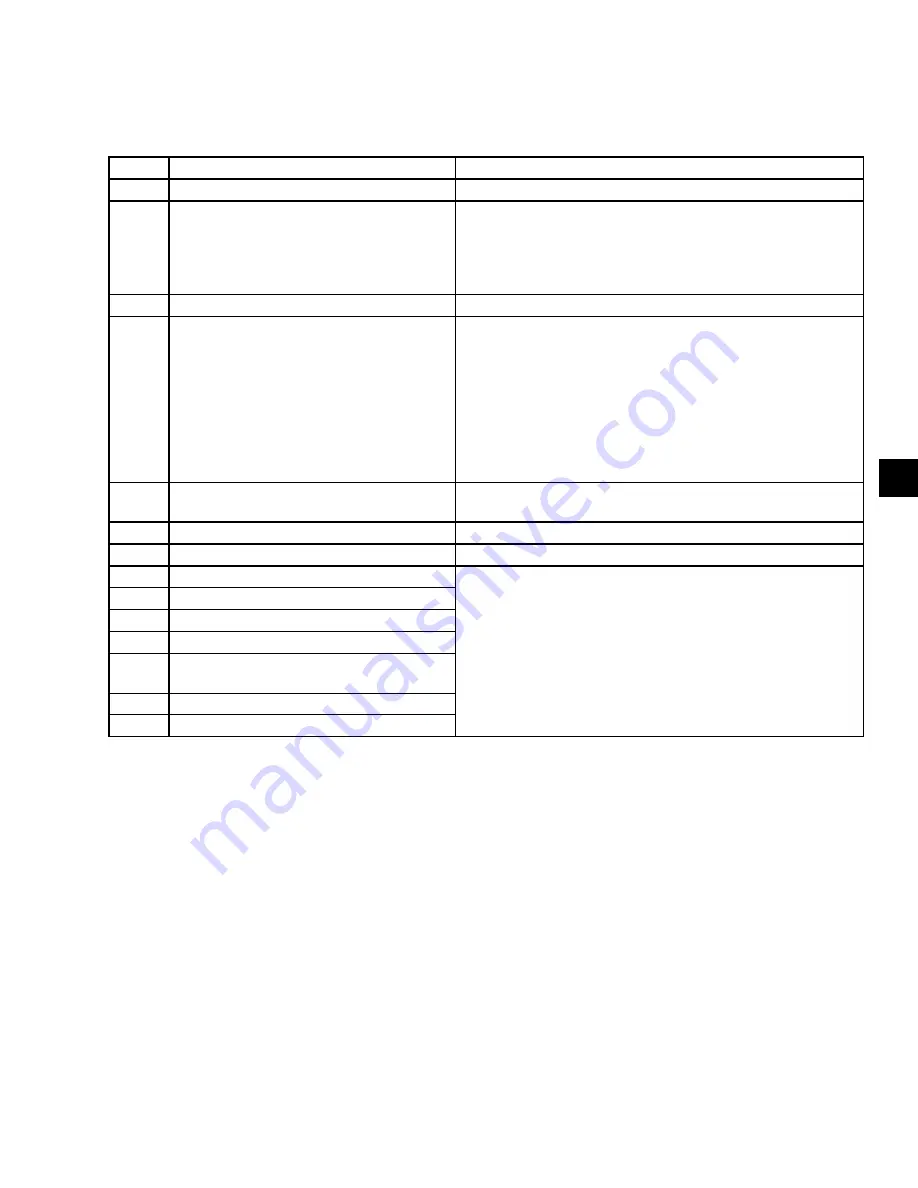
JOHNSON CONTROLS
159
SECTION 8 – TROUBLESHOOTING
FORM 155.30-ICOM2.EN.UL
ISSUE DATE: 12/21/2018
8
TROUBLESHOOTING PERFORMANCE
ISSUES
TABLE 44 -
TROUBLESHOOTING PERFORMANCE
ISSUES
ITEM
CAUSE
COUNTERMEASURE
1
Cooling water temperature is high.
Check the capacity of the cooling tower.
2
Cooling water is insufficient.
• See if the cooling water supply rate matches the specification.
•
Check the flow meter, discharge pressure of the cooling water
pump, current, and so on.
•
If the flow rate is insufficient, check the opening ratio of the flow
controller valve and check the strainer for clogging.
3
Cooling water heat exchange tube is dirty.
Contact your local Johnson Controls Service Office.
4
Non-condensable gas remains in machine.
• See
• Check the capacity of the vacuum pump.
• Check the purge unit for trouble.
•
Purge air from the absorption chiller. If partial-load operation is
continued for a long period, non-condensable gas tends to stay
in the absorber. In this case, purge directly from the low-pressure
side (absorber). See
automatic purge unit is installed, purge from the lower pressure
side (absorber) manually.
5
Chilled water outlet temperature controller is
not set properly.
Check that the chilled water outlet temperature controller on the
control panel by the machine is set to the target value.
6
Manual refrigerant blow valves are kept open. Check that manual refrigerant blow valve V8 is closed.
7
Refrigerant pump
Stop
button is pressed.
Press the Refrigerant Pump
Auto
button.
8
Corrosion inhibitor is depleted.
Contact your local Johnson Controls Service Office.
9
Surface active agent is depleted.
10
Refrigerant is dirty (contains solution).
11
Internal cycle control valve is not set properly.
12
Chilled water outlet temperature controller is
broken.
13
Solution is crystallized.
14
Air leaks in absorption chiller.
If the performance is insufficient while the hot water
control valve is fully opened or if the hot water control
valve does not fully open while the load is sufficient,
check numbers 1-7 in the above table in order. If the
cause of the trouble is other than numbers 1-7, it may
be one of number 8-14. In this case, contact your local
Johnson Controls Service Center immediately.