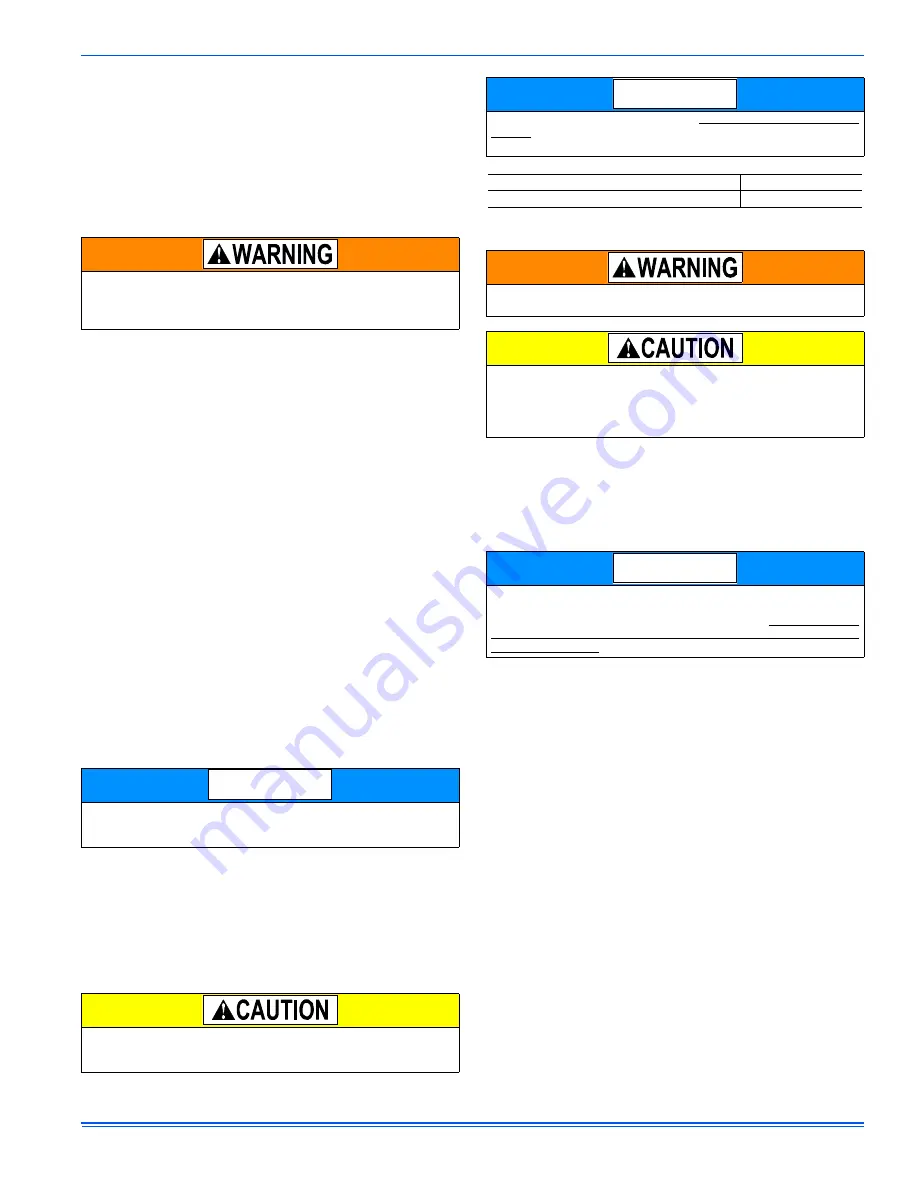
835966-UIM-E-0814
Johnson Controls Unitary Products
3
GROUND INSTALLATION
The unit may be installed at ground level on a solid base that will not
shift or settle, causing strain on the refrigerant lines and possible leaks.
The unit must be installed in as level a position as possible while main-
taining the clearances shown in Figure 1.
Normal operating sound levels may be objectionable if the unit is placed
directly under windows of certain rooms (bedrooms, study, etc.).
Condensate will drain from beneath the coil of the outdoor unit during
the defrost cycle. Normally this condensate may be allowed to drain
directly on the ground.
1. Elevate the unit sufficiently to prevent any blockage of the air
entrances by snow in areas where there will be snow accumulation.
