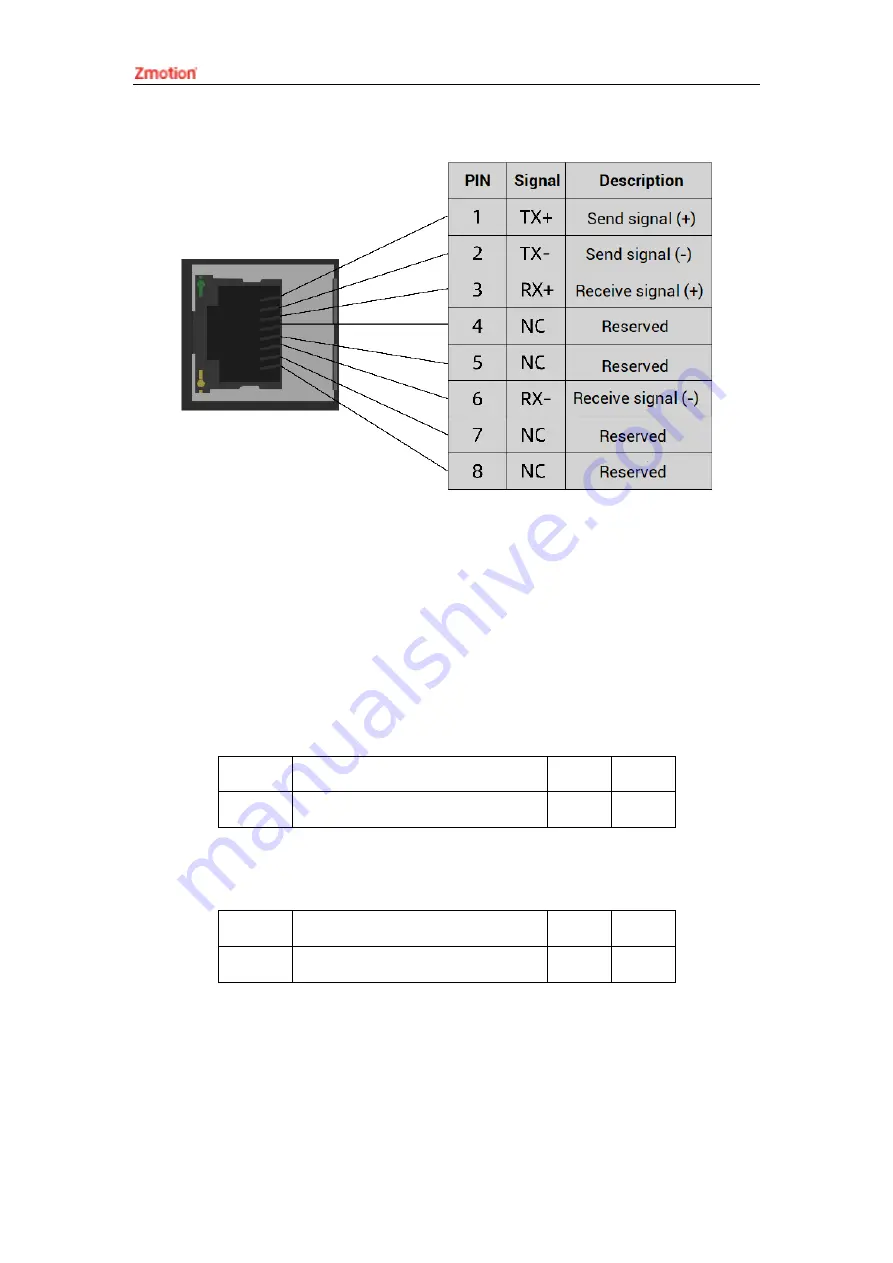
ZMC432N Motion Controller User Manual V1.5
to Panasonic RTEX servo driver.
3.9.1.
RTEX Bus Interface Rule
→
Specification
Controller default firmware is configured 1ms period, which can be checked through
SERVO_PERIOD. Below shows corresponding drive parameters to configure:
7.20
RTEX Communication Period
6
1ms
7.21
RTEX Instruction Update Period
1
1ms
If controller firmware is customized, please refer to drive period configuration to
adjust. For example, the firmware is with 0.5ms, corresponding drive parameters:
7.20
RTEX Communication Period
3
0.5ms
7.21
RTEX Instruction Update Period
1
0.5ms
→
Wiring Reference
Two cables are required for the RTEX bus, TX is the sending side and RX is the
receiving side. TX needs to be connected to RX, RX needs to be connected to TX, all
Summary of Contents for ZMC432N
Page 1: ......