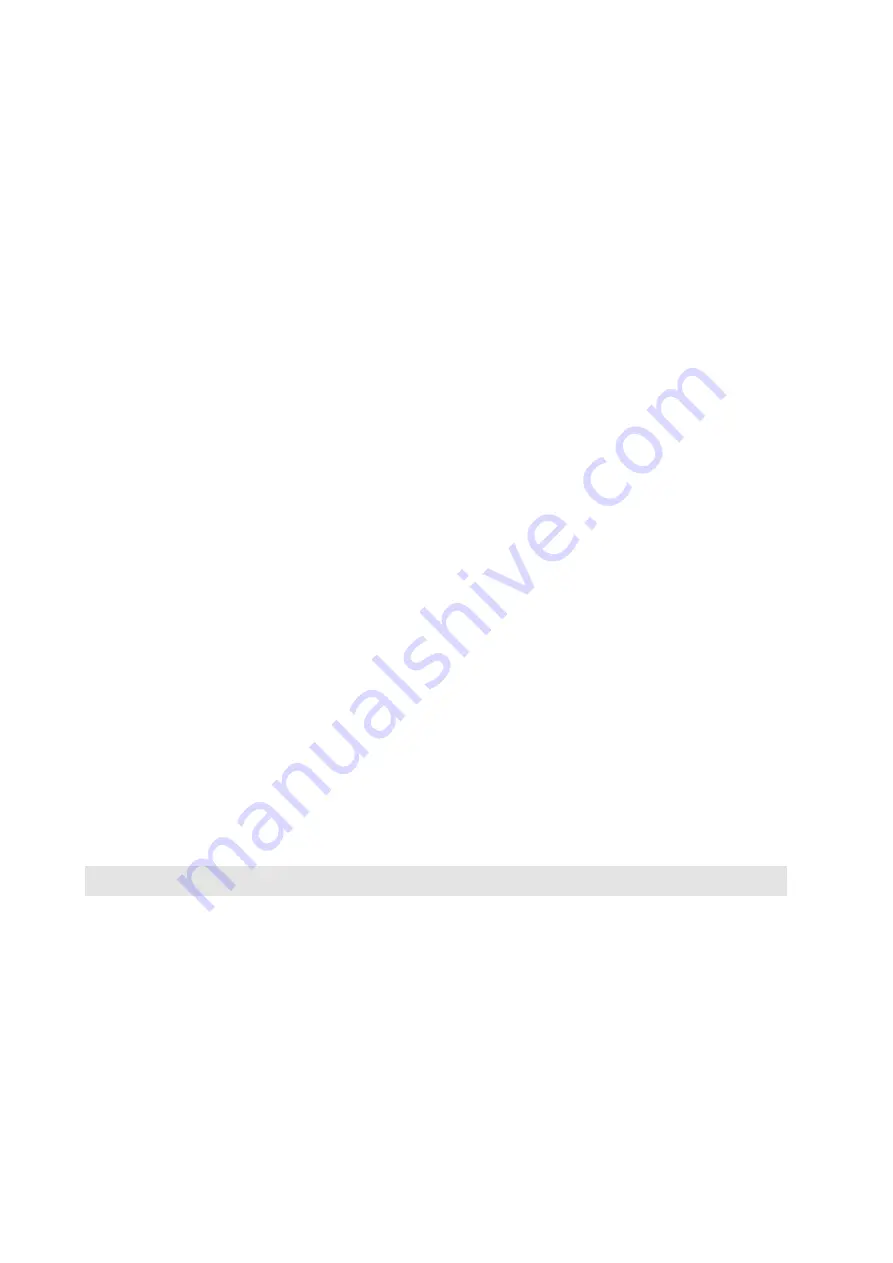
43
Limiting conditions:
1.
Cable bushings OS and O can only be used for braided cables and firm instruments; the cable should be
properly fixed to prevent its possible pulling out or twisting.
2.
Operating temperature of the cable bushing is -60 °C to +80 °C.
3.
The space between the equipment and the cable bushing should be sealed in order to preserve particular
degree of protection against penetration of dust, solid particles, and water.
Accessories:
Before assembling or dismounting the cable bushing, become familiar with accessories of the cable bushing
which include, for instance:
– coat providing additional protection against corrosion;
– safety nut securing position of the cable bushing;
– sealing washer under the additional protection of the cover of the cable bushing front part against pene-
tration;
– knurled washer damping vibrations that could loosen the safety nut or the cable bushing assembly
The inlet to the actuator and connection to its switching, protection and securing instruments can only be
installed by technicians with particular qualification who must follow pertaining standards and wiring diagrams
as provided in these Instructions for Use. After connecting the inlet cables, all screws of the connecting termi-
nals should be checked for tightness so that they do not get warm during operation due to increased transition
resistance. The connecting terminals must not be under tension or bending stress from the connected conduc-
tors. In case of connection with aluminium conductors the following measures are recommended. One-step
before connecting the conductor, the oxidized layer should be removed from the conductor and new oxidation
should be prevented by smearing the connection with a neutral vaseline.
After the connection, make sure, by short starting of the actuator in the intermediate position of the working
stroke, that the output shaft of the actuator rotates in a proper direction. If this is not the case, reconnect any
two conductors on the terminals U, V, W of the motor
(actuator)
terminal board. Then, repeat the functional
check. After verifying correct electric connection, the actuator is fitted to the valve and adjusted according to
the paragraph Actuator Setting. The adjustment is best carried out using the manual control regime.
Important warning!
1) During adjusting, repair, and maintenance, secure the actuator in the prescribed way in order to rule out its
connection to the power supply and thus to prevent possibility of an injury due to electric shock or the actuator
rotation.
After adjusting the actuator, check its function using the control circuit. In particular, make a check that the
actuator is correctly starting and that there is no voltage on the electric motor after particular relays has been
switched off. If this is not the case, switch the actuator power supply immediately so that damage to the electric
motor is prevented, and seek for the failure.
9) OPERATION AND MAINTENANCE
Depending on the operating conditions, the operation of rotary actuators usually involves only the transmission of
pulses, as required for the individual functions. In the event of a power supply failure, readjust the controlled device by
the handwheel. If the actuator has been connected in the circuit of automatic equipment
(which does not imply
the control mode)
it is advisable that manual remote control units are connected in the circuit so that the actuator can
be controlled even if a failure of the automatic equipment occurs.
It is the operator’s duty to ensure that the actuator is given the prescribed maintenance attention and is
protected against the harmful effects of ambient and climatic conditions not included in the Clause “Operating
conditions”. Moreover, care should be taken to ensure that excessive heating-up of the surface of the explosion-proof
closure of the motor and control box is prevented. It is necessary to make sure that rated values are not exceeded and
excessive actuator vibrations are prevented.
Lubrication
The actuators are lubricated with plastic consistent lubricants or gearbox oil PP 80
(Table 1 or 2).
Summary of Contents for MODACT MO EE 52 120
Page 2: ......
Page 25: ...25 Terminal board of DMS2 Analog Terminal board of DMS2 Profbus...
Page 49: ...NOTES...
Page 50: ...NOTES...