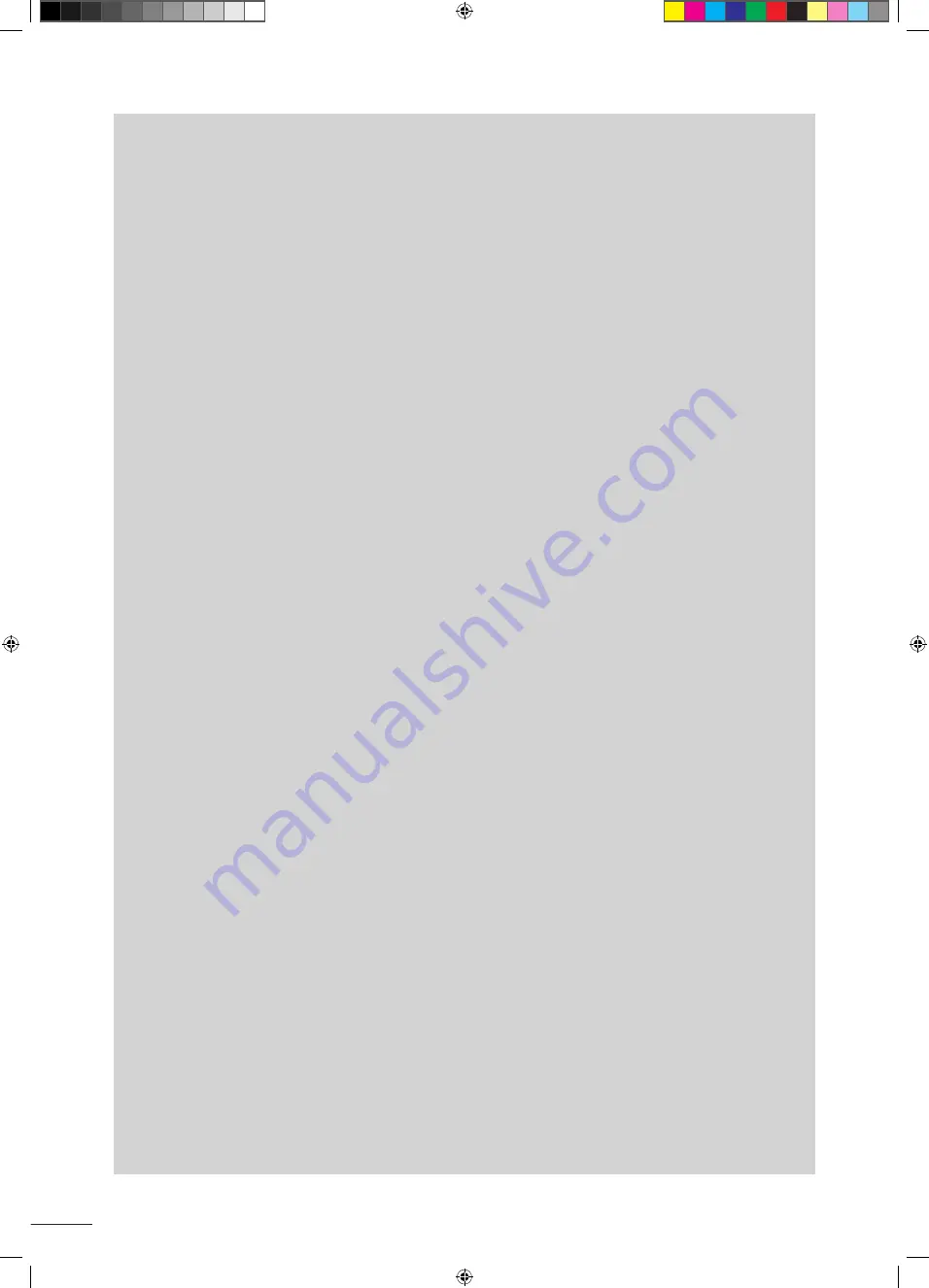
3
•
The appliance shall be stored in a room without continuously operating ignition
sources (for example: open flames, an operating gas appliance or an operating
electric heater).
• Do not pierce or burn.
• Be aware that refrigerants may not contain an odour.
INSTALLATION AND MAINTENANCE
•
The appliance may not be installed close to combustible materials, or an air duct
inlet of an adjacent building.
•
With some appliances, it is essential to fit protection grids if the unit is installed in
an area with uncontrolled access.
•
During installation, troubleshooting and maintenance, pipes may not be used as
steps: the pipe could break under the weight, spilling coolant and possibly causing
serious burns.
•
When servicing the appliance, the composition and state of the heat transfer fluid
must be checked, as well as the absence of any traces of coolant.
•
During the appliance's annual sealing test in accordance with applicable legislation,
the high and low pressure switches must be checked to ensure that they are
securely fastened to the cooling circuit and that they cut off the electrical circuit
when tripped.
• During maintenance work, ensure there are no traces of corrosion or oil around
the cooling components.
• Before beginning work on the cooling circuit, stop the appliance and wait for a few
minutes before fitting the temperature and pressure sensors. Some elements such
as the compressor and piping may reach temperatures in excess of 100°C and high
pressures with the consequent risk of severe burns.
TROUBLESHOOTING
•
All soldering work must be carried out by a someone qualified to do so.
• Replacement pipes must always be made of copper in compliance with standard
NF EN 12735-1.
•
Leak detection, pressure test:
- never use oxygen or dry air (risk of fire or explosion)
- use dry nitrogen or the mixture of nitrogen and coolant indicated on the
information plate,
- the test pressure for both the high and low pressure circuits must not exceed 42
bar (for R410A), 20 bar and 15 bar (for R407C) if the appliance is equipped with
the optional pressure gauge.
•
The high pressure circuit pipes are made of copper and have a diameter equal to or
greater than 1’’5/8. A certificate as indicated in §2.1 in compliance with standard NF
EN 10204 will be requested from the supplier and filed with the facility's technical
documentation.
•
Technical data relative to the safety requirements of the various applicable directives
are indicated on the information plate. All this information must be recorded in
the appliance's installation manual, which must be kept in the its technical file:
model, code, serial number, maximum and minimum OT, OP, year of manufacture,
CE marking, manufacturer’s address, coolant and weight, electrical parameters,
thermo-dynamic and acoustic performance.
LABELLING
•
Equipment shall be labelled stating that it has been decommissioned and emptied
of refrigerant.
• The label shall be dated and signed.
•
For appliances containing flammable refrigerants, ensure that there are labels on
the equipment stating the equipment contains flammable refrigerant.
RECOVERING
• When removing refrigerant from a system. either for servicing or decommissioning,
Summary of Contents for iAquaLink Z400iQ
Page 2: ......
Page 27: ...2 Z400iQ MD7...
Page 28: ...3 Z400iQ MD8...
Page 29: ...4 Z400iQ MD9...
Page 30: ...5 Z400iQ TD7 TD8 TD9...