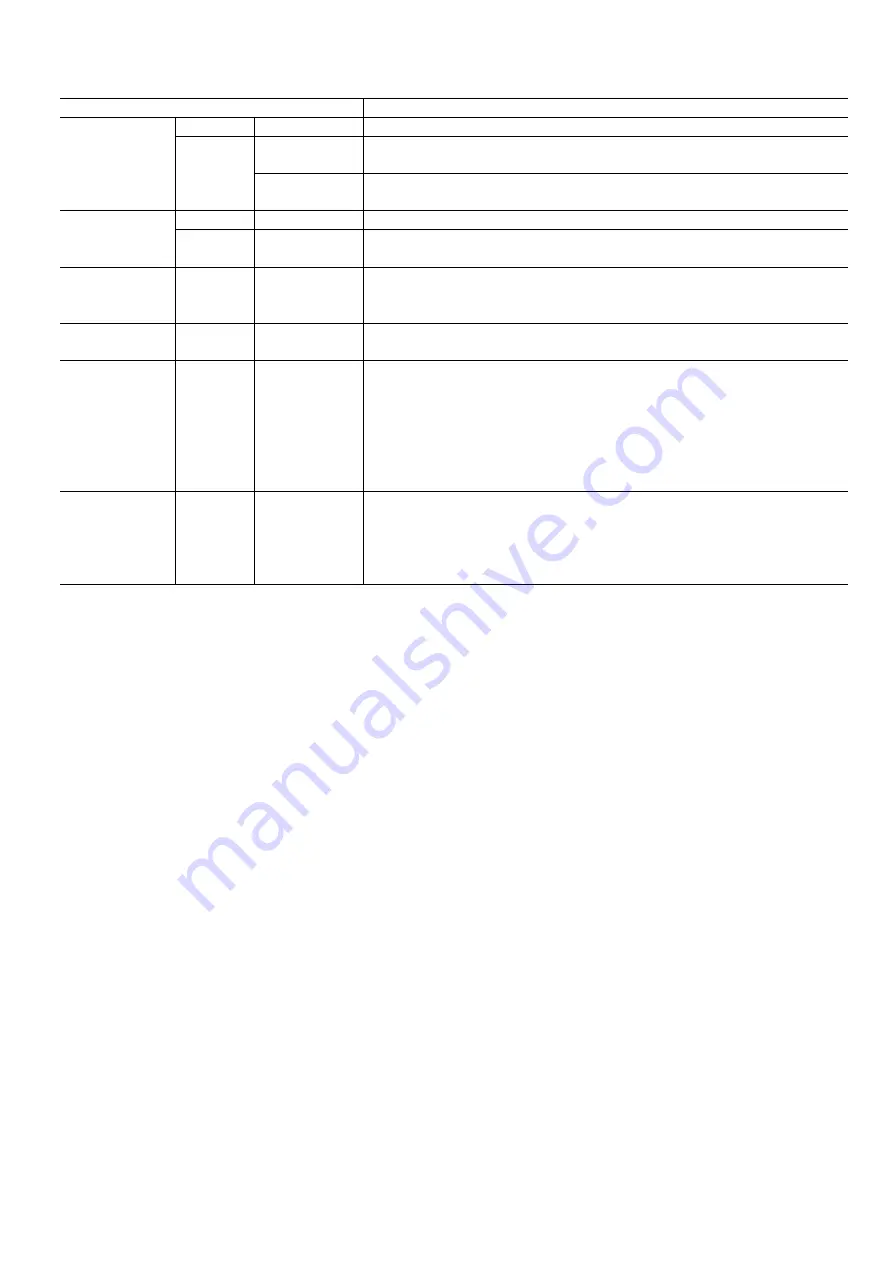
41
2 6 6 H S H MODBUS TR A N S M IT TE R |
P R E SSU R E/ T EM P ER AT U R E M U LT I VA R I A B L E | O I/ 2 6 6 H SH M T- EN R E V. A
— Respect the below table indications for reinstalling the process flanges.
T
ransmitter model and range
Procedure
266DSH / PSH / VSH
Viton Gaskets All bolting
Use a torque wrench to tighten the bolts to a torque of 25 Nm.
