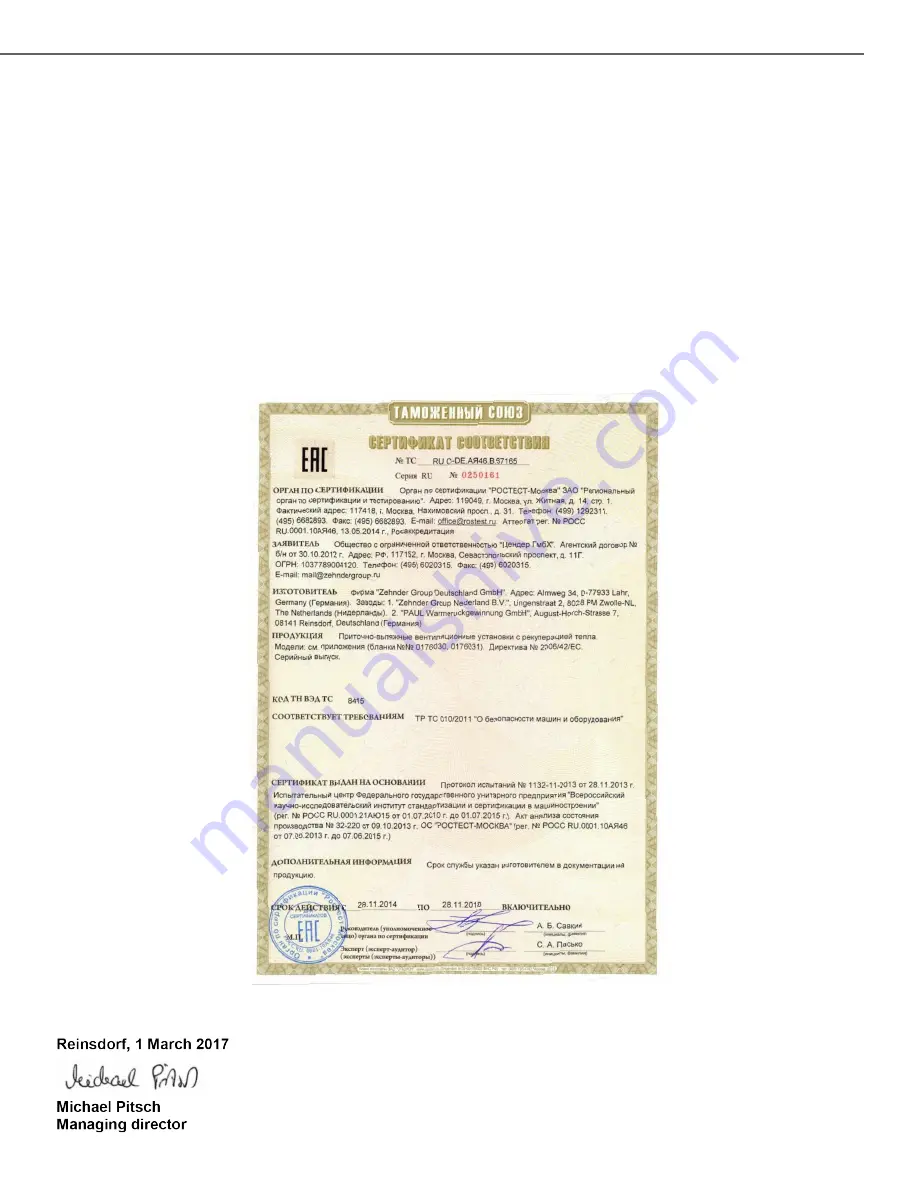
49
5.7.2
EAC certificate of the Eurasian Economic Union
Manufacturer:
PAUL Wärmerückgewinnung GmbH
August-Horsch-Straße 7
08141 Reinsdorf
Germany
EAC CERTIFICATE
We hereby declare that the product/series named in the following, by virtue of its conception and design, as well as in
terms of the configuration placed on the market by us, meets the relevant and essential health and safety requirements
in the EAC certificate of the Eurasian Economic Union listed below.
Product name: Decentralized waste heat recovery unit ComfoAir 70 - Series
Signed for an in the name of: