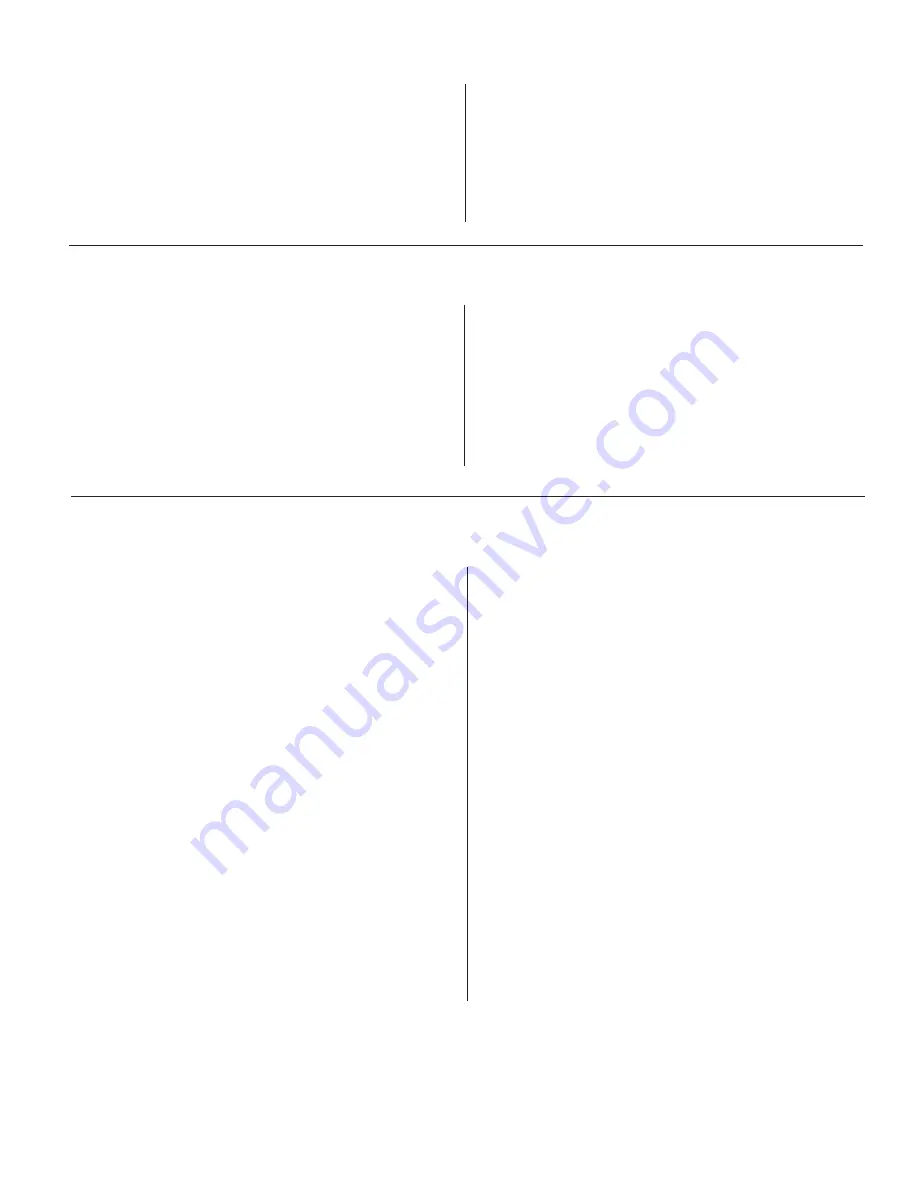
15
© Copyright 2022. All rights reserved.
RECOMMENDED METHODS FOR COLLECTING EFFLUENT SAMPLES*
ALARM PANEL & BLOWER INSPECTION AND MAINTENANCE
1. Listen for any loud rattling sounds. The blower should hum
softly. If a rattle is heard, ensure that all four legs securely
contact the ground or base medium.
2.
Inspect the filter once the power has been disconnected
by
removing the filter retention screw. Then, remove the cover
by snapping the filter cover off the top of the blower. Clean
the filter by knocking the dust out or by rinsing with water to
remove accumulated particles. Be sure the filter is dry before
reinstalling.
Proper effluent sample collection technique is essential for
obtaining an accurate assessment of treatment efficiency. To
accurately interpret treatment efficiency, influent as well as effluent
samples should be collected. In the event of reduced efficiency,
influent composition can be useful in determining system owner
practices. Depending upon configuration, effluent samples can be
collected at:
1. Disposal pump tank downstream of the Fusion
®
2. Fusion
®
discharge chamber
3. Distribution Box downstream of the Fusion
®
Samples should be obtained in clean, one liter bottles. Bottles
should be labeled appropriately to denote the sample’s original
location and kept on ice during transport. Samples should be
collected to approximate daily residential sewage flow. When
opening the Fusion
®
lid during sampling, try not to disturb the
unit. Also, do not collect the effluent sample from the wall of the
tank.
For further information, reference procedure identification number
SOP-F-103, Zoeller Pump Company, 1-800-928-7867.
* Consult local rules and regulations to determine jurisdictional
effluent sampling requirements.
Inspect the alarm panel for signs of water or odors inside. Toggle
the test switch on the side of the box to check that both the alarm
horn and the alarm beacon light are operational.
Inspect the blower and switching valve for proper operation. If the
blower is not functioning, refer to the troubleshooting section near
the end of this guide.
TROUBLESHOOTING
1. Odor
Offensive odors are often the result of insufficient or
inappropriate bacterial growth. Causes may include a young
or unestablished system, insufficient air introduction, or the
addition of detrimental chemicals or poisons into the system.
Ensure the blower and air delivery systems are functioning.
Check with the homeowner regarding chemical use and
disinfection habits. Check all risers and lids to ensure an
airtight seal.
2. Foam Formation
Foam formation is observed in the following situations:
a) In the early stage of operation when the
aerobic bacteria colony is establishing itself,
b) when an excess amount of air is supplied for aeration,
c) when the difference between ambient
temperature and water temperature is great, and
d) when an excessive amount of detergent is
introduced.
In most cases, foam will disappear with proper operation.
When excessive amounts of detergent have been introduced
to the system, remind the homeowner to use appropriate
amounts of detergent.
3. Cloudy Treated Water
• Check the amount of scum and sludge: If too much scum or
sludge is observed, transfer them to the first chamber and adjust
recirculation flow rate, frequency and duration. (See backwash
flow adjustment, pg. 10)
• Check the aeration situation:
If uneven bubble generation is observed, adjust valve (1). If
aeration is weak, flush the aeration pipe with air or water.
• Check the recirculation flow rate:
If the recirculation flow rate has increased
after the last inspection the aeration pipe may
be clogged. Flush the aeration pipe with air or
water. If the recirculation flow rate has decreased after the
last inspection, the airlift pump or recirculation pipe may be
clogged. Clean them with a brush and running water.
4. Blower
Blower Motor Does Not Run, with Power Connected:
• Check the electric supply to the panel, ensuring 120 volt
to blower power.
• Check that all breakers and fuses in the panels are on or
intact.
Little or No Aeration:
• Check the blower motor is running.
• Check the air line piping connectons at the blower and
switching valve.
• Check the air filter and clean or replace if necessary.
• Check the diaphragms and replace if necessary.
• Check the air piping for leaks, clogs, or dislocations and
fix
accordingly.
• Verify check valves (if installed) in supply lines are
installed correctly.