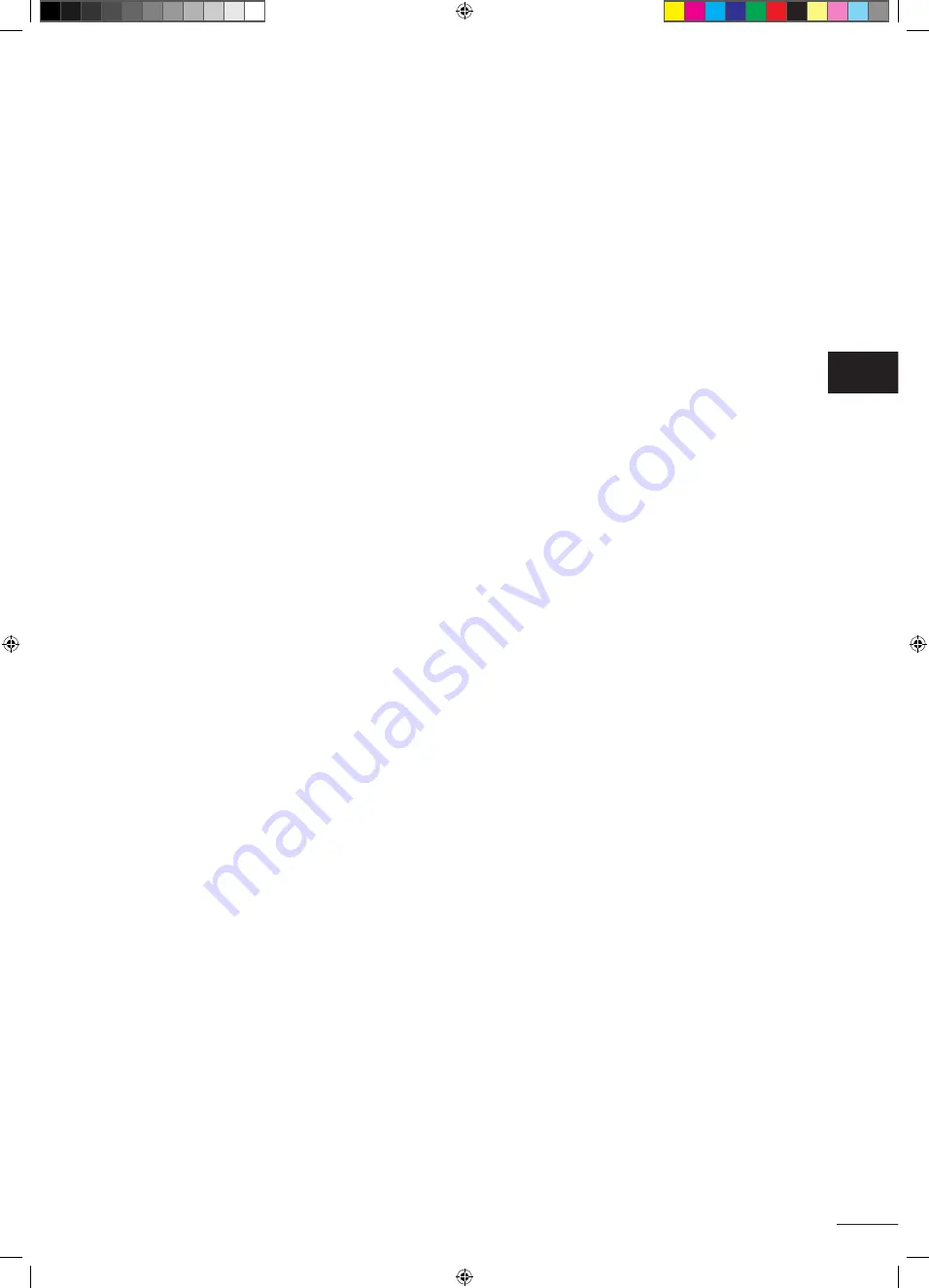
16
Area ventilation
•
Prior to penetrating the unit in any way to perform any required service, ensure that the area is open and adequately
ventilated. Proper ventilation, to allow for safe dispersion of any refrigerant which may be inadvertently released to
the atmosphere, should be maintained while service is being performed on the unit.
Refrigeration equipment check
•
The manufacturer’s service and maintenance guidelines must be followed at all times. When replacing any electrical
components, be sure to use only components which are of the same type and rating and which are recommended/
approved by the manufacturer. If in doubt, consult the manufacturer’s technical department for assistance.
