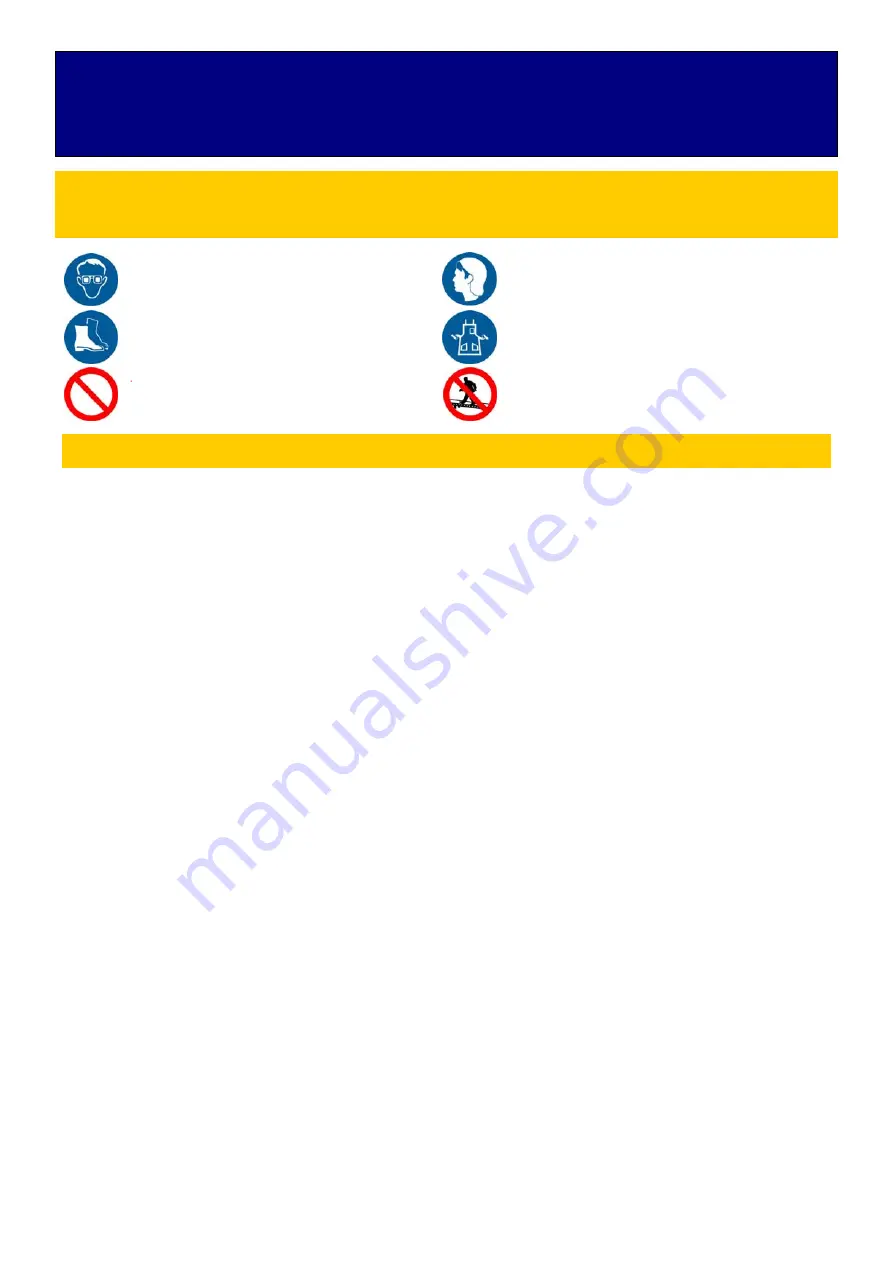
This
Safety Operating Procedure
does not necessarily cover all possible hazards associated with the machine and should be used in conjunction with
other references
. It is designed to be used as an adjunct to the operation in the safety procedures and to act as a reminder to the operatior prior to
machine use.
SAFETY OPERATING PROCEDURES
Vehicle Hoist
DO NOT
use this machine unless the operator has been
thoroughly instructed in its safe use and operation.
Safety glasses must be worn at all
times in work areas.
Long and loose hair must be
contained.
Sturdy footwear must be worn at all
times in work areas.
Close fitting/protective clothing must
be worn.
Rings and jewellery must not be
worn.
Do not stand on hoist whilst hoist is in
operation.
A vehicle hoist must not be operated unless it has a current certificate of inspection.
PRE-OPERATIONAL SAFETY CHECKS
1. Ensure that vehicle hoist has operating and maintenance instructions permanently located
and clearly visible.
2. The equipment must be used in accordance with manufacturer’s instructions.
3. Check the capacity of the hoist compared to the weight of the vehicle. If vehicle is too
heavy, do not proceed.
4. Ensure the area is clean and clear of grease, oil, and objects that may be a slip/trip hazard.
5. Familiarise yourself with and check all machine operations and controls.
6. Check all safety devices are in good condition.
7. Ensure support arms are capable of being locked in position.
8. Ensure rubber pads are in good condition on all load points.
9. Faulty equipment must not be used. Immediately report suspect equipment.
OPERATIONAL SAFETY CHECKS
1. Centre vehicle on hoist, ensuring that the weight is evenly distributed to the front and rear.
2. Identify the correct jacking points.
3. Only one person shall operate the hoist at a time.
4. Ensure hoist area is clear of people and equipment before operating.
5. Never leave the hoist running unattended.
6. Check vehicle stability by looking at the jacking points.
7. Engage and check for the correct engagement of the locks.
8. At the completion of work lower the vehicle hoist and ensure all equipment is left in a safe
position.
HOUSEKEEPING
1. Switch off equipment.
2. Leave the equipment and work area in a safe, clean and tidy state.
POTENTIAL HAZARDS
Falling objects
Trapping hazards
Crushing
hazards
Entanglement
hazards
Содержание AL-6214A
Страница 15: ...14 Installation Operation and Parts Manual AutoLift AL 6214 Annex2 Overall diagram ...
Страница 16: ...15 Installation Operation and Parts Manual AutoLift AL 6214 Annex3 Floor plan ...
Страница 18: ...12 ...
Страница 19: ...12 Installation Operation and Parts Manual AutoLift AL 6214 Three phase ...
Страница 20: ...12 Installation Operation and Parts Manual AutoLift AL 6214 ...