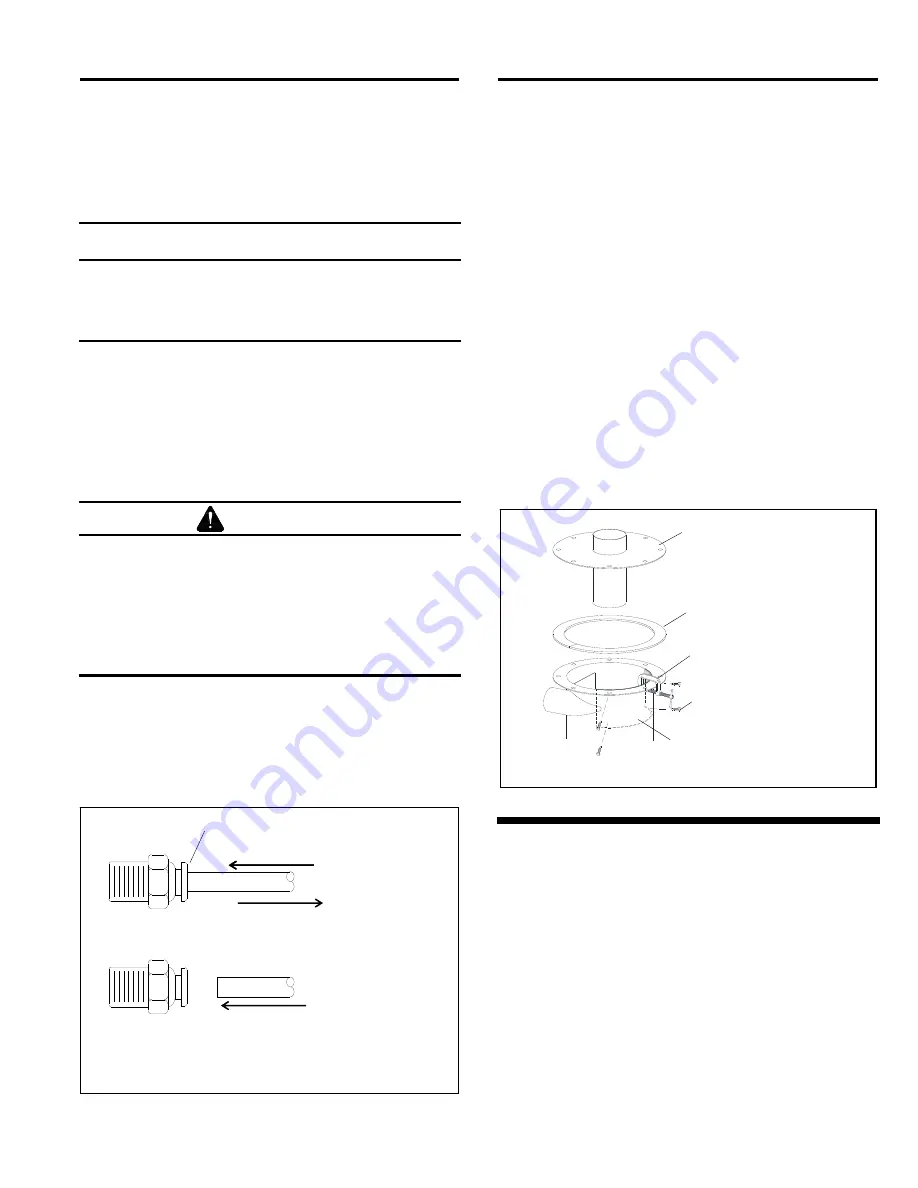
BNP-160 TUMBLE BASKET BLAST CABINET
Page 13
© 2018 CLEMCO INDUSTRIES CORP.
www.clemcoindustries.com
Manual No. 25993 Rev B 05/18
6.5.3
Remove the element and empty dust from the
housing.
6.5.4
Shake the cap and tubing to see if dust is in the
tubing. If dust is present, remove the tubing from the cap
and shake the tubing until all dust is removed.
NOTICE
If the inline filter is removed from the tubing,
reinstall it with the directional arrow pointing
toward the Hi (+) pressure port on the differential
pressure gauge, as shown in Figure 16.
6.5.5
Before attaching the inlet cap, be sure the filter
is correctly positioned. Align the tabs on the cap with the
recesses on the housing. Make sure the end of the cap
enters the ID of the element as it is pushed into position.
Turn the cap toward L to lock it in place.
6.6
Tube-Lock Fittings – Figure 17
WARNING
Failure to observe the following procedure
before performing any maintenance can cause
injury from the sudden release of trapped
compressed air.
Lock out and tag out the compressed air
supply.
Bleed all compressed air-supply lines.
6.6.1
To remove the tubing, push the retaining collar
toward the fitting, releasing the tubing so it can be easily
removed by pulling it out. Do not force it; only a slight
pull on the tubing is required if the collar is pushed in
correctly.
Figure
17
6.6.2
Reconnect the tubing by inserting it into the
retaining collar until it seats. Tug on the tubing to make
sure it is secured.
6.7
Replace Reclaimer Wear Plate – Figure 18
6.7.1
Remove the fasteners holding the reclaimer top
to the body and remove the top.
6.7.2
The gasket should adhere to the reclaimer when
the top is removed. Inspect the gasket and replace it if
damaged.
6.7.3
Remove the screws that hold the wear plate to
the body and remove the old wear plate.
6.7.4
Press or clamp the new wear plate into position
and use self-drilling screws inserting through the existing
screw holes to secure the wear plate.
6.7.5
Replace the top and secure with fasteners.
Figure
18
Retaining Collar
Push collar in to release tubing.
Pull tubing straight out.
To reconnect the tubing, push it into the
fitting until it bottoms out. Pull on the
tubing to make sure it is securely fastened.
Wear Plate
Gasket
Self-Drilling Screws
Reclaimer Top
Clamp
Shown for reference.