•
The following checks shall be applied to installations using flammable refrigerants:
- if an indirect refrigerating circuit is being used, the secondary circuit shall be checked for the presence of refrigerant;
- Marking to the equipment continues to be visible and legible. Markings and signs that are illegible shall be corrected;
- refrigerating pipe or components are installed in a position where they are unlikely to be exposed to any substance
which may corrode refrigerant containing components, unless the components are constructed of materials which
are inherently resistant to being corroded or are suitably protected against being so corroded.
Electrical component check
•
Repair and maintenance to electrical components shall include initial safety checks and component inspection
procedures. If a fault exists that could compromise safety, then no electrical supply shall be connected to the circuit
until it is satisfactorily dealt with. If the fault cannot be corrected immediately but it is necessary to continue operation,
an adequate temporary solution shall be used. This shall be reported to the owner of the equipment so all parties
are advised.
•
Initial safety checks shall include:
- that capacitors are discharged: this shall be done in a safe manner to avoid possibility of sparking;
- that no live electrical components and wiring are exposed while charging, recovering or purging the system;
- that there is continuity of earth bonding.
Repair of insulated components
•
During repairs to sealed components, all electrical supplies shall be disconnected from the equipment being worked
upon prior to any removal of sealed covers, etc. If it is absolutely necessary to have an electrical supply to equipment
during servicing, then a permanently operating form of leak detection shall be located at the most critical point to
warn of a potentially hazardous situation.
•
Particular attention shall be paid to the following to ensure that by working on electrical components, the casing
is not altered in such a way that the level of protection is affected. This shall include damage to cables, excessive
number of connections, terminals not made to original specification, damage to seals, incorrect fitting of glands, etc.
•
Ensure that the apparatus is mounted securely.
•
Ensure that seals or sealing materials have not degraded to the point that they no longer serve the purpose of
preventing the ingress of flammable atmospheres. Replacement parts shall be in accordance with the manufacturer’s
specifications.
Repair of intrinsically safe components
•
Do not apply any permanent inductive or capacitance loads to the circuit without ensuring that this will not exceed
the permissible voltage and current permitted for the equipment in use.
•
Intrinsically safe components are the only types that can be worked on while live in the presence of a flammable
atmosphere. The test apparatus shall be at the correct rating.
•
Replace components only with parts specified by the manufacturer. Other parts may result in the ignition of refrigerant
in the atmosphere from a leak.
Wiring
•
Check that cabling will not be subject to wear, corrosion, excessive pressure, vibration, sharp edges or any other
adverse environmental effects. The check shall also take into account the effects of aging or continual vibration from
sources such as compressors or fans.
Detection of flammable refrigerant
•
Under no circumstances shall potential sources of ignition be used in the searching for or detection of refrigerant
leaks. A halide torch (or any other detector using a naked flame) shall not be used.
•
The following leak detection methods are deemed acceptable for all refrigerant systems.
•
Electronic leak detectors may be used to detect refrigerant leaks but, in the ease of flammable refrigerants, the
sensitivity may not be adequate, or may need re-calibration. (Detection equipment shall be calibrated in a refrigerant-
tree area.) Ensure that the detector is not a potential source of ignition and is suitable for the refrigerant used. Leak
detection equipment shall be set at a percentage of the LFL of the refrigerant and shall be calibrated to the refrigerant
employed, and the appropriate percentage of gas (25% maximum} is confirmed.
•
Leak detection fluids are also suitable for use with most refrigerants but the use of detergents containing chlorine
shall be avoided as the chlorine may react with the refrigerant and corrode the copper pipe-work.
•
If a leak is suspected, all naked names shall be removed/extinguished.
•
If a leakage of refrigerant is found which requires brazing. all of the refrigerant shall be recovered from the system. or
isolated (by means of shut off valves} in a part of the system remote from the leak.
Removal and discharge
•
When breaking into the refrigerant circuit to make repairs - or for any other purpose - conventional procedures shall
be used. However, for flammable refrigerants it is important that best practice is followed since flammability Is a
consideration. The following procedure shall be adhered to:
- remove refrigerant;
EN
Summary of Contents for iAquaLink Z400iQ
Page 2: ......
Page 27: ...2 Z400iQ MD7...
Page 28: ...3 Z400iQ MD8...
Page 29: ...4 Z400iQ MD9...
Page 30: ...5 Z400iQ TD7 TD8 TD9...