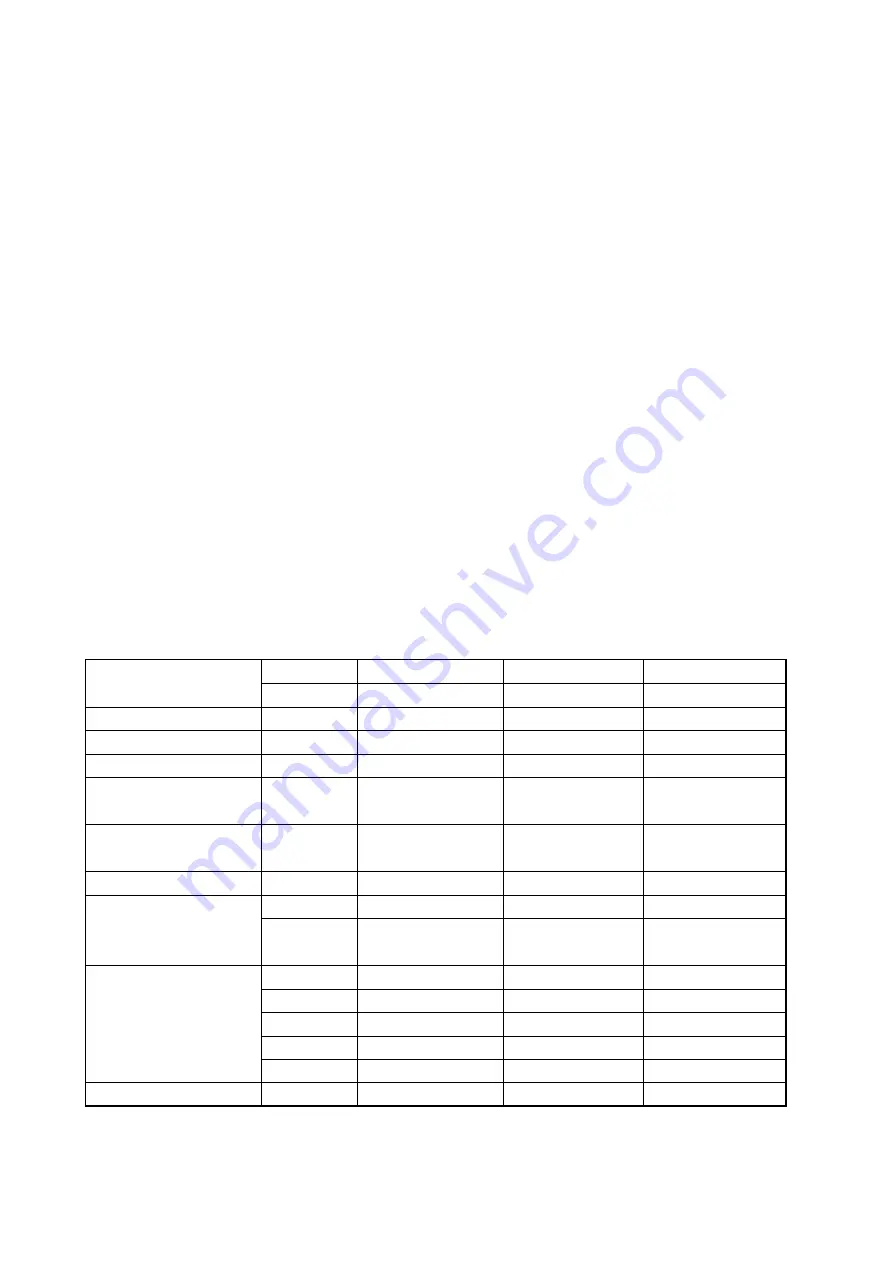
21
Working torque
– Check and, if necessary, set the value of the working torque 50 – 100 % in program DMS2.
Tripping in end-limit positions
– Check and, if necessary, set the way of tripping in the end-limit positions::
– Torque
– position O
– position Z
– position O + Z
End-limit positions - working stroke
– Position
Z
– Shift to position Closed either manually or by means of menu Motor in program DMS2.
–
The actuator can only be controlled by means of the program if no torque is induced. The torque should be left
manually.
– Press push-button Z to confirm consent with the record.
– Position
O
– Shift to position Open either manually or by means of menu Motor in program DMS2.
–
The actuator can only be controlled by means of the program if no torque is induced. The torque should be left
manually.
– Press push-button O to confirm consent with the record.
Autocalibration
–
The autocalibration can only be started by means of the program if no torque is induced. The torque should be left
manually.
– The autocalibration is started by push-button Start in program DMS2.
– Wait until the autocalibration is completed; information on its course is signalized next to push-button Start.
Other parameters
Check and, if necessary, change other parameters:
Control signal
4 – 20 mA
20 – 4mA
0 – 20 mA
20 – 0 mA
2
position
Bus
Insensitivity
1 – 1 0 %
Function SAFE
Open
Close
Stop
To position
Active SAFE
O V
230 V
Time of blocking torque
in end-limit positions
0 – 20 s
Position of blocking torque
in end-limit positions
1 – 10 %
Output of position signal
4 – 20 mA
20 – 4 mA
Function READY
Switched off
Warning
Errors
Warning or error
- Combined error
Errors or not
Errors or warning
Torque “O” or “Z”
remote or
not
remote
Switched off
Position O
Position Z
Torque O
Torque Z
Torque and position O Torque and position Z
Relay 1 – 4
Opening
Closing
Motion
Position
position N
Local control
Emote control
Control switched off
Torque O/Z
Motion - blinker
Position Relay 1 – 4
0 – 100 %
Note:
SAFE - input information on the error of an external device can be set so that the actuator would respond as to
its own error.
Summary of Contents for MODACT MO EE 52 120
Page 2: ......
Page 25: ...25 Terminal board of DMS2 Analog Terminal board of DMS2 Profbus...
Page 49: ...NOTES...
Page 50: ...NOTES...