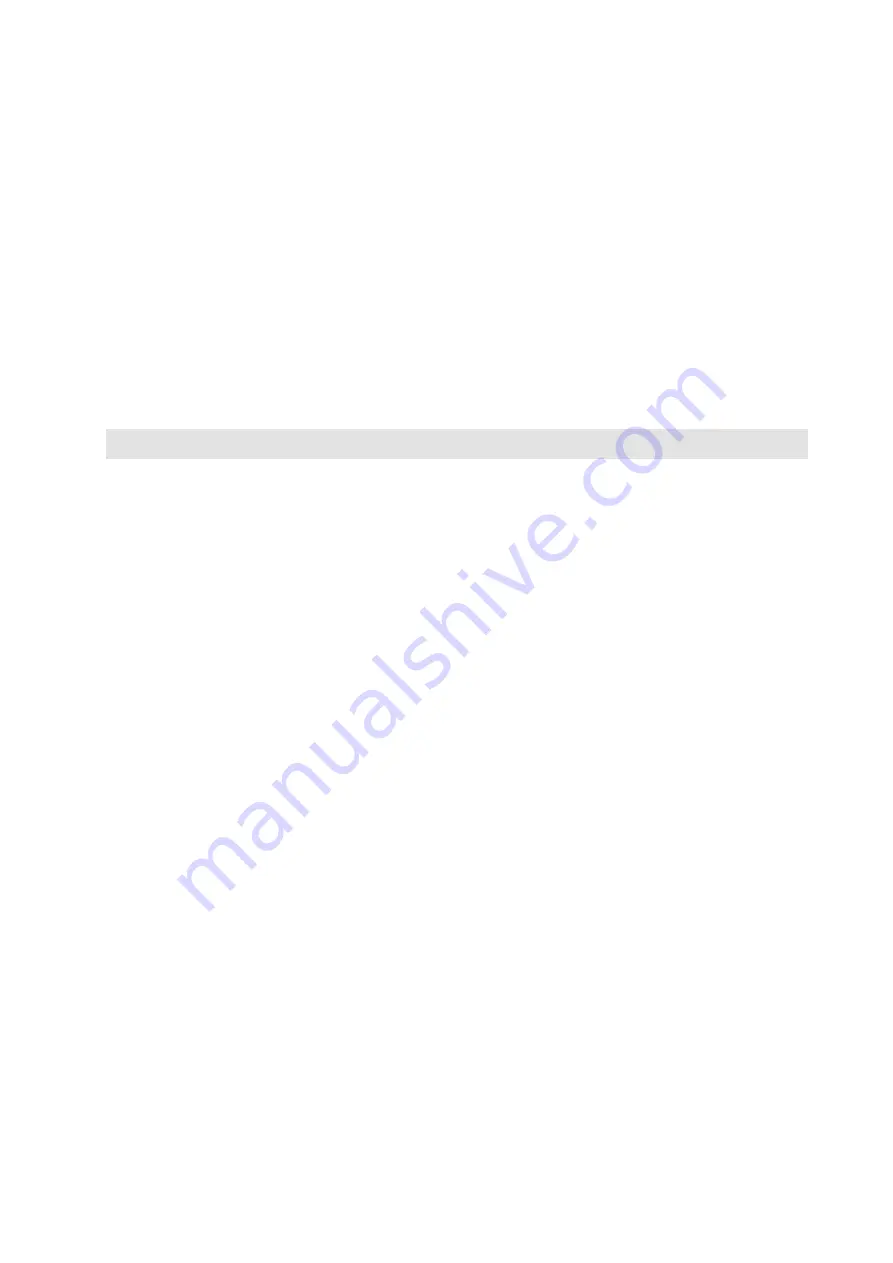
24
Technical parameters of DMS2 electronics:
Scanning of position
contact-less, magnetic
Scanning of torque
contact-less, magnetic
Working stroke see
90°
Torque blocking
0 – 20 s at reversing in limit positions
Input signal
0
(4)
– 20 mA with switched on 3P regulator function
Open, Close 15 – 60 V AC/DC with switched on 2P
regulator function
Safe 15 – 60 V AC/DC
Local/remote control, local open, stop, local close
Output signals
5 x relay 250 V AC 3A
(R1, R2, R3, R4, READY)
Position signal 4 – 20 mA, max. 500
Ω
,
active/passive, galvanic-isolated
LCD display 2 x 12 alpha-numeric characters
Power supply
230 V AC, 50 Hz, 4 W, over-voltage category II
Monitoring the presence and sequence of a phase
PROCEDURE OF SETTING PARAMETERS BY PROGRAM DMS2
Before putting the actuator into operation, it is necessary to set some parameters of the system by means of
program DMS2 on PC.
Warning:
For safety reasons (reduced risk of damage to the actuator by wrong wiring), the system is delivered in the state of
the induced error of calibration when the functions are limited and, during controlling the actuator from program DMS2,
its run is stopped if any torque is induced.
Note:
The setting program is the same for electronics DMS2 ED. See the figure on page 12 for the main window
and the window of Selection of electronics.
Working torque
– Check and, if necessary, set the value of the working torque 50 – 100 % in DMS2 program.
Tripping in end-limit positions
– Check and, if necessary, set the way of tripping in the end-limit positions:
– Torque
– position O
– position Z
– position O+Z
End-limit positions – working stroke
– Position Z
– Shift to position Closed either manually or by means of menu Motor in program DMS2.
– The actuator can only be controlled by means of the program
if no torque is induced. The torque should be
left manually.
– Press
push-button Z to confirm consent with the record.
– Position O
– Shift to position Open either manually or by means of menu Motor in program DMS2.
– The actuator can only be controlled by means of the program
if no torque is induced. The torque should be
left manually.
– Press
push-button O to confirm consent with the record.m.
Autocalibration
– The autocalibration can only be started by means of the program
if no torque is induced. The torque should be
left manually.