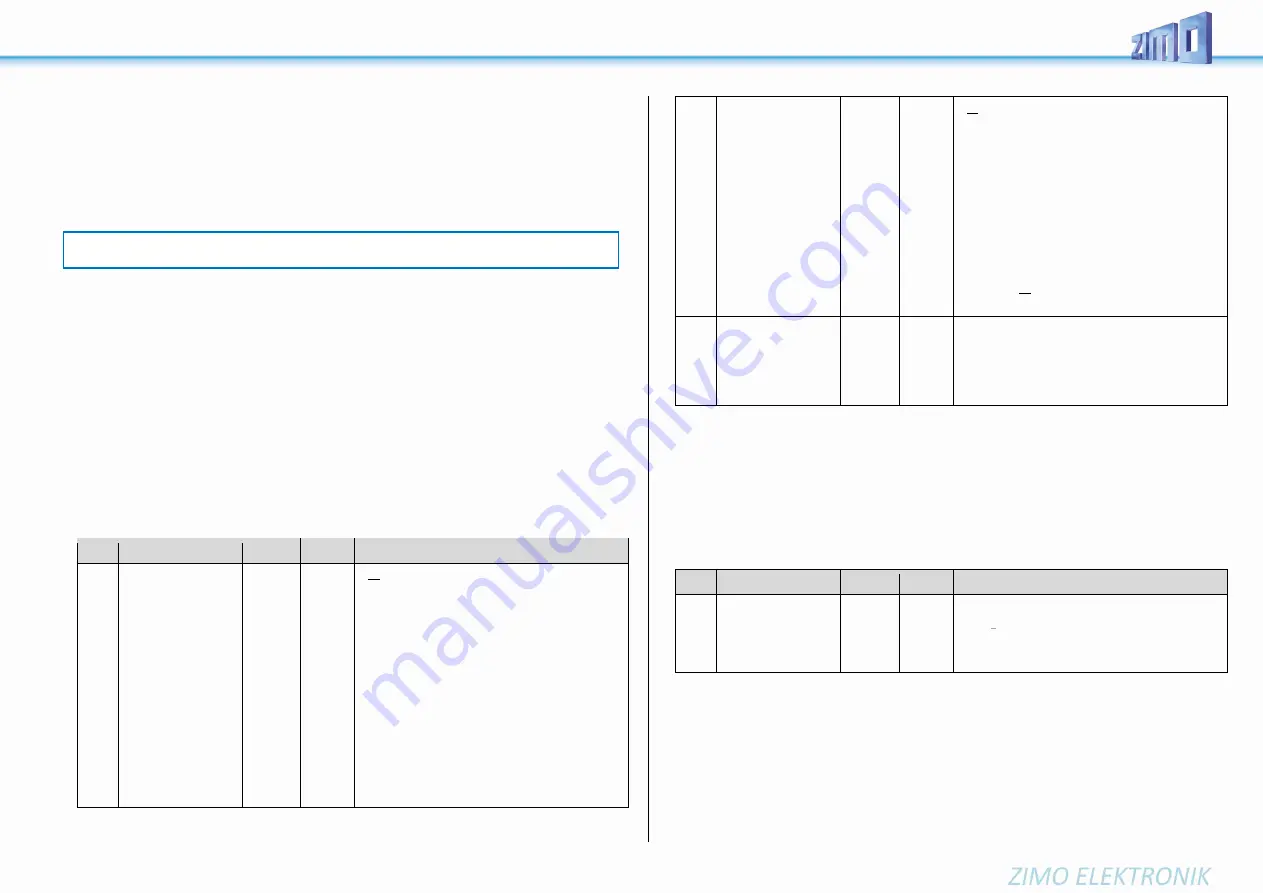
MS - SOUND decoders MS440 to MS990 and MN - NON-SOUND decoders MN170 to MN340 Page 27
Tweaking the motor regulation by controlling algorithm
The motor’s performance, especially at crawling speeds (as judder-free as possible), can be fine-tuned
with the following parameters:
CV #9
– Motor control frequency and EMF sampling rate
The motor’s PWM is high frequency (typ. 20 kHz, also above the frequencies audible for the human ear).
Compared to the low frequency control (used until the 1990s, usually around 100 Hz)
quiet
and
engine-
friendly
.
When using high frequency, the power supply to the motor is interrupted periodically with low frequen-
cies (50
– 200 times/sec.), in order to determine the current speed by measuring back-EMF (voltage
generated by the motor). The more frequent these interruptions happen (sampling rate), the better; but
that also causes increased noise. By default, the sampling frequency varies automatically between 200
Hz at low speed and 50 Hz at maximum speed.
CV #9 allows the adjustment of the sampling rate (tens digits) as well as the sampling time (ones digits).
The default value of 55 represents a medium setting.
CV #56 or CVs #147, #148, #149
– The PID regulation
The motor regulation can be tailored to motor type, vehicle weight and so on, by using different
Pr
opor-
tional-
I
ntegral-
D
ifferential values. Changing the differential value can usually be omitted.
CV #56 allows the proportional value (tens digit) as well as the integral value (ones digit) to be set indi-
vidually. The default value of 55 represents a medium setting. In MS-decoders, CV #56 exists solely for
compatibility reasons; the fine adjustment is made possible by the new CVs #147, #148, #149:
CVs #147, #148, #149 automatically adapt to the modification of CV #56, NOT the other way round.
CV
Denomination
Range
Default Description
#9
Motor control-
period
or frequency
and
EMF-sampling
Rate
(sampling rate,
Sampling time)
Total PWM period
01 - 99
High fre-
quency
with modi-
fied sam-
pling rate
100
– 199
From SW
V. 4.215
55
High fre-
quency
medium
Sampling
rate
= 55: Default motor control with high frequency (20 kHz),
medium EMF sampling rate that adjusts between 200Hz
(low speed) and 50Hz and medium EMF sampling time.
= 0: equal to 0 (is converted automatically)
<> 55 and <> 0: Modification of the default setting,
each divided in: tens digit for sampling rate
and ones digit (sampling time).
Hundreds digit 1: modified settings for coreless motors
(Faulhaber, Maxxon, etc.)
Tens digit 1 - 4: Sampling rate lower than
default (less noise)
Tens digit 6 - 9: Sampling rate higher than default
(to combat juddering!)
Ones digit 1 - 4: EMF-sampling time shorter than
by default (works well for Faulhaber, Maxxon, ...
less noise, more power)
Ones digit 5 - 9: EMF-sampling time longer than default
(may be needed for round motors or similar)
#56
P and I value
for
PID motor regulation
(= EMK
EMF-load balance con-
trol)
The value of this CV will
be automatically trans-
ferred to CVs #147 -
#149
01 - 99
55
medium
PID
Setting
= 55: Default motor control using medium
values in PID parameters P and I (Diff = 0).
= 0: equal to 0 (is converted automatically)
<> 55 and <> 0: modified settings
Tens digit 1 - 4: Proportional value of the PID-motor reg-
ulation, lower than default
Tens digit 6 - 9: Proportional value of the PID-motor reg-
ulation, higher than default
Ones digit 1 - 4: Integral value of the PID regulation
lower than default
Ones digit 6 - 9: Integral value of the PID regulation
higher than default
Typical test values against jerky driving:
CV #56 = 55 (default)
→
33, 77, 73, 71, ...
ATTENTION
: The values 10, 20, 30, 40, 50, 60, 70, 80
and 90 are NOT allowed!
#147
#148
#149
complete setting of
PID parameters
NOTE
: are adjusted au-
tomatically with CV #56!
0 - 255
0 - 255
0 - 255
adapts to
CV #56,
if not pro-
grammed
I
ntegral value of the PID-motor regulation,
recommended for „modern“ powertrain: CV #147 = 65
D
ifferential value of the PID-motor regulation,
recommended for „modern“ powertrain: CV #148 = 45
P
roportional value of the PID-motor regulation,
recommended for „modern“ powertrain: CV #149 = 65
Tips on how to find the optimal CV #56 settings:
can also be used for #147, #148, #149:
Start with an initial setting of CV #56 =
11
; set the engine at low speed while holding it back with one
hand. The motor regulation should compensate for the higher load within half a second. If it takes longer
than that, increase the ones digit gradually: CV #56 = 1
2
, 1
3
, 1
4
, ...
Continue running at a low speed, increase the tens digit in CV #56. For example: (if the test above
resulted in CV #56 = 1
3
) start increasing the tens digit CV #56 =
2
3,
3
3,
4
3… as soon as driving conduct
is detected, revert to the previous digit
→
this would be the final setting.
CV
Denomination
Range
Default Description
#112
Special ZIMO
Configuration data
SW version 5.00 and
higher
0 - 255
0
Bit 2 = 0: ZIMO loco number recognition OFF
= 1: ZIMO loco number recognition ON
CV #58 - Load compensation
At this moment it is not clear, if this CV will also be necessary in MS-decoders.
The goal of load compensation is to keep the speed at a constant level in all circumstances (only limited by available
power). Though, a certain reduction in compensation is quite often preferred.
100
% load compensation is useful within the low-speed range to successfully prevent engine stalls or run-away under
light load. Load compensation should be reduced as speed increases, so that at full speed the motor receives full
power. Also, a slight grade-dependent speed change is often considered more prototypical.
Locomotives operated in consists should never run at 100
% load compensation in any part of the speed range, be-
cause it causes the locomotives to fight each other and could even lead to derailments.
NOTE
: Frequencies higher than 20 kHz do not have an advantage for motor manufacturers and lead to a (slightly)
higher heat loss within the decoder. Therefore, the option to 40 kHz on the new decoders is not planned anymore.
Summary of Contents for MS450
Page 5: ...MS SOUND decoders MS440 to MS990 and MN NON SOUND decoders MN170 to MN340 Page 5...
Page 61: ...MS SOUND decoders MS440 to MS990 and MN NON SOUND decoders MN170 to MN340 Page 61...
Page 85: ...MS SOUND decoders MS440 to MS990 and MN NON SOUND decoders MN170 to MN340 Page 85...
Page 87: ...MS SOUND decoders MS440 to MS990 and MN NON SOUND decoders MN170 to MN340 Page 87...
Page 88: ...Page88 MS SOUND decoders MS450 to MS990 ZIMO Elektronik GmbH Sch nbrunner Str 188 A 1120 Wien...