2. Check the local weather bureau for the expected snow accumula-
tion in your area.
3. Isolate the unit from rain gutters to avoid any possible wash out of
the foundation.
ROOF INSTALLATION
When installing units on a roof, the structure must be capable of sup-
porting the total weight of the unit, including a pad, lintels, rails, etc.,
which should be used to minimize the transmission of sound or vibra-
tion into the conditioned space.
WALL MOUNT INSTALLATION
Care must be taken to mount the outdoor unit on a solid base that is
sloped to shed water, secure from settlement, and is isolated from the
structural foundation or walls to prevent sound and vibration transmis-
sion into the living space. In addition heat pump units must be elevated
above anticipated snow accumulation levels to allow for proper defrost
drainage and airflow.
On occasion, site conditions may require direct wall mounted brackets
to be used to locate and support the outdoor unit. In these applications,
care must be taken to address unit base pan support, structural integ-
rity, safe access and serviceability, as well as the possible sound and
vibration transmission into the structure. These applications are best
served by a properly engineered solution.
UNIT PLACEMENT
1. Provide a base in the pre-determined location.
2. Remove the shipping carton and inspect for possible damage.
3. Compressor tie-down bolts should remain tightened.
4. Position the unit on the base provided.
LIQUID LINE FILTER-DRIER
The heat pumps have a solid core bi-flow filter/dryer located on the liq-
uid line.
PIPING CONNECTIONS
The outdoor unit must be connected to the indoor coil using field sup-
plied refrigerant grade copper tubing that is internally clean and dry.
Units should be installed only with the tubing sizes for approved system
combinations as specified in Tabular Data Sheet. The charge given is
applicable for total tubing lengths up to 15 feet. See Application Data
Part Number 247077 for installing tubing of longer lengths and elevation
differences.
PRECAUTIONS DURING LINE INSTALLATION
1. Install the lines with as few bends as possible. Make sure there is no
damage done to the couplings nor kink made in the tubing. Use
clean hard drawn copper tubing where no appreciable amount of
bending around obstruction is necessary. If soft copper must be
used, make sure to avoid sharp bends which may cause a restric-
tion.
2. Ensure that the lines are installed so they do not obstruct service
access to the coil, air handling system, or filter.
3. Make sure to isolate the refrigerant lines to minimize noise transmis-
sion from the equipment to the structure.
4. Make sure to insulate the vapor line with a minimum of 1/2” foam
rubber insulation (Armaflex or equivalent). Make sure to insulate the
liquid lines which are exposed to direct sunlight and/or high temper-
atures.
5. Tape and suspend the refrigerant lines as shown. DO NOT allow
tube metal-to-metal contact. See Figure 2.
6. Use PVC piping as a conduit for all underground installations as
shown in Figure 3. Keep buried lines as short as possible to mini-
mize the build up of liquid refrigerant in the vapor line during long
periods of shutdown.
The outdoor unit should not be installed in an area where mud or ice
could cause personal injury. Remember that condensate will drip from
the unit coil during heat and defrost cycles and that this condensate
will freeze when the temperature of the outdoor air is below 32°F.
Heat pumps will defrost periodically resulting in water drainage. The
unit should not be located where water drainage may freeze and cre-
ate a hazardous condition - such as sidewalks and steps.
Failure to use the same as the original factory drier, or using a substi-
tute drier, or using a granular type drier may result in damage to the
equipment.
NOTICE
Replacements for the liquid line drier must be exactly the same as
marked on the original factory drier. See Source 1 for O.E.M. replace-
ment driers.
Filter-Drier Source 1 Part No.
Apply with Models
S1-404101
All Sizes
Never install a suction-line filter drier in the liquid line of an R-410A
system. Failure to follow this warning can cause a fire, injury or death.
This system uses R-410A refrigerant only, which operates at higher
pressures than R-22. No other refrigerant than R-410A may be used
in this system. Gauge sets, hoses, refrigerant containers, and recov-
ery system must be designed to handle R-410A. If you are unsure,
consult the equipment manufacturer.
Using a larger than specified line size could result in oil return prob-
lems. Using too small a line will result in loss of capacity and other
problems caused by insufficient refrigerant flow. Slope horizontal
vapor lines at least 1" every 20 feet toward the outdoor unit to facili-
tate proper oil return.
NOTICE
NOTICE