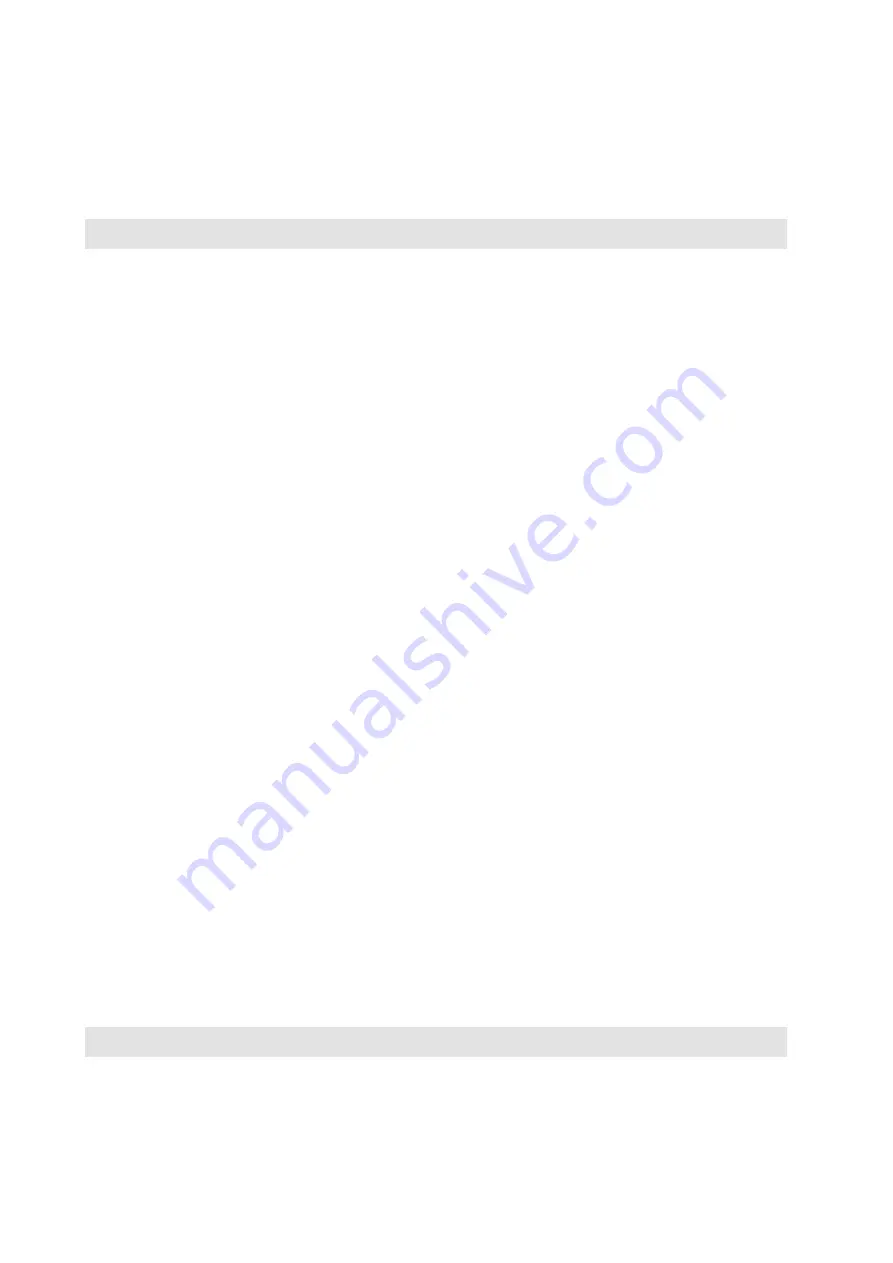
15
MENU 8 – Way of switching off in end-limit positions in 3P regulation
– Shortly press
P to select value TORQUE
- 1x blinking of LED2,
or PO
- 2x blinking of LED2,
or PZ
- 3x blinking of LED2,
or PO+PZ
- 4x blinking of LED2
and keep pressing push-button
P to store the parameter to memory.
PROCEDURE OF SETTING PARAMETERS BY PROGRAM DMS2
– Before starting the actuator, it is necessary to set some parameters of the system by means of program DMS2 on PC.
– For safety reasons, the system is delivered in the state of induced error of Calibration when the functions are limited in
order to reduce the risk of damaging the actuator by wrong wiring. In controlling the actuator from program DMS2, its run is
stopped when any torque is induced.
Working torque
– Check and, if necessary, set the value of working torque 50 – 100 % in program DMS2.
End-limit positions – working stroke
Position Z
– Shift to position Closed either manually or by means of menu Motor in program DMS2.
– The actuator can only be controlled by means of the program if no torque is induced. The torque should be left manually.
– Press push-button
Z to confirm consent with the record.
Position O
– Shift to position Open either manually or by means of menu Motor in program DMS2.
– The actuator can only be controlled by means of the program if no torque is induced. The torque should be left manually.
– Press push-button
O to confirm consent with the record.
Autocalibration (CONTROL only)
– The autocalibration can only be started by means of the program if no torque is induced. The torque should be left
manually.
– The autocalibration is started by push-button Start in program DMS2.
– Wait until the autocalibration is completed; information on its course is signalized next to push-button
Start.
Other parameters
Check and, if necessary, change other parameters:
Control signal
4 – 20 mA, 20 – 4 mA, 0 – 20 mA, 20 – 0 mA
Insensitivity
1 – 10 %
Function in case of error
open, close, stop, to position
Time of torque blocking in end-limit positions
0 – 20 s
(default 5s from producer)
Position of torque blocking in end-limit positions
1 – 10 %
Output of position signal
4 – 20 mA, 20 – 4 mA
Function READY
combined error
Note:
Signal READY is brought out as contact of the relay on the terminal board. If the state ERROR or WARNING is
not detected (setting can be made of what is to be evaluated as error or warning), the contact is closed; in case of error,
warning, or if feeding of electronics is interrupted, the contact is opened. The state of the relay READY is indicated by the
LED diode on the source board.
AUTODIAGNOSTICS
DMS2 ED performs continuously its diagnostics and, if a problem is detected, it reports warning or error. The
warning or error is signalized by LED of the display and, possibly, by relay Ready. The warning has no effect on
operation of the system, the error stops the actuator.
Assigning or switching off of warnings and errors is set in window
“Warning and error”
of the setting program
(it is opened by clicking one of parameters Warning 1 – 4 or Error 1 – 4 in window “Parameters”).