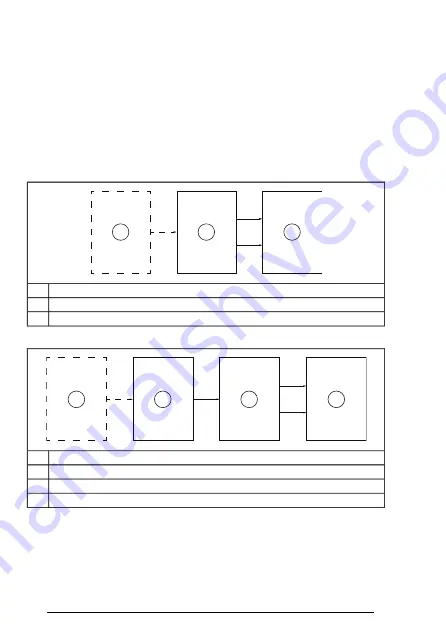
Safety block diagrams
The components that are included in the safety data calculations are
shown in the safety block diagrams below.
Note:
The failure rate of the PTC sensor is not included in the
calculations.
■
Two-channel configurations
This diagram is applicable to configuration 1.
1
2
3
PTC sensor
1
FPTC module
2
Drive STO
3
This diagram is applicable to configuration 2.
1
2
3
4
PTC sensor
1
FPTC module
2
FSO module
3
Drive STO
4
84 Technical data
Содержание FPTC-02
Страница 2: ......
Страница 4: ......
Страница 23: ... Layout 1 1 2 4 3 XSTO2 XSTO1 XWRN XFLT Retaining clips 1 Lock 2 Hardware description 23 ...
Страница 28: ...28 ...
Страница 37: ...2 3 1 4 Mechanical installation 37 ...
Страница 38: ...38 ...
Страница 48: ...48 ...
Страница 64: ...64 ...
Страница 70: ...70 ...
Страница 78: ...78 ...
Страница 89: ...Technical data 89 ...
Страница 90: ...90 Technical data ...
Страница 92: ...92 Technical data ...
Страница 93: ...Check the latest version of the certificate in the ABB Library Technical data 93 ...