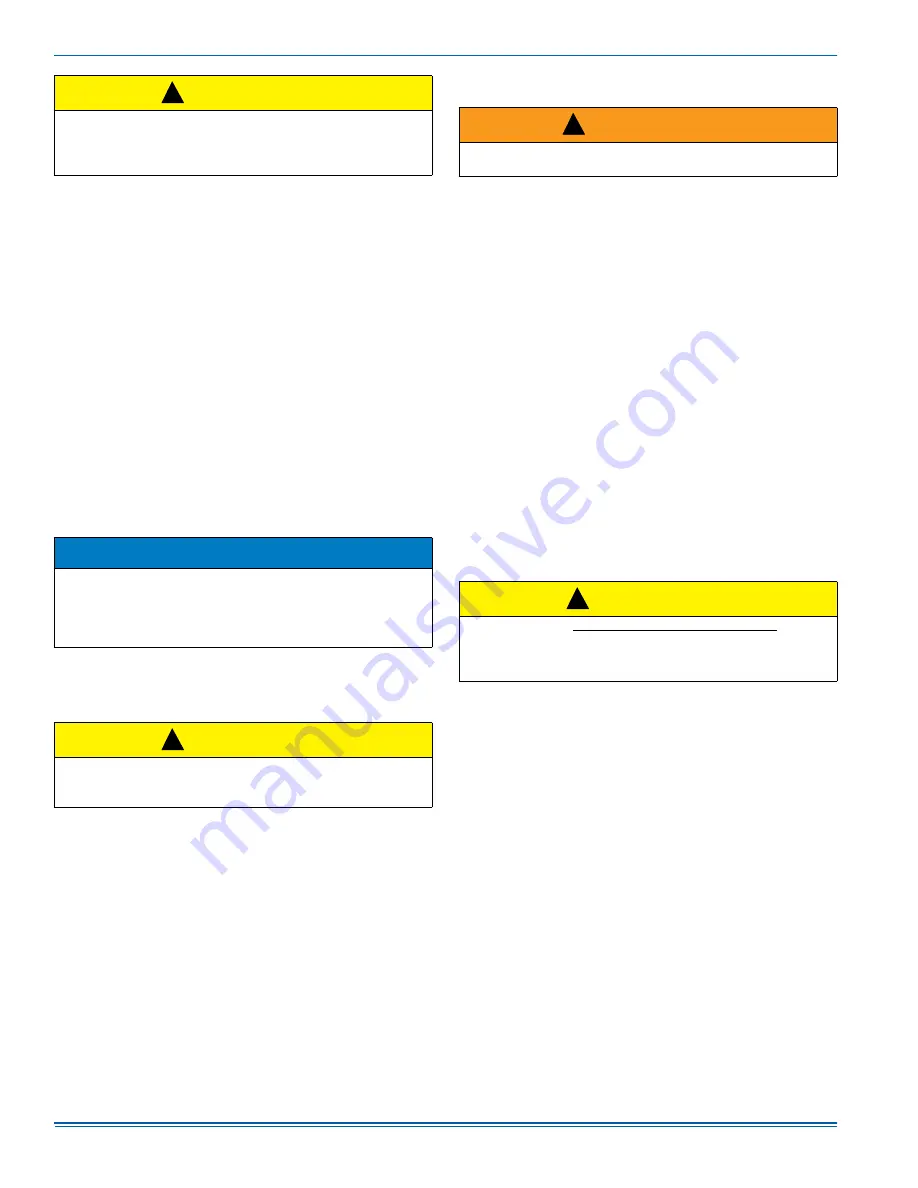
5284792-UIM-A-0317
6
Johnson Controls Unitary Products
4. Power must be applied to the indoor unit. If installing a coil/furnace
match or multi piece air handler system, the EEV harness must be
plugged into the communication port header on furnace or blower
control board prior to apply power to the indoor unit. Allow 1 minute
for the EEV to open to allow proper nitrogen flow through the coil
and line-set.
5. Protect the vapor valve with a wet rag and braze the vapor line con-
nection to the outdoor unit. The nitrogen flow should be exiting the
system from the vapor service port connection. After this connection
has cooled, remove the nitrogen source from the liquid fitting ser-
vice port.