PTFE Gaskets
Carbon Steel NACE
and Stainless Steel
Use a torque wrench to tighten the process flange nuts to a torque of 40 Nm, let the flange
stabilize for an hour, unscrew the nuts and tighten again to 25 Nm.
Stainless Steel
NACE
Use a torque wrench to tighten the process flange nuts to a torque of 25 Nm, let the flange
stabilize for an hour and perform the final tightening to 25 Nm.
266DSH.x.H
(High static option)
Viton Gaskets All bolting
Use a torque wrench to tighten the bolts to a torque of 31 Nm.
PTFE Gaskets All bolting
Use a torque wrench to tighten the process flange nuts to a torque of 40 Nm, let the flange
stabilize for an hour, unscrew the nuts and tighten again to 31 Nm.
266DSH range A
(1KPa)
All gaskets
All bolting
Use a torque wrench to tighten the process flange screws/nuts to a torque of 14 Nm.
Please be aware that in case of bottom work disassembly and reassembly the original
performances can not be guarantee anymore.
266DSH / 266PSH
with Kynar inserts
All gaskets
All bolting
Use a torque wrench to tighten the process flange screws/nuts to a torque of 15 Nm
266MSx / 266RSx
MWP ≤ 41Mpa /
410bar / 5945 psi
All gaskets
All bolting
First, use a torque wrench to tighten the process flange screws/nuts to a joining
torque of — MJ = 2 Nm (0.2 kpm), working in a crosswise manner.
— Then tighten them with a torque MJ = 10 Nm (1.0 kpm), working in a crosswise
manner — Then tighten them fully by turning each nut or screw again (in a
crosswise manner) by the tightening angle A = 180°, working in two stages of 90°
each. Some transmitter versions are using screws with size M10. If this screws are
used the tightening angle A = 270°, working in three stages of 90° each.
266MSx / 266RSx
MWP 60Mpa /
600bar / 8700 psi
Perbunan
All bolting
First, use a torque wrench to tighten the process flange screws/nuts to a joining
torque of — MJ = 2 Nm (0,2 kpm), working in a crosswise manner.
— Then tighten them with a torque MJ = 10 Nm (1,0 kpm), working in a crosswise
manner — Then tighten them fully by turning each nut or screw again (in a crosswise
manner) by the tightening angle A = 180°, working in two stages of 90° each.
9.4 Pressure transducer replacement
If the pressure transducer needs to be replaced proceed as
follows:
1. Insulate the transmitter from the process by acting on
the manifolds or on the insulation valves.
2. Open the vent valves to allow sensor depressurization.
3. Disconnect the power supply and disconnect the
wiring.
4. Disconnect the transmitter from the bracket
unscrewing the fixing bolts.
5. Open the communication board compartment cover.
6. The communication board is connected to the sensor
via a flat cable and a connector. Remove the
communication board and gently disconnect the
connector.
7. Release the tang screw until nd rotate the housing until
its complete removal.
8. Unscrew the fixing bolts from the transducer and
remove the process flanges.
9. The orings placed between the diaphragm and the
flange (Viton or PTFE) must be replaced after every
disassembly.
10. Reassemble the flanges following the steps above in
reverse order.
11. The 266 can reconfigure itself with the previous
configured parameters thanks to the auto-
configuration functionality.
12. Before powering on the transmitter raise dip-switches
1 and 2 in up position. Connect the transmitter to
power supply, wait ten seconds and lower dip-
switched 1 and 2.
13. After installing the transmitter on the bracket and
connecting it to the manifold, perform a PV zero bias.
9.5 Electronic replacement
If the electronic module needs to be replaced proceed as
follows:
1. Insulate the transmitter from the process by acting on
the manifolds or on the insulation valves.
2. Open the vent valves to allow sensor depressurization.
3. Disconnect the power supply and disconnect the
wiring.
4. Open the communication board compartment cover
and remove the LCD display (if installed).
5. Remove the communication board and gently
disconnect the connector.
6. Connect the sensor flat cable to the new electronic
module with dip switch 1 in up position.
7. Connect the transmitter to power supply, wait ten