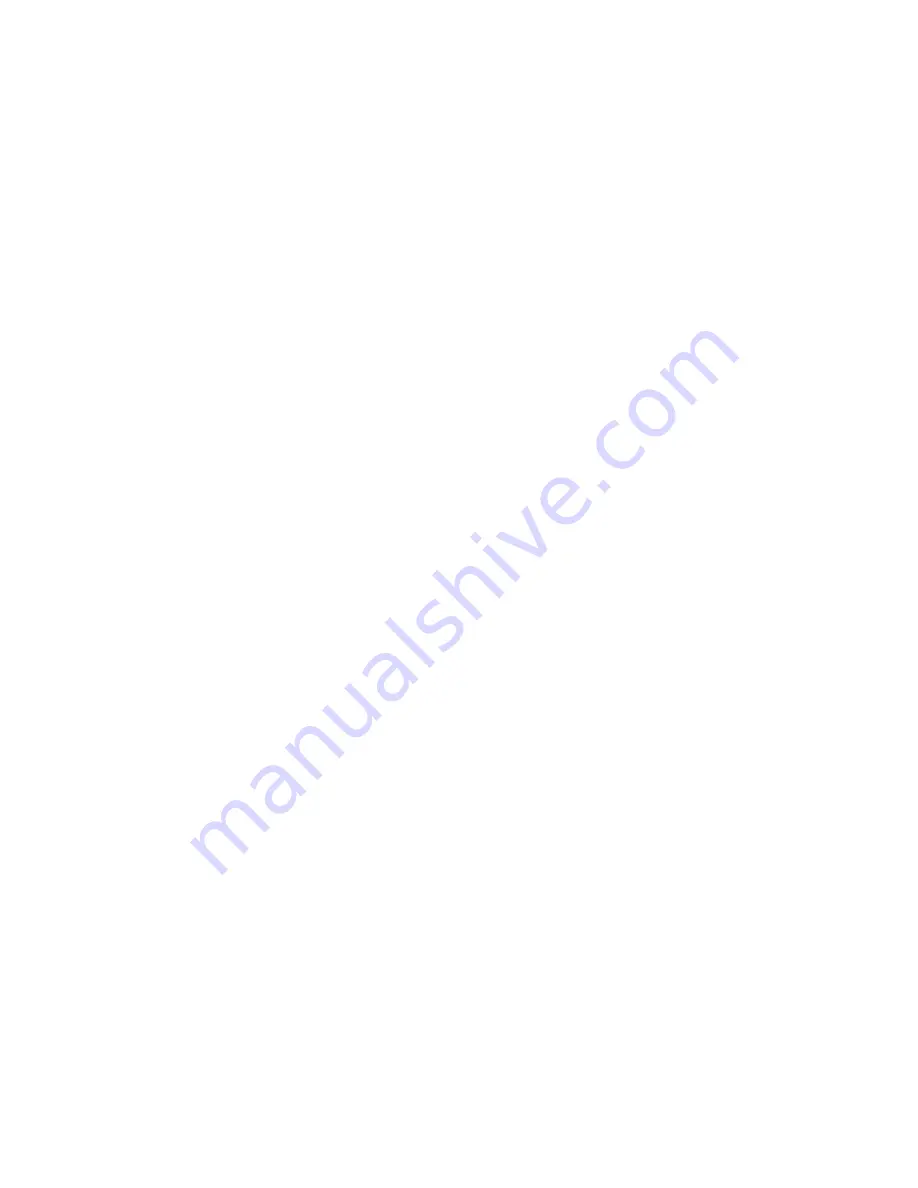
14
GAA330-M
EMISSION MONITORING SYSTEM | OI/GAA330-M-EN REV. C
Cabinet interior
The cabinet contains the sample conditioning components, pump, valves,
filters and gas analyzer. It also contains the main switch, the power supply
and the fuses for all components, as well as the connection terminals for
analog and digital signals.
Gas cooler with condensate collecting bottle
The gas cooler defines the water content of the sample at a certain dew
point (typically 3 °C). Therefore, the temperature of the sample falls from
approx. 180 °C to the set point of the sample gas cooler and condensation
will occur. The condensate is removed with a hose pump and collected in a
separate bottle.
The cooler is controlled by the system and the following signals can be out-
put:
•
Condensate level: The level of the condensate collecting bottle is moni-
tored and a signal will output (displayed via a red LED on the front panel)
when maintenance / emptying the bottle is required.
•
Fault cooler: A status signal "fault cooler" is set (red LED on the front
panel) if the cooler temperature is too high. The signal is also provided
as "Failure" status signal.
•
Failure alarm: If a failure of the cooler is detected, the feed pump is
switched off and the system is set to failure mode. The failure mode is
displayed on the panel and provided as a status signal.
Universal filter, humidity control
The universal filter contains a PTFE filter element with 2 µm fineness to reli-
ably separate solids, in particular extremely fine particles, occurring in analy-
sis techniques in gas filtration. It uses very fine, deep-acting filter elements.
At the bottom of the filter is the humidity controller, which is a conductive
liquid sensor. If this sensor detects humidity, a signal is generated and dis-
played as an illuminated red lamp on the status signal board. Furthermore,
the analyzer pump is switched off.
Sample gas pump
The sample gas pump sucks the sample from the exhaust gas and continu-
ously feeds the gas analyzer with the sample gas. The pump is a diaphragm
pump. If the pump fails a flow alarm occurs. This alarm is displayed on the
front panel and provided as a failure status signal.
Pressure control valve
The pressure control valve ensures a constant sample flow to the gas ana-
lyzer. This means, the valve stabilizes the outlet pressure of the sample
pump by returning some sample gas to the pump inlet. Thus, if the pressure
at the pump outlet drops, the valve reduces the returned gas volume to in-
crease the pressure at the outlet.
Flow control
The flow meters monitor the sample gas flow through the analyzer. The
following parameters are considered:
•
Typical flow: 60 l/h
•
Minimum flow level: 40 l/h
•
Maximum flow level: 80 l/h
If the flow violates a limit value an alarm is displayed on the front panel. In
addition, the sample probe is automatically back-purged.
Содержание GAA330-M
Страница 2: ......
Страница 43: ...GAA330 M EMISSION MONITORING SYSTEM OI GAA330 M EN REV C 43 ...
Страница 44: ...44 GAA330 M EMISSION MONITORING SYSTEM OI GAA330 M EN REV C ...
Страница 84: ...84 GAA330 M EMISSION MONITORING SYSTEM OI GAA330 M EN REV C Notes ...
Страница 85: ......