6. Braze the liquid line to the evaporator liquid connection. Nitrogen
should be flowing through the evaporator coil.
7. Slide the grommet away from the vapor connection at the indoor coil
and wrap with a wet rag as shown in Figure 5. Braze the vapor line
to the evaporator vapor connection. After the connection has
cooled, slide the grommet back into original position. After this con-
nection has cooled, remove the nitrogen source from the liquid fit-
ting service port.
8. Replace the Schrader core in the liquid and vapor valves.
9. Leak test all refrigerant piping connections including the service port
flare caps to be sure they are leak tight. DO NOT OVERTIGHTEN
(between 40 and 60 inch - lbs. maximum).
10. Evacuate the vapor line, evaporator, and liquid line to 500 microns
or less.
11. Replace cap on service ports. Do not remove the flare caps from the
service ports except when necessary for servicing the system.
12. Release the refrigerant charge into the system. Open both the liquid
and vapor valves by removing the service valve cap and with an
Allen wrench back out counter-clockwise until valve stem just
touches the chamfered retaining wall. If the service valve is a ball
valve, use a Crescent wrench to turn valve stem one-quarter turn
counterclockwise to open. Do not overturn or the valve stem may
break or become damaged. See “PRECAUTIONS DURING BRAZ-
ING SERVICE VALVE”.
13. Replace service valve cap finger tight, then tighten an additional 1/2
turn (1/2 hex flat). Cap must be replaced to prevent leaks.
14. See
Section VI “System Charge” section for checking and recording
system charge.
SECTION IV: EVACUATION
Evacuate the system to 500 microns or less. If a leak is suspected, leak
test with dry nitrogen to locate the leak. Repair the leak and test again.
To verify that the system has no leaks, simply close the valve to the
vacuum pump suction to isolate the pump and hold the system under
vacuum. Watch the micron gauge for a few minutes. If the micron
gauge indicates a steady and continuous rise, it’s an indication of a
leak. If the gauge shows a rise, then levels off after a few minutes and
remains fairly constant, it’s an indication that the system is leak free but
still contains moisture and may require further evacuation if the reading
is above 500 microns.
SECTION V: ELECTRICAL CONNECTIONS
GENERAL INFORMATION & GROUNDING
The control box cover is held in place with 5 screws (one screw near
each lower corner, one each at the midpoint of each side and one at top
middle).
Check the electrical supply to be sure that it meets the values specified
on the unit nameplate and wiring label.
Power wiring, control (low voltage) wiring, disconnect switches and over
current protection must be supplied by the installer. Wire size should be
sized per NEC requirements.
The complete connection diagram and schematic wiring label is located
on the inside surface of the unit service access panel. An example of
typical field connections can be found in Figure 7.
FIELD CONNECTIONS POWER WIRING
1. Install the proper size weatherproof disconnect switch outdoors and
within sight of the unit, per local code.
2. Remove the screws at the top and sides of the corner cover. Slide
the control box cover down and remove from unit.
3. Run power wiring from the disconnect switch to the unit.
4. Route wires from disconnect through power wiring exit provided and
into the unit control box as shown in Figure 1 and view the openings
in Figure 6.
5. Make the power supply connections to the supplied terminal block.
CAUTION
Do not install any coil with a furnace which is to be operated during
the heating season without attaching the refrigerant lines to the coil.
The coil is under pressure which must be released to prevent exces-
sive pressure build-up and possible coil damage.
NOTICE
Line set and indoor coil can be pressurized to 250 psig with dry nitro-
gen and leak tested with a bubble type leak detector. Then release
the nitrogen charge.
Do not use the system refrigerant in the outdoor unit to purge or leak
test.
CAUTION
Do not connect manifold gauges unless trouble is suspected. Approx-
imately 3/4 ounce of refrigerant will be lost each time a standard man-
ifold gauge is connected.
!
!
WARNING
Never attempt to repair any brazed connections while the system is
under pressure. Personal injury could result.
CAUTION
All field wiring must USE COPPER CONDUCTORS ONLY and be in
accordance with Local, National, Fire, Safety & Electrical Codes. This
unit must be grounded with a separate ground wire in accordance
with the above codes.
!
!