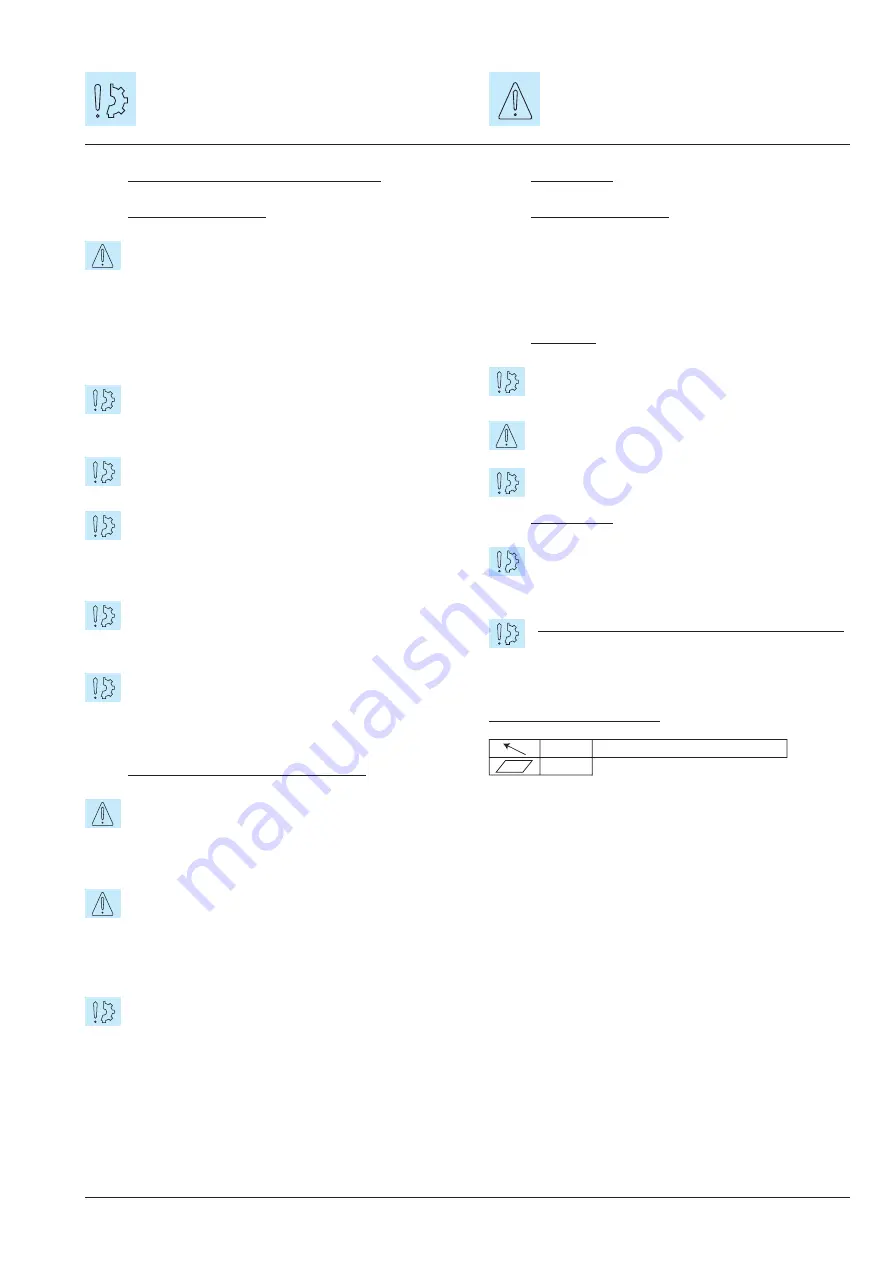
WARNER ELECTRIC EUROPE - Rue Champfleur, B.P. 20095, F - 49182 St Barthélemy d’Anjou Cedex
SM346gb - rev 09/03
3/5
2
Precautions and restrictions on use
2.1
Restrictions on use
For the brake to comply with directive 95/16/EC,
the integrator must observe the general conditions
for installations and use as defined in the EC type certifi-
cate ref. ABV 591 of 08/08/01 drawn up by the TUV
Munich, including the mandatory use of a speed limiting
device, in compliance with EN 81-1 paragraph 9.9 subpoint
9.10.10.
This brake is designed to work in dry conditions.
Friction faces must be kept completely clean of
any oil, grease or abrasive dust.
If maximum rotation speeds are exceeded, the guar-
antee is no longer valid.
This brake may only be used in a "horizontal axis".
The customer must be careful not to alter the fac-
tory-set airgap. This is in order to ensure the brakes may
be properly released.
This brake is designed for a maximum ambient
temperatur of 40°C. The maximum surface
temperature on the brake should not exceed 100°C.
This brake is designed for static applications. Any
dynamic braking is restricted to emergency brak-
ing and test braking. This brake can in no way replace the
safety braking system used during lift descent.
2.2
Precautions and safety measures
During maintenance, make sure that the mecha-
nism to be braked by the brake is at a standstill, i.e.
has no torque to transmit, and that there is no danger of it
accidentally starting up.
Any modification made to the brake without the
express authorisation of a representative of Warner
Electric will result in the warranty being invalidated and
Warner Electric will no longer be liable in any way with
regard to conformity.
When switching on DC-side the coil must be pro-
tected against voltage peaks.
Symbol designating an action that
might damage the brake
Symbol designating an action that
might be dangerous to human safety
3
Installation
3.1
Transport / storage
This brake is delivered in standard packaging that will keep
it intact for a period of 6 months during ground, air or sea
transport towards neighbouring continents (without cross-
ing the tropics).
3.2
Handling
Avoid any impact to the brake so that its perform-
ance is not impaired.
When handling, use the threads for eye hooks
intended for this purpose.
Never lift the brake by its cables.
3.3
Installation
This brake is designed to operate in dry conditions.
The friction faces must be completely clear of any
oil, grease or abrasive dust.
Specifications for the customer’s friction face:
Material: Steel (150 to 250 HV) or Cast iron
Roughness
≤
Ra 3,2
Protection: Phosphatizing (dry) or nitriding
Geometrical tolerances:
The brake is delivered pre-assembled with pre-set
microswitches and airgaps. Fixing screws, the hub and
the O-rings are supplied separately, The O-rings are not pre-
assembled on the hub.
•
Put the hub into position on the customer’s shaft.
Maximum fretting temperature: 150°C (keying JS9)
•
When the hub has cooled down, assemble the 2 shock
absorbing O-rings lightly smeared with Vaseline
(see Fig. 1)
•
Engage the front disc on the hub as in Fig. 1, the heel
on the brake side
•
Engage magnet C
0,1
Customer's shaft axis
0,1