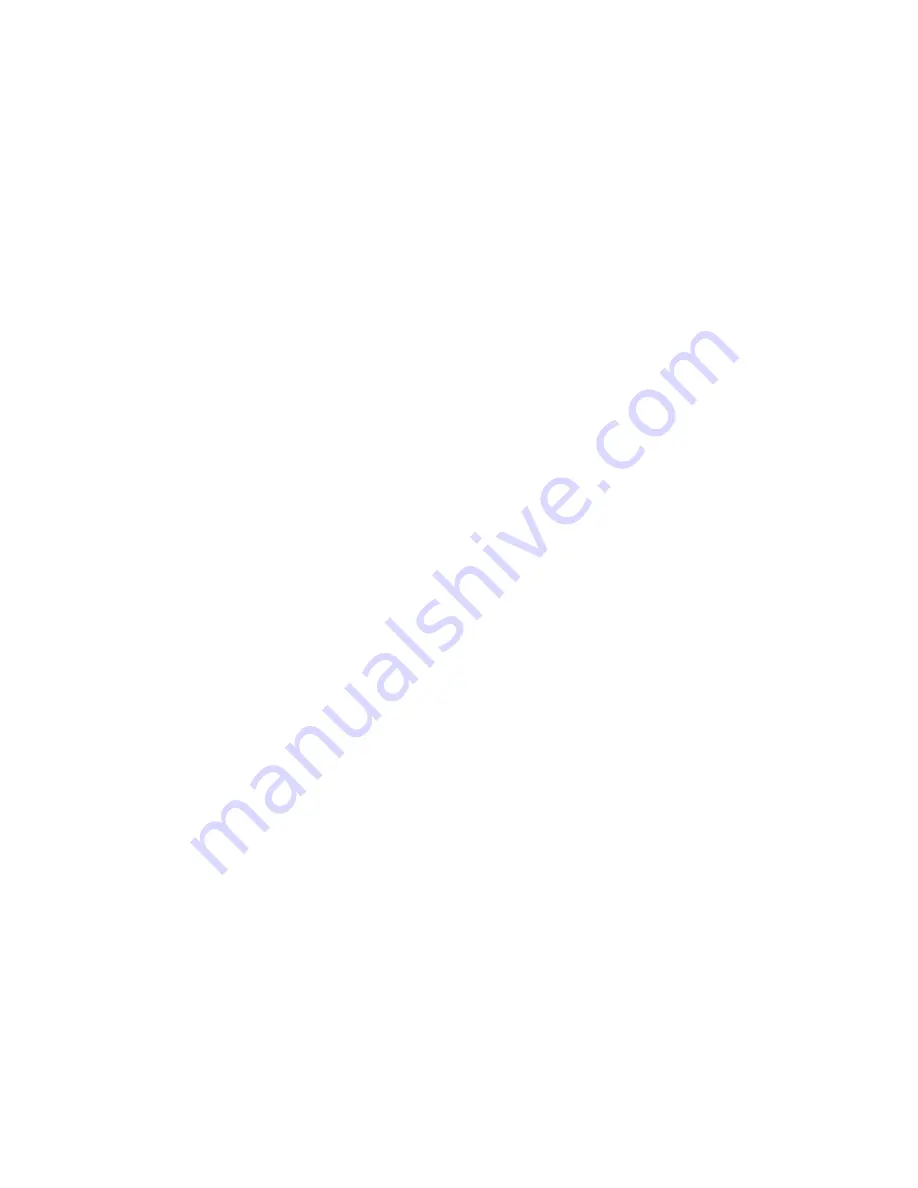
GAA330-M
EMISSION MONITORING SYSTEM | OI/GAA330-M-EN REV. B
83
Index
A
Analyzer cabinet
Visual inspection • 65
Analyzer cabinet electrical connection • 41
Analyzer cabinet installation • 35
Analyzer cabinet problems • 80
Analyzer system
Installation site requirements • 17
B
Back-purging unit
Installation • 34
Installation site and air supply requirements •
20
C
Calibrating the analyzer system • 67
Cancel keys • 56
Checking the seal integrity • 70
Components for automatic back-purging
procedure • 46
Cycle time • 49
D
Display and control unit • 53
Disposal • 82
Dynamic QR code • 76, 81
E
Electrical connection • 36
Emptying the condensate collection bottle • 75
G
Gas analyzer problems • 79
Gas pump problems • 79
Gas sampling with automatic back-purging • 45
I
In general • 45
Installation • 24
Installation preparation • 16
Installing the analyzer system • 16
Intended application • 7
Items delivered • 21
M
Maintenance • 62
Materials needed for installation (not supplied) •
22
Menu tree • 59
N
Notify service • 81
Numeric keypad • 55
O
Operation • 53
P
Password protection • 58
PFE2 Filter unit electrical connection • 38
PFE2 Filter unit gas connection • 27
PFE2 Filter unit installation • 26
PFE3 Filter unit electrical connection • 40
PFE3 Filter unit gas connection • 30
PFE3 Filter unit installation • 29
Post-purge time • 50
Preface • 5
Program sequence • 47
R
Regular maintenance tasks • 63
Replacing the cooling unit / fan outlet filter
mesh • 75
Replacing the filter element in the filter unit • 71
Replacing the suction filter in the diaphragm
pump • 75
S
Safety information • 7, 36, 62
Sample gas cooler problems • 78
Sample gas line installation • 31
Screen • 54
Selecting user interface language • 61
Setting the time zone, date and time • 60
Softkeys • 56
Start of the back-purging procedure • 46
Start-up • 51
Start-up and operation • 51
Status LEDs • 55
Status messages • 78
System description • 10
System design • 12
System overview • 10
T
Troubleshooting • 76
Type 40 probe tube and filter unit installation •
24
Type 42 probe tube and filter unit electrical
connection • 37
Type 42 probe tube and filter unit installation •
25
W
Warm-up phase • 52
Содержание GAA330-M
Страница 2: ......
Страница 43: ...GAA330 M EMISSION MONITORING SYSTEM OI GAA330 M EN REV C 43 ...
Страница 44: ...44 GAA330 M EMISSION MONITORING SYSTEM OI GAA330 M EN REV C ...
Страница 84: ...84 GAA330 M EMISSION MONITORING SYSTEM OI GAA330 M EN REV C Notes ...
Страница 85: ......