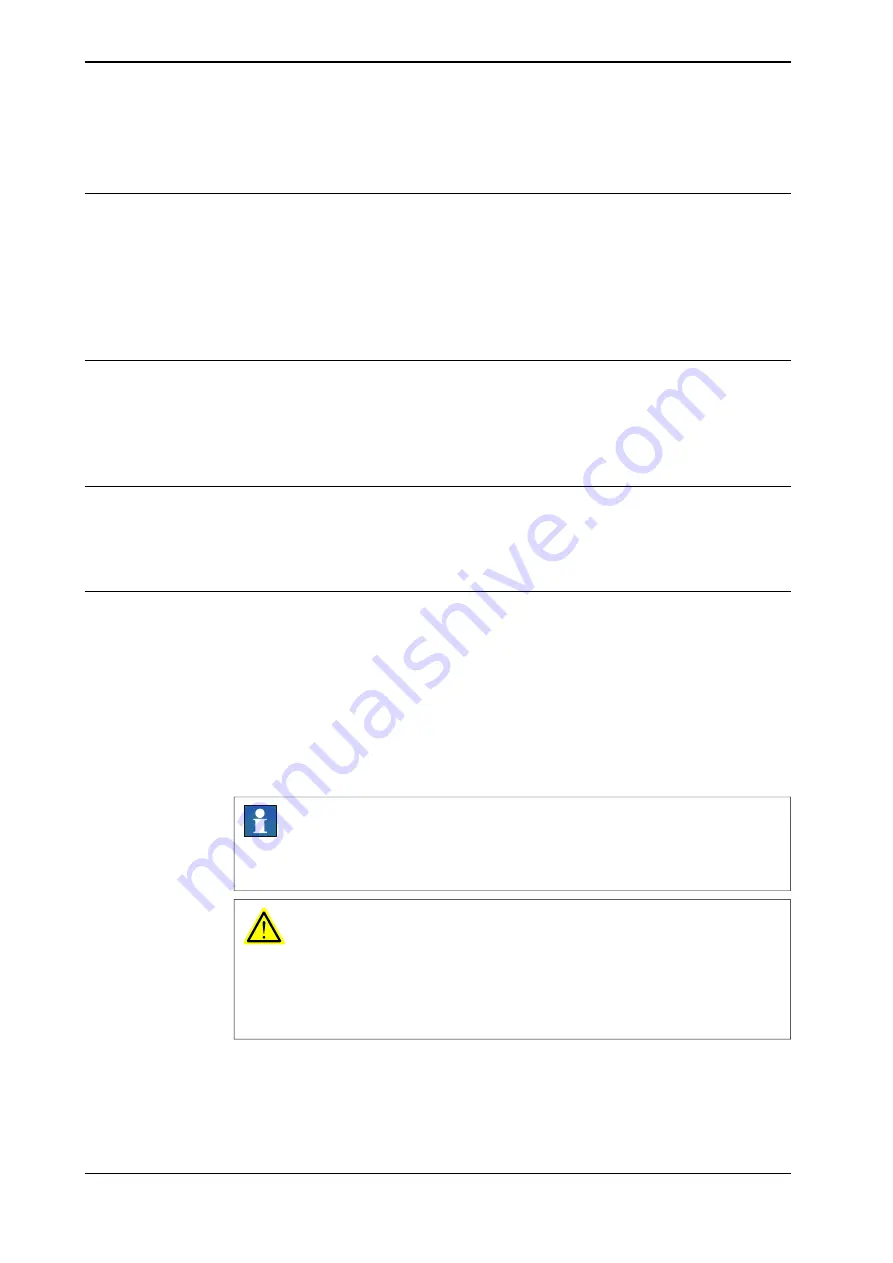
2.2 Installation and operational requirements for Foundry Prime robots
Introduction
Robots with protection type Foundry Prime are specially designed to work in harsh
environments. To ensure that the protection offers the best reliability, special
measures are required during installation and operation. It is required that the
environmental and application conditions are fulfilled and that the special
maintenance activities and intervals for the Foundry Prime protected robot are
followed.
Fluids in the vicinity of the robot
If fluids that can cause rust formation, for example, water etc., are used in the
vicinity of the robot it is required to add rust inhibitor to the fluid or take other
measures to prevent rust on unpainted joints or other unprotected surfaces of the
robot.
Activity to lubricate gearboxes cavities and gears
Run each axis on high speed at least once per hour. This activity will lubricate the
gearbox cavities and gears, which reduces the risk for corrosion due to
condensation in the gearboxes.
Pressurized components
The motors, the balancing device, and the serial measurement board cavity must
be pressurized on Foundry Prime robots during operation and shut down. The
overpressure can be dropped when atmospheric humidity has reached the same
level as the surrounding environment.
At the installation of the Foundry Prime robot a pressure sensor and pressure relief
valve (not included) must be installed in the air supply system to monitor the supply
of air pressure in order to secure a correct pressure. See
for equipment specifications.
Note
The overpressure must be kept at 0.2 - 0.3 ± 0.0 bar during 24 hours independent
of Motors On/Off mode, start-up, and shut down periods.
WARNING
Do not to exceed the maximum pressure of 0.3 bar. If the air pressure exceeds
the specified, it can lead to damage to the gearbox or brake failure in the motors
which may cause the robot arms to fall down, leading to personal injury or physical
damage.
Continues on next page
48
Product manual - IRB 4400
3HAC022032-001 Revision: Q
© Copyright 2004-2018 ABB. All rights reserved.
2 Installation and commissioning
2.2 Installation and operational requirements for Foundry Prime robots
Содержание IRB 4400 - L10
Страница 1: ...ROBOTICS Product manual IRB 4400 ...
Страница 2: ...Trace back information Workspace R18 1 version a9 Checked in 2018 03 22 Skribenta version 5 2 025 ...
Страница 8: ...This page is intentionally left blank ...
Страница 94: ...This page is intentionally left blank ...
Страница 282: ...This page is intentionally left blank ...
Страница 294: ...This page is intentionally left blank ...
Страница 296: ...This page is intentionally left blank ...
Страница 302: ......
Страница 303: ......