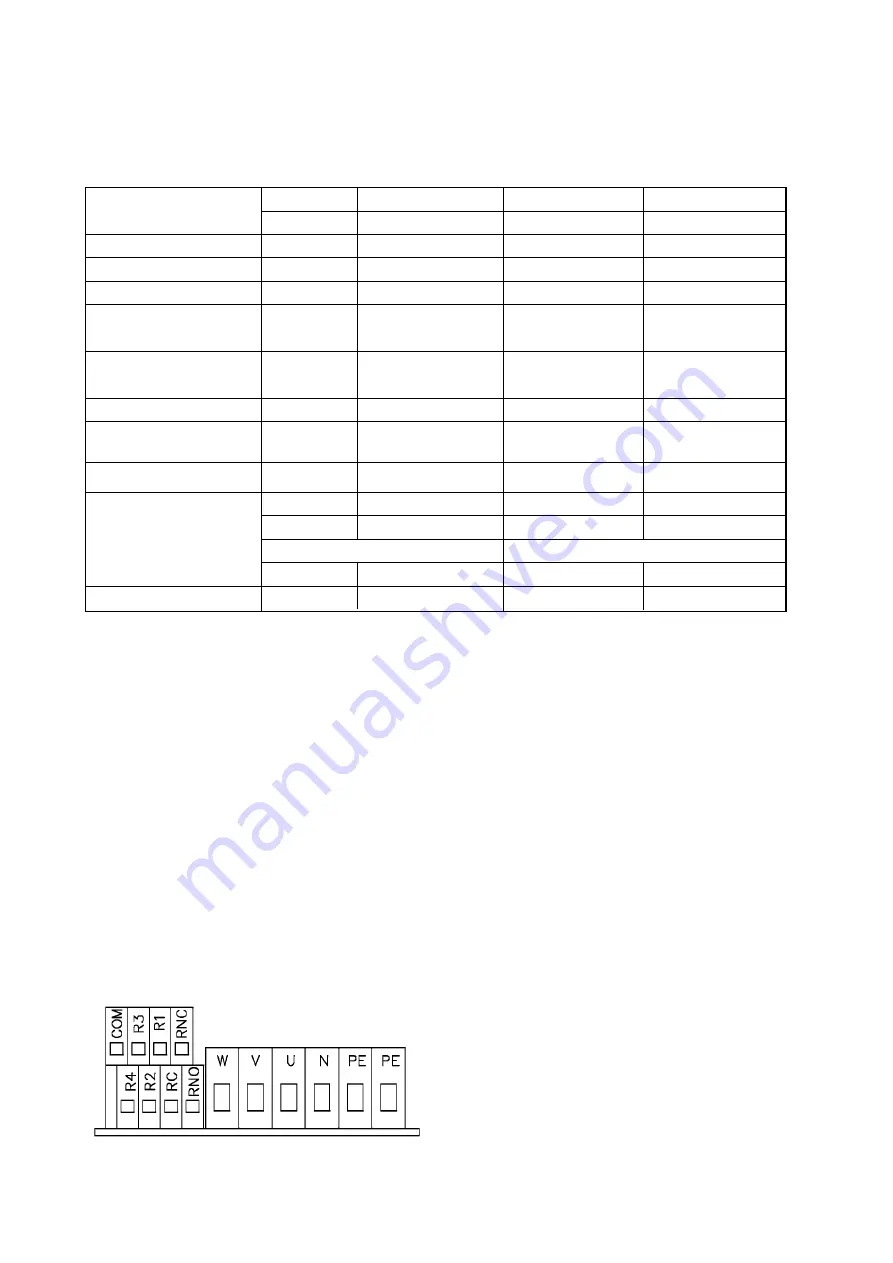
25
Terminals on source board
– The autocalibration is started by push-button
Start in program DMS2.
– Wait until the autocalibration is completed; information on its course is signalized next to push-button Start.
Other parameters
Check and, if necessary, change other parameters:
Control signal
4 – 20 mA
20 – 4mA
0 – 20 mA
20 – 0 mA
2 position
Bus
Insensitivity
1 – 1 0 %
Function SAFE
Open
Close
Stop
To position
Active SAFE
0 V
230 V
Time of blocking torque
in end-limit positions
0 – 20 s
Position of blocking torque
in end-limit positions
1 – 10 %
Output of position signal
4 – 20 mA
20 – 4 mA
READY function
Combined
error
Error code
Ready – Local
Switched off Switched on
Switched off Position O
Position Z
Torque O
Torque Z
Relay 1 – 4
Torque and position O
Torque and position Z
Opening
Closing
Movement
Position Relay 1 – 4
0 – 100%
Note:
SAFE – input information on the error of an external device can be set so that the actuator would respond as to its
own error.
Autodiagnostics
The table List of errors – same as for electronics DMS2 ED
(page 13)
Memory of number of induced errors
– same as for the DMS2 ED electronics
Memory of recently induced errors
– DMS2 stores 3 recently induced errors to the memory EEPROM.
– DMS2 provides for displaying the errors by means of the PC program or the switches of the local/ remote control.
– Reading and clearing of the counters with the local / remote control switches:
– Display – OFF position and the O or C position.
– Reset – after switch from errors to remote control.
Terminal board of actuator with electronics DMS2
– Terminals